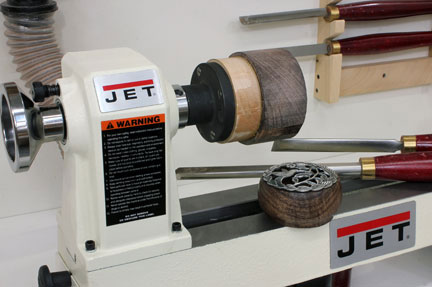
How to turn a simple faceplate that will offer solid, secure support for a variety of woodturning projects.
Of all the ways to mount workpieces on the lathe, few are as simple and versatile as a faceplate. You can attach a faceplate directly to a turning blank with screws, and that works fine for large bowls with thick bottoms where the screws won’t interfere with turning. That’s also a quick way to attach a blank and turn the outside first before flipping the blank and remounting it in a lathe chuck to do the inside — again, a method better suited to large projects. However, for smaller work like the lidded bowl featured here, coupling a faceplate with a glue block is the easiest way to go.
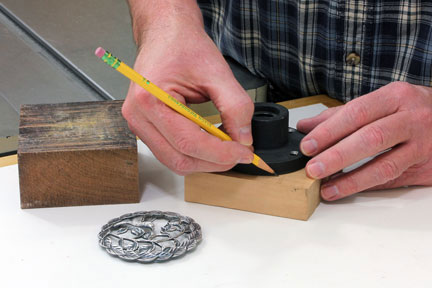
STEP 1: Select a piece of solid wood scrap (not plywood) at least 1″ thick, making sure that both faces are flat for secure attachment. The faces should also be perfectly coplanar, or you’ll end up with a lopsided turning. If in doubt, run the scrap through your planer before cutting it to size. Trace around the faceplate onto the scrap as in Photo 1. I like to make this tracing slightly larger than the plate by maybe 1/8″ to 3/16″ to allow a bit more material to work with. A bit of extra stock also helps prevent splitting when we drive in the screws later.
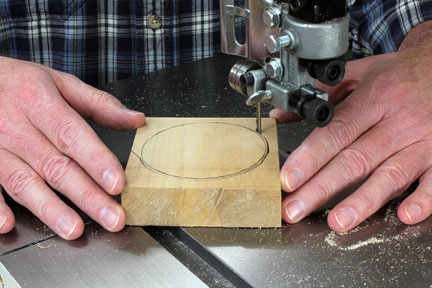
STEP 2: Move over to the band saw and cut out the glue block (see Photo 2). You’ll notice here that I’m going a bit larger than the tracing; I want to allow a bit of extra working stock for truing up the block. No need to sand these cut edges.
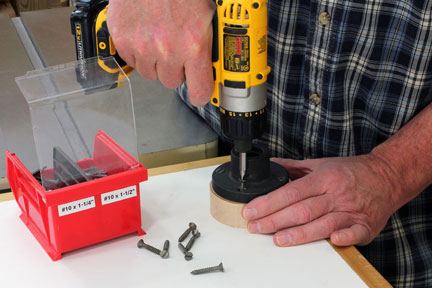
STEP 3: Drill pilot holes into the glue block and attach it with screws (see Photo 3). Select screws that will penetrate the glue block to a depth of 3/4″. It’s best to use a heavier gauge screw — not only will the threading hold more securely, but you don’t want any “wiggle room” in the screw holes in the faceplate that could allow the glue block to shift during turning. For my 1/2″-thick faceplate, #10 x 1-1/4″ screws work perfectly.
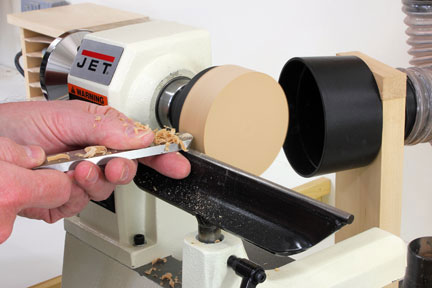
STEP 4: Mount the faceplate/block assembly on your lathe and true up the block as in Photo 4. It’s common when driving the screws for the faceplate to sit not quite center on the block. By giving it a quick turning to true the block, it will keep everything balanced on the lathe when we’re turning the project itself. When truing, take only enough material to get it perfectly circular.
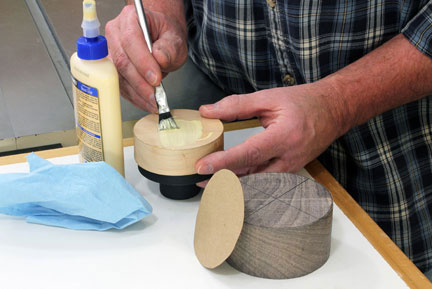
STEP 5: Now it’s time for the glue-up (see Photo 5). Start by spreading glue evenly onto the face of the block. Press a circle of paper onto the block, and then spread glue evenly on the paper. Finally, center everything on the back of your turning blank and press it firmly in place by hand. That piece of paper won’t affect the solidity of the glue-up, but when it comes time to remove the final turning, it’ll make the task of separating the turning from the block much easier.
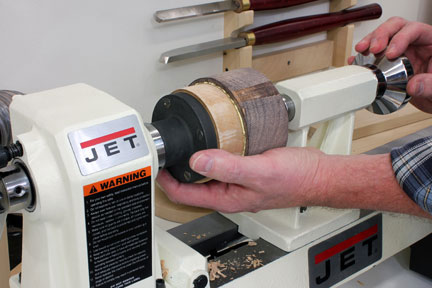
STEP 6: For a secure bond, the faceplate/block/blank assembly must be firmly clamped. You can do this with regular clamps — which I do if I’m making up additional blanks while my lathe is otherwise occupied — but if you’re only working on one project you’ll find it efficient to use your lathe. In Photo 6, I’ve mounted the faceplate assembly onto the lathe and brought up the tailstock, then cranked the center into the workpiece with enough pressure to convert the lathe into a very effective clamp until it dries.
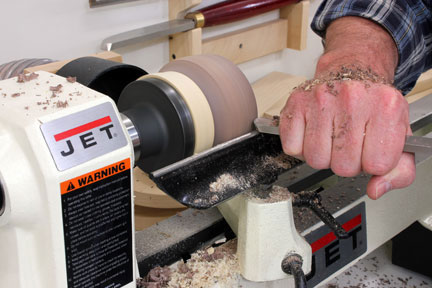
STEP 7: Once the glue-up has dried thoroughly, go ahead and make your turning (see Photo 7). Note here that I’ve used the chisel to cut right into the front edge of the glue block. Since I made my glue block slightly oversized, this is perfectly fine as long as you remember that those screws extend 3/4″ into the block. For a 1″-thick block like this one, I’m careful to cut only into the final 1/4″ near the workpiece.
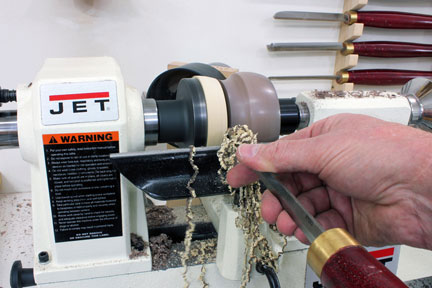
STEP 8: With the turning complete, you can now prepare to separate the turning from the glue block. In Photo 8, I’m using a parting tool to cut a groove right at the glue line between the block and turning that extends about 1″ deep. At this point, you have a few options. You can cut through the remainder with a hand saw while the assembly is still mounting on the lathe. Or, you could remove the assembly, and tap a chisel into that groove to finish the separation. However, for a small bowl like this I’ve found that after cutting my groove I can just snap it loose by hand with a gentle twist to the side while still mounted — the paper fibers separate cleanly to release the turning.
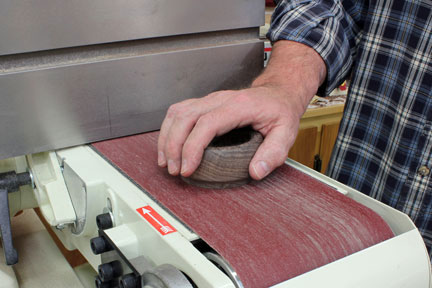
STEP 9: To remove the last bit of paper fibers and glue from the bottom of the turning, a few seconds on a belt sander does the trick (see Photo 9). All that’s left now is to add the finish of your choice, if you didn’t already do a friction polish on the lathe. For this lidded bowl, I chose several coats of rubbed-in boiled linseed oil, followed by a nicely buffed coat of wax. A pewter lid tops everything off beautifully.