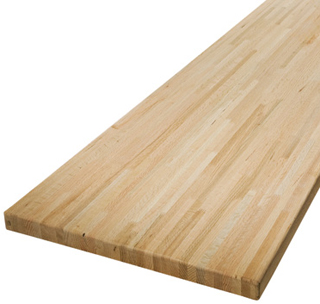
My son has asked me to build a butcher block countertop for the new kitchen in their newly remodeled home. Will build it out of soft or hard maple. It needs to be 50″ x 90″. Question: on a top that large, is it appropriate to build it in 12′ – 13′ sections that then are glued together for the final phase? Also, how thick does the butcher block top need to be? I’ve seen plans that look to be about 1″ or 1-1/2′ thick. It has been suggested that the top should be 2″ thick because of the large size. Should that contribute to the thickness of the project?- Doug Selfe
Rob Johnstone: Most modern kitchen cabinets are constructed so that a 1-1/2″ countertop will put the work surface right at 36″ from the floor. That standard work height is the compromise the industry came to for the “average” person. With that said, I put cabinets into an NBA player’s house one time and we lifted the work surface up to 40″ — of course, he had a tall wife as a partner. Although it is entirely subjective, I would suggest 1-1/2″ thick counter unless you have a big reason not to do so. We are used to seeing countertops of that thickness and any significant variation will draw attention to the counter. Which could be good — if that is your goal.
From a purely functional point of view, it makes no difference if you use hard or soft maple; the countertop will perform equally well.
Now to the question of the 12″ or 13″ sections … I am guessing that what you mean by butcher block is not the ultra traditional end grain presentation, but simply gluing long strips of solid maple together to form a solid wood countertop. If you are doing the latter, then by all means, glue up sections that you will be able to run through your planer — and in that way get flat level tops and bottoms to the panels. To make your final task of gluing the panels together, take care that all the pre-glued-up panels are the same thickness: it will make the final glue-up a bit easier.
Tim Inman: One man’s butcher block is another man’s (or woman’s) idea of just another wooden workbench top. There are differences in definition. Traditionally, a “butcher block” was made so the end grain was the working surface. This involves gluing up thousands of little blocks to get the end product on a job like yours. Expansion and contraction is the enemy, and the “force majeure.” The top made this way will be stable in the vertical dimension, but it will swell and shrink like crazy in the horizontal directions. A lot, and often.
Most often, the “butcher block” countertop is actually wood pieces laid up with quarter cut wood, so the swelling and shrinking is directed more to the vertical dimension, like an old-fashioned wooden porch floor, making the counter more dimensionally stable along the horizontal dimensions.
Either way you make it, dimensional stability is your goal, and your worry. Making small workspace-sized pieces that can insert into a visually pleasing frame system that will tolerate some movement is a great idea.Whatever you do, allow for wood movement so you won’t be disappointed a year or two after the installation.
Chris Marshall: I second Rob’s advice to glue up the countertop in smaller sections, flatten them and then join the flattened blanks into a larger countertop. I actually do that with any large panel I need to glue up. The fewer wet glue joints and clamps you have to grapple with, the better!