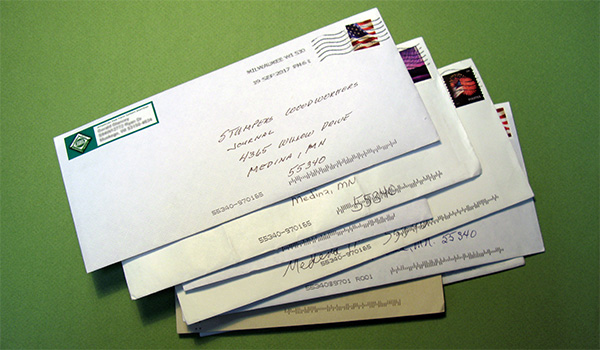
Here’s a sampling of the comments we received:
Not having a lathe didn’t prevent Don G. from completing a turning required for a project. After unsuccessfully trying “the old chuck it in the drill press routine,” he recalled seeing a decorative rope pattern created using a router in a jig that traveled down a spindle while the spindle turned. That process (using chains and gears) and the results were more ambitious that his requirements, but it inspired Don. His challenge was to figure out a way to keep the workpiece the correct distance above the bit and to figure out how to rotate it as it moved along the desired length. Getting more and more ambitious as he went along, here’s how he proceeded:
– He first cut two circles out of hardboard and attached one to each end of the workpiece … so that the corners of the square stock were about 1/4″ less than the circumference of the circles.
– He then adjusted the fence on the router table so the stock was centered over a 1/2″ straight cutting bit set to take about 1/4″ of material off the corners of the square stock.
– He clamped a stop block on both sides of the bit to limit the travel of the piece & so it wouldn’t cut too close to the supporting circles.
– He simply passed the stock over the bit, rotating it slightly with each pass and found that he was able to make a perfectly round dowel very quickly.
– Experimenting further, he was able to make a taper by changing the size of one of the circles.
– He was then able to produce a nice bead detail by installing a V-groove bit, setting the stop blocks so the workpiece couldn’t travel side to side, and adjusting the height of the bit.
Multiple, identical copies can be made by completing each step before changing the setup. Don got the best results from a single fluted 1/2″ Craftsman bit and his Porter-Cable plunge router.
JDM didn’t claim to be the inventor, but he described his use of a router to cut thin sheet goods … 1/2″ and less … such as paneling, mica, Corian, plywood, and hardboard. Since the router rides on the template surfaces, not on the finish, he avoids the splintering of edges and scratching of pre-finished panels common to saws. Here’s his setup:
– A set of T-square jigs (8′, 4′ lengths for starters) with a couple of “C” clamps.
– A set of templates for electrical boxes (single, double, light fixtures) that clamp (or screw) to the T-squares. (Note that the “square” part of the templates are usually only locating cutout templates.)
– Since doors, windows, and corners are not usually perfectly square and need to be measured & the T-squares are only useful as straight edges on longer cuts.
– A set of saw horses with a few 2″ x 4″s to hold the sheet level and prevent warping and twisting.
As with all good jigs, there are many other uses around the shop … dadoing, slot cutting, and mortising. And the T-squares make good guides for portable saws.
Obsolete equipment is sometimes referred to metaphorically as a “boat anchor.” Todd’s creative use of an old router makes that characterization close to reality! When he decided to hang his shop-built extension table (for a Delta 12-1/2″ portable planer) from the ceiling, he decided to use a block and tackle to lift it up. Three factors then came into play … Todd didn’t like the idea of having rope strung all over the shop to hold up the table … due to the physics of the setup, lifting only required 15-lbs of force and he possessed an old Black and Decker 3-HP, purchased without knowing that there was a slight bend in the shaft. After playing around with the router and a couple of chunks of added (epoxied) steel, he had the perfect counterbalance for the planer. A light push up on the router brings the planer table down within easy reach.
Locking an abrasive bit from a Dremel set onto his router, made it easy for G to sharpen an old fishing knife.
Ever try to route a dado in a dowel? Probably not, but that didn’t stop Kent H. To create a bottom shelf for an end table, he needed to insert some 3/8″ boards into the dowel. To pull this off, he made a jig that clamped the dowel into place, and then ran the jig along the fence.
Q&A
Shop-Vac Static
Cal thinks it might be time to consult with an expert on the topic of dust explosions (akin to the deadly grain storage explosions). Though he’s read articles (including ours) that indicate there’s no problem or only a small problem of static shock, he’s also seen claims that a static discharge in a commercial shop could knock you to your knees or worse!
Putting some water in a wet-dry vac tank, according to D.A. Clements, is another way to reduce static and catch more of the finer dust.
To avoid drawing a static arc (sometimes quite large), a reader suggested keeping one hand on a grounded metal tool while vacuuming sawdust off the floor & that way there’s no buildup.
Dave Dick wrote from the UK that the danger of static shocks should not be minimized. The surprise of getting a “wee buzz” while operating a spindle molder, he points out, can be highly detrimental to your finger! The remedy is to wrap what he calls an old-style earth (meaning ground, we presume) cable of 1.5mm or 1/16″ multi-strand copper around all plastic duct pipes and fittings and attach it to a known earth source. This source can be as simple as driving a copper pipe into the ground.
Robert R. Clough wrote to tell us about an article on the dust collection myth by Rod Cole. In the article, Rod indicates there is no danger of dust building to a dangerous, explosive level and that grounding was not required for safety, but only as a personal preference for eliminating all static.
Grounding a PVC dust system is a TOTAL WASTE of time, declares William Ryalls, who has seen no documentation of dust-collection static causing a fire or explosion in the United States. And he wonders why people keep telling everyone to run wires.
“Dry” Glue Is Gumming up Sandpaper
When his father-in-law had the same problem with gummed up sandpaper, Garrick wrote to tell us he switched over to polyurethane glue and has never looked back. Now, just three hours after they put in the clamps, they can sand it.
Made in the USA?
B.M. Ribler feels that instead of arbitrarily requiring that tools be made in America, the real issue is insisting on tools produced in a safe, humane environment where workers benefit from the enterprise. He pointed out that in many foreign countries, workers are forced to work sweatshop hours, in dangerous conditions, and are paid pitifully low salaries. Purchasing those tools subsidizes that exploitation, while tools made in America offer some assurance that they were produced under safe and humane conditions, and that the workers were paid at least a minimum wage.
Green Wood Turnings
Jim Locy suggested placing a green bowl in a black garbage bag filled with sawdust will help it dry with less cracking.
The Cost of Building Versus Buying Furniture
A contributor to the thread wrote to add a few points that he felt our summary missed:
1) The cost of buying tools should be amortized over several projects … but there should come a point when you can consider them paid for
2) Some of the cost of tools will be recovered when they are sold. Whether this is at an estate sale (presumably after you’ve made that final trip to the celestial workshop) or, a bit pessimistically, when you lose interest, there is always a market for used tools
Industry Interview
Cut-n-Sand: Simple and Smooth
With a Forrest blade on his compound saw, Rod Hansen wrote that he wouldn’t risk ruining a perfect cut by trying to simultaneously sand it.
Tool Preview
Mafell DD40 Duo-Dowel System
A reader thought the Duo-Dowel System was a great idea, but the price was too high … especially since he could get a good biscuit cutter for hundreds less.
Today’s Woodworker
Jill Biros: Finding Beautiful Bowls
As a new woodturner, Tim Morano appreciated our article on Jill Biros. He tries to absorb all the information he can get through books, articles, and stories like Jill’s.
Other Reader Comments
Jack Brewer took time to tell us how much he enjoys reading our eZine. From the copious notes he’d taken over the years, plus using some of our links, he was able to build a table for his wife (picture included). His advice to others: go slow and pay attention!
Speaking of turning, Neil Brown wrote to tell us about his invention. He uses a strobe light on his lathe that’s synchronized so the wood appears to be standing still regardless of the turning speed. This technique has allowed Neil to learn more about how his tools interact with the rotating wood, differences in wood characteristics, and how to better use what he called the “evil dreaded SKEW” … without having to turn the lathe off. To “turn” the piece, he uses a “pulse delay circuit” to delay the strobe and see a different side of the wood. (He wanted us to hear about it first from him … before the idea is stolen!)