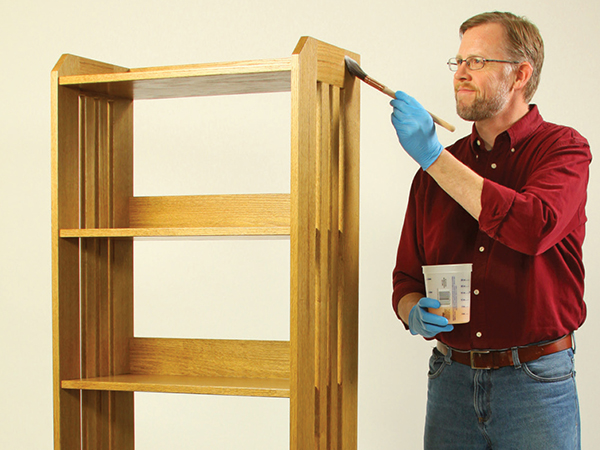
This step-by-step project video shows you how to build a classic oak bookcase. This bookcase can be built using dimension lumber that can be purchased at any home center. You only need a circular saw and router to build it, plus a way to make dowel joints.
This video is sponsored by Triton.
Tools Used in this Project:
Triton Plunge Track Saw
Triton 2-1/4HP Dual-Plunge Router
Triton Doweling Joiner
Video Transcript:
Chris Marshall: Hi folks, I’m Chris Marshall with Woodworker’s Journal Magazine. There’s always room for another bookcase, especially one that’s not too big and built to last, like this one is! Our version here loosely resembles Arts & Crafts furniture, with these slatted sides, a darker finish and an open design. It never goes out of style! And in this video, I’m going to show you how to build it
Now, if you’re new to woodworking, this is a great project, for a couple of reasons. First, we’ve kept the design pretty simple — and you can build it from pre-milled lumber you can find at any home center. I made this one from red oak. Here’s what you’ll need: three 8 ft. 1x2s, and four 8 ft. 1x4s. You’ll also need a 2-ft. x 4-ft. piece of 3/4 in. plywood for the shelves. Many home centers sell quarter sheets of plywood like this that are already precut, for convenience — and they’re called “Handy Panels.”
And if you don’t have a shop full of woodworking machinery, don’t worry about it. You’ll only need two main tools for this project — a circular saw and a plunge router. You’ll also need a way to drill dowel joints, because this bookcase has lots of dowel joints. I’m going to use this Duo Dowel Jointer from Triton Tools. It looks like a biscuit jointer, but it drills two dowel holes at a time. But, there are other options. You can also use a conventional doweling jig like this for most of this project. It clamps to workpieces so you can drill the dowel holes with a regular drill and drill bit. Oh, and one last thing: you can download the technical drawings and step-by-step instructions for this bookcase by clicking on the link in this video. Now, let’s get started!
Our first step is to mark and cut the bookcase’s four legs to length. What’s important here is that these crosscuts are square when you’re done. But when you’re cutting narrow workpieces like this, it can be hard to cut them to square accurately with a circular saw. And the narrower the workpieces are, the harder it is, because the saw base will want to tip off the workpiece, one way or the other. If you have a way to crosscut accurately with your circular saw, by all means, use it. But I’m going to use this simple, shop-made crosscut jig. It’s just a raised platform with a fixed fence on top that guides my circular saw across a cut. There’s enough room under the platform to slide 3/4-in.-thick workpieces into place for cutting. This base has another long fence along the front edge that gives me something to square my workpiece to. And there’s a clamp here to hold the wood securely so I can keep both hands on the saw. The jig is easy to build from scrap, and it will make all the crosscuts for this project quickly and precisely.
Measure and crosscut two 1x4s into four legs. Then mark and cut four side rails to length from another 1×4. If you don’t use a crosscutting jig like this, choose a cutting method that will make sure all of these cuts are square. The bookcase legs have these angled feet. And the tops of the front legs are clipped at 45 degrees too. Mark these cuts, and guide the base of your circular saw against a straightedge, or use a track if your saw comes with one, to make sure these angled cuts follow your layout lines.
Now that the legs and rails are cut, clamp them together into two side assembles of front and back legs, with rails in between, so you can measure the length of these inside spaces where the narrow side stiles are going to go. When you measure these spaces, measure them individually, just in case their length varies at all. Because depending on how carefully you cut the feet, they just might. Then carefully mark and cut two 8-ft. 1x2s into four stiles. Set the long stiles you’ve just cut into place. Now it’s time to mark for all the dowel joints. Here’s how those work.
These stiles are spaced 1 in. in from the inside edges of the legs and 3/4 in. in the middle. I’m using a spacer block here to hold their position. Mark both of them for a single centered dowel on top. The top rail here receives two dowels on each end, and they’re positioned 1/2 in. down from the top and 1-1/4 in. apart. And down here, mark the centers of the stiles, just like on top. This bottom rail also gets two dowels per end, but this time set the first one 3/8 of an inch down from the top edge, and then 1-1/4 in. below from there. And don’t forget to mark all of the parts on each of the bookcase’s side assemblies so that you’ll know how everything should go together. Mark the joints however they make the most sense to you.
At this point, we’re ready to drill all the dowel holes to put these side assemblies together! Set your doweling machine or doweling jig and drill bit to drill these holes just slightly deeper than half the length of your dowel pins. I’ve got my machine set to 13/16 in. because I’m using 1-1/2-in. long dowel pins. Be sure to test your setup on scrap first, like I’m doing here, to be sure everything is dialed in. Also, try to center these holes as close as possible on the thickness of the parts, for maximum strength. Now go ahead and drill dowel holes in the sides of the legs, the ends of the rails and the ends of the stiles. When you drill the narrow stiles, it’s helpful to clamp all four of them together to give your doweling machine or jig a wider, more stable surface to rest against. For the Triton Dowel Jointer I’m using, I also had to remove one of the two end mill bits from the tool so I could drill the stile holes one at a time.
CM: And when your dowel holes are bored, the next step is to dry-fit both side assembles together with the dowels in place. You want to make sure all of these joints line up properly and close correctly. Then pull everything apart and sand the inside edges of the legs, rails and stiles smooth — you won’t be able to reach these surfaces easily once everything is glued up. Sand them up to 180 grit.
Now you’re ready to put the side assemblies together! Spread glue into the dowel holes, insert the dowels and clamp the parts until the joints close. Be sure to glue the stiles between the rails first, and then add the legs. You always want to start on the innermost joints of a dowel assembly, and work your way out. And if there’s any glue squeeze-out around the joints, scrape that off when the glue gets rubbery. Then repeat the whole process to glue up the other side assembly. When both side assemblies are dry and out of the clamps, check all of the joints to make sure the parts meet flush. If they don’t, use a card scraper or your sander to flatten them. Then sand the side assemblies smooth.
Let’s cut the shelves to size, next. If you use a home center 2 x 4 “handy panel,” you can get all four shelves from one sheet. I’m going to use this track that comes with my Triton Track Saw, to guide these cuts. This will make sure your cuts are arrow straight. But if you don’t have one, you can use a straight piece of scrap stock or a metal straightedge clamped to the workpiece to guide your circular saw’s base.
The four plywood shelves fit into long dadoes here, that run across the bookcase sides. Think of dadoes like a three-sided channel that crosses the grain and fits around a workpiece, like this. Dado joints are strong with just glue alone, and they help to hold shelf assemblies square. But here’s the challenge: the long dadoes for our shelves have to be dead straight, AND they have to be just shy of 3/4-in. wide. That’s because three-quarter-in. plywood like this is almost always 23/32-in. thick these days. A standard 3/4-in. bit will cut a dado that’s too loose. So, here’s how I’m going to cut tackle both of those challenges: straightness and snug fit. I’ll be using a plunge router, equipped with a 1-in. outside diameter guide collar. It’s this silver ring, here. And I’ll be using a special undersized plywood-cutting bit with a 23/32-in. diameter, so it will cut the shelf dadoes just right.
And to make sure those dado cuts will be straight and right where I want them to be, I’m going to use this shop-made, slotted jig. The slot is 1-in. wide, so the router’s guide collar just fits inside it with no extra play. The advantage: there’s no way the router can drift off course as I cut the dadoes. Every one will be perfectly straight and exactly 23/32 in wide. And, on my jig I’ve tacked on this stop to keep my router from cutting too far. This stop block will limit the length of the dadoes to 11-3/4 in. long, which is the width of the shelf boards. That’s what I want. You can find simple plans online for making these slotted jigs like this. They’re super handy, especially if there’s no room for error, or if you’re new to using a router. I use them all the time.
Prepare for dadoing by laying the back edges of both side assemblies together, and marking their back legs for the four shelf dado locations. Now draw the dadoes, including their stopping points. Then, set your plunge router’s depth so the bit will cut to a maximum of 3/8-in. deep below the slotted jig. And here’s a tip: I’m fitting strips of scrap MDF between the stiles so the router bit won’t splinter the legs or stiles as it exits each of these pieces. But if you don’t have access to a table saw to cut these strips, you can also use a utility knife and just score the wood at your dado layout lines here, here and here. That works, too–it will help keep the router bit from breaking this fragile edge grain.
Now carefully clamp the side assembly and the slotted jig together on your workbench. Make sure the bit lines up exactly with your layout lines. Then rout each dado in three deepening passes at 1/8, 1/4 and finally 3/8 in. deep. Doing this in stages will produce cleaner dadoes with less burning and keep from overloading your router or router bit. When all the dadoes are routed, square up the rounded ends left by the router bit with a chisel and mallet. Then double-check that the shelf boards fits all the way up to the ends of the dadoes.
Since the sides of these bookcases are slatted, you can see the ends of these two middle shelves between the slats. And since these shelves are plywood, that means the inner laminations will show. We don’t want that, so we need to cover these ends. For that, I applied strips of this iron-on oak edge-banding. It’s just a long strip of thin wood veneer with hot-melt adhesive pre-applied to the back. So when you heat it up with an iron, it will stick to the wood. Just cut strips of edgebanding about an inch longer than the shelf ends, set them in place and iron them on with a household iron set to a medium/high Cotton setting. Press the veneer down with a wood block to improve the bond. Then trim off the overhanging ends with a sharp utility knife.
This tool has razor blades inside that trim off the overhanging edges of the veneer, so they’re flush to the faces of the shelf. It works really well. And while you’re at it, apply a strip of edgebanding to the back edges of all four shelves, too, so the edge plys won’t show up on the back of the bookcase. Now we can add a shelf back to each shelf. To do that, dry-assemble and clamp the bookcase together with the four shelves in their dadoes. Measure the bookcase’s actual inside span to determine the final length of these 1×4 shelf backs, before crosscutting them to length. Cut the three lower shelf backs, and make sure they fit in their openings.
This top shelf back is narrower than the rest, at 2-1/4-in. wide, so it can fit this space, here. It’s not a standard 1×2 or 1×4 width. So, if you don’t have a table saw, you have two options: One, you can have a friend with a table saw rip a piece of 1×4 to width for you. Or, you can rip it with your circular saw and straightedge yourself, but be sure to cut it from an oak board that’s wide enough to give your saw plenty of support underneath. A piece of 1×8, or even wider, would be a good idea. After giving the shelf backs a good sanding, now I’m laying out three pairs of dowel joints to attach these parts. Here’s where this Triton Doweling Jointer will be really helpful — it can drill dowel holes into the bottom edges of these shelf backs, as well as drilling into the faces of the shelves. Not all doweling jigs work as well as this does for face drilling applications.
Drill holes for the dowel joints, but be careful: this time you only need the holes in the shelves to be drilled about 5/8-in. deep. Be sure to reset your doweling tools for shallower holes. I’m drilling the shelf back holes to 5/8-in. deep too, then using shorter 1-1/4-in. dowels for these joints. Now dry-assemble the bookcase and glue the shelf backs onto their shelves with dowels in place. This way, you’ll know that the shelf backs are in exactly the right position on the shelves so the bookcase will fit together correctly. Clamp these joints until the glue dries.
The front edges of the shelves will get some solid-oak edging to hide these edge plys. This front trim helps to stiffen the shelves, and it also makes a durable wear surface against dings and scuffs over time. With your bookcase dry-assembled, measure each of these shelf lengths, then crosscut strips of 1×2 to fit them. Spread glue along the front edge of each shelf, and install its trim strip with the bookcase still dry-assembled. Clamp the trim strips in place until the glue dries. Then scrape, plane or sand the trim strips flush to the faces of the shelves, but be careful not to damage the plywood face veneer — it’s very thin!
Right now, these trim strips on the shelves are twice as wide as they should be. So, use your circular saw and a straight-edge to rip them to 3/4-in. wide instead. We’re almost ready to glue this bookcase together for the last time, but there’s one more machining step. I used my router and a chamfering bit to soften as many sharp edges of the project as I could — around the side assemblies, along the front edges of the shelves and the shelf backs, AND in between the stiles. This bit of detailing will make the bookcase more pleasant to touch and make the project stand up to wear and tear better over time.
The chamfers on the stiles also add some nice shadow lines here, and they help make the sides of the bookcase look a little less flat and “cookie cutout.” I made them larger than the rest of the chamfers, at about 1/8-in. wide. When you’re done routing them, these corners will be left round from the router bit. So square them up with a sharp chisel. Sand the chamfers smooth, then go ahead and glue the shelves into their dadoes and clamp the whole bookcase together. Let the joints dry overnight.
You can stain and finish your new bookcase however you like. I used a medium-brown stain, and now I’m brushing on three coats of a clear finish. I think you’ll find that this is a fun and useful piece of furniture to build, and it will give you some good practice with your circular saw, router and doweling techniques. To learn more about the tools you’ve seen in this video, visit tritontools.com or a Rockler store near you. So I hope you’ll give it a try! And thanks for watching.