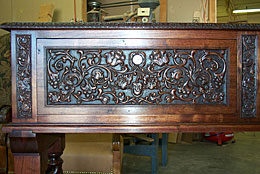
When a woodworker mentions that they also makes boats, one automatically imagines a 17-foot wooden sailboat with a glossy exterior finish and a teak interior. So when Kirt Kirkpatrick said he used to make boats, he had to explain that he used to make turbine powered, unlimited hydroplaning boats out of high density foam, honeycombed aluminum and a little wood here and there. The boat he worked on in particular was only the second turbine powered speedboat ever built and it set the world record for speed in 1981. More recently, he built himself a 17-foot tunnel hull, but he only put a wimpy little 200 HP engine on that one.
There’s not much call for boat building where he currently lives – Santa Fe, New Mexico – but he still likes challenges. Quite recently, a family commissioned him to create a table for an antique silver jewelry box that had been acquired (when someone acquires an antique, it means the piece was so expensive you don’t even want to know about it). Kirt is a skilled carver and furniture builder, but he decided to bring in the most talented woodworker he knew for this project: Joe Ihasz.
Kirt and Joe met back when they both lived in Kansas and they were both pattern makers. A pattern maker, Kirt explained, makes full-size patterns out of wood for metal castings. Then a sand cast is taken of the wooden pattern and used to cast parts for airplanes, presses, engines and all kinds of other things. The trick, Kirt says, is that the tolerances are so tight for metal parts that not only do you have to take the wood’s movement into account, you also have to factor in the metal shrinkage for aluminum, iron, steel, brass or whatever material you are casting. After everything is done, the tolerances have to be plus or minus one ten thousandth of an inch.
“It’s the most technical woodworking trade there is. If you’re a pattern maker for 50 years, like Joe, you’re the best,” says Kirt. Joe’s carving skills are truly amazing, so Kirt flew him out to look at the jewelry box. They took pictures and plaster casts of the box’s carvings, and Joe went back to Kansas to work on the carvings for the table.
The result was a carved table that exactly emulated the carving on the box, down to the tiniest detail. Says Kirt, “So when that jewelry box sits on top of this table, you’re going to notice that…and you’re going to know it’s one of a kind.” The whole piece is in walnut, and after Kirt and his team built the table, they disassembled it, sent it to Kansas, and Joe added his carvings to it. The table itself is about 4′ long and the drawer, shown here, is about 20 inches. What you can’t see, he explains, are the carving details in the background and in the spaces between the flowers; they are just too tiny to catch in a photograph. It makes sense when you realize that Joe sometimes grinds the eyes off sewing needles to make gouges for his really detailed work.
Working with and around antiques has become a niche for Kirt. For example, one family found a set of antique dining room chairs and hired him to create a matching dining room table. He did a lot of the carving on that piece and only brought Joe in to add the gargoyles.
A recent challenge for Kirt and his team (one person who does the basic furniture building and another professional finisher) consisted of 300-year-old Asian carved wooden screens. These are screens with vast carvings of landscapes in them including people, trees, mountains–all in intricate detail. He was supposed to use these screens and incorporate them into an entertainment center. That meant he had to cut them apart.
He wasn’t nervous about that in particular, but he says you don’t do something like that without a huge feeling of respect for the craftsmen that created the panels. “When they made these things, the joinery in the frames was all done by hand. They were amazing,” says Kirt.
So, after meeting with the audiovisual folks, he designed an entertainment center that was 7 feet wide, 8 feet tall and 30 inches deep. It is a unique contrast between the latest in technology and some of the oldest woodworking craftsmanship in the world.
– Bob Filipczak