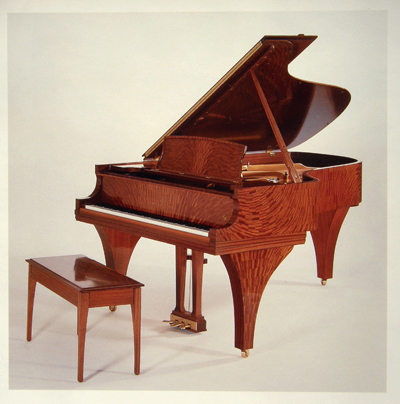
As we reported a few weeks back, building a piano from the ground up is a significantly daunting task. But what if you just want to work on a piano that someone else builds?
Tom Schrunk got an opportunity to do just that. After seeing an article about Frank Pollaro and the work he did on a Steinway and Sons piano, Tom contacted the company. He wanted to take his unique brand of veneering and apply it to one of the company’s “Art Case” pianos. Maybe it was his ability to do veneering projects that others wouldn’t take on or just his convincing manner; whatever the case, Steinway and Sons took him up on his offer and had him feature his work on one of their pianos.
The result is a work he calls “Reflections” (though it may need to be renamed Reflections One). It’s a checkered pattern of pomele sapele veneer that covers every surface of the Steinway. There are some solid pieces of pomele sapele, too, but most of it is veneered.
Tom’s unique view of woods and veneer centers around the concept of luster. He loves a wood’s natural luster and loves to play with it in different lights and patterns. That’s why his pattern in this piano is so intriguing: the more you look at it, the more you see. “I want it to be interesting from every angle, and I want it to be changing from every angle,” says Tom. He’s gotten so good at thisinterplay of veneer, luster and light that he can actually imbed pictures in the work that you can only see from certain angles if the light is right.
We mentioned earlier that this piano might be renamed Reflections One because Tom just got finished doing the veneer work on another piano for Steinway and Sons. This one will be done in a bloodwood veneer and, says Tom, the effect is just stunning. He hasn’t seen it on the piano yet, but the bloodwood veneer he found at a local lumber store totally floored him.
Steinway obviously likes working with Tom and he certainly likes working with them. “This is just a dream. The people at Steinway are just incredible people to work with,” he says. All of the assembly of the piano takes place in the company’s factory in Queens, NY, and they brought him in to watch how it works. As a woodworker, Tom was amazed at the scale of what they accomplish at the factory. It takes 11 months to make a Steinway, and the factory builds about 2,400 pianos every year. Some of the jigs he saw were works of art in their own right. Steinway knows “every trick in the book; they’ve tried it and they’ve made use of it,” he says.
The rim that his veneers are applied to consists of 16 pieces of rock maple, glued together and bent into the familiar double hump horseshoe shape that is the center of the piano. The lid is made of a special plywood that Steinway has developed over the years. For his part, Tom gets the dimensions of all the surfaces on the piano and tapes together the appropriate veneer sheets so the company can add them to the piece when it’s ready. “For it to be a Steinway,” says Tom, “it must have all Steinway components and they must control the assembly process.”
There are three varieties of the piano in the Steinway pantheon. The black lacquered piano is the most familiar — it makes up about 90 percent of the company’s inventory. The second type they call the “Crown Jewels.” Those are natural veneers of either walnut or rosewood. The third type of pianos are the “Art Case” pianos like Tom’s. Those pianos go on nationwide tours, and two have ended up in the White House.
– Bob Filipczak