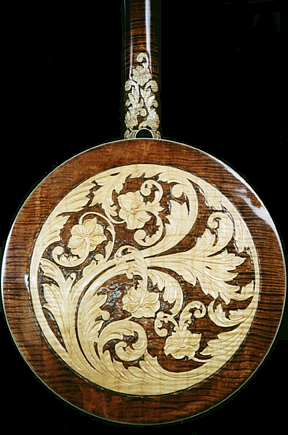
“I’m actually an artist. The banjo is my canvas,” says Bob Flesher, a professional luthier who specializes in some of the coolest banjos you’ve ever seen. His banjos range from authentic minstrel banjos that sport few decorations all the way up to modern banjos that include carved necks, elaborate wood carvings on the resonator and marquetry on the rim of the head. It’s all part of Bob’s evolution, from banjo player to banjo maker to artist, that has taken him in a lot of different directions.
It all started with the Andy Williams Show. Bob was the banjo player for that TV variety show for a year. While he was doing that, it occurred to him that his plain old banjo didn’t really lend itself to national attention. So he went in search of a fancy banjo only to find that no one made them anymore. Or almost nobody.
He finally tracked down a skilled banjo maker named Gariepy in Long Beach, California. Gariepy’s Banjo Company made the kind of instruments Bob was looking for, and he ended up opening a shop that sold these banjos. His friendship with Gariepy allowed him to learn banjo making ? – how to make the necks, how to work with the resonator, how to do the metal engraving and how to build the peg board and fingerboards and do the pearl inlay. The whole package.
Then Bob went to work for Eastern Airlines as a pilot for 22 years. The whole time there, however, he kept his passion for banjos alive through Liberty Banjo Co., a Connecticut-based firm he started. Later he moved to Atlanta, making banjos part time, and finally he landed in California where he now pursues the craft full time. He’s ready to retire right after he fills the orders for the 46 banjos he’s agreed to make. He can make about two banjos per month, so job security isn’t an issue.
Bob mostly works with curly maple. That’s a traditional material for banjos, he says, as is walnut. For a time in the 1800s, Brazilian rosewood was also popular, explains Bob.
He knows his banjo history, too. He explains how the banjo came over with the slaves from Africa and how the early ones in America were cut from gourds, with possum or cat skin heads and horsehair strings. The early banjos (or banjies or banjars or marywangs) sound very different, he says, having recreated some of them with the original materials.
The instrument was popularized by Joe Sweeney, Bob explains, who learned how to play from local slaves near the Appomattox courthouse. Sweeney is also credited with adding the fifth string: all the early iterations were four-stringed instruments.
One of the traditions of the banjo, Bob explains, is that it has almost always been highly ornamented. That’s the result of its popularity in minstrel shows, where the instruments became more and more gaudy as the shows became more and more popular. Few instruments, he says, aside from a piano here and there, have a long tradition of being both musical and decorative the way banjos have been.
So Bob has taken up the craft to make banjos as beautiful as they can be. In the case of the Jubilee, he has carved extensive designs on the back of the resonator, using a four ply maple veneer. The top layer is curly maple, and he carved through that to the next layer of plain maple. This gave the carving some depth, but it also allowed him to do some very selective staining on the lower layers of the veneer. This, says Bob, really makes the carving jump out. In the past, all of this design would have merely been painted on the instrument. The marquetry is a rope pattern that he orders from another artisan and adds to the banjo’s head.
In most cases, banjo makers will ship some of their work out to others, but Bob does all the work himself, including all the metalwork and hardware. He does a layered veneer design on the fingerboard, alternating gaboon ebony and a red dyed veneer. He also does all his own inlay, most of it in mother of pearl. He carefully lays out the pattern and cuts the pearl with a tiny jewelers saw, usually cutting it two at a time for the symmetrical designs that are popular on banjos. Then he carefully routs out the spaces and inlays the pearl. Later he etches it to create shadow effects.
The myth of inlay, he says, is that when it’s done right you can’t even tell where the seam between the wood and the inlay material is. “You’ve heard people say that ‘I’ve seen inlay work so perfect that you couldn’t even see the crack.’ Well that’s because they didn’t know what they were talking about,” says Bob. He uses a black epoxy for inlay so it both adheres and fills in the surrounding cracks, making them invisible.
He still often gets a chance to play the banjo. Bob runs a side business called Dr. Horsehair Music Company where you can hear him play on the CD he sells. The music company also sells instruction books and banjo supplies. If you’ve like to hear Bob play an old banjo from the 1850s-complete with cat skin head and horsehair strings-click here.
– Bob Filipczak