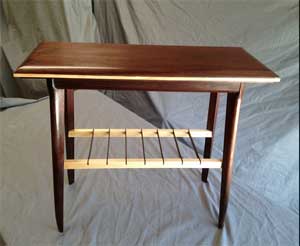
Ted Golbuff is a woodworker who has also designed studio furniture for a public radio station. That kind of furniture requires “bass traps” meant to absorb low frequency sound waves in order to improve acoustics. “One of the popular ways to do bass traps is with slats,” Ted said. “I’m influenced by a lot of slats in what I do — I’ve always been interested in parallels.” For instance, he’s done some shoji screens, and some of what he calls “hockey stick furniture.”
Some of that material, such as maple slats, might come from contractors’ castoffs. Starting a couple of years ago, “With the economic crisis, contractors were doing what they could to make ends meet” — which meant that Ted could find some of their supplies on eBay and Craigslist. “I’m trying to keep costs as low as I can, to sell to people who couldn’t normally afford” the types of pieces he builds, he said.
Also, Ted said, “I’m in a neighborhood that loves recycled things.” In his building, that might mean redwood from an old fence turned into a side table, or tiles turned into tabletops or planter stands. Another recycled fence turned into a screen cover for an air conditioner compressor. “I put stained glass panels in it so it’s real interesting, rather than real mechanical,” Ted said. Or, since Ted originally got started in woodworking due to repairing and making things — tables, trays, etc. — for his boat, and has continued to work a lot with teak, recycling might mean using the extra teak from his saw cuts to create serving trays or plant stands.
He has also built a client a dining room table using “zip-code based wood” from Wood from the Hood, a Minneapolis-based urban lumber reclamation program, and has a pending project for the same client from a tree they had taken down in their backyard. “For me, that’s the classic example of something that has a story,” Ted said. “You can say, ‘This was in our backyard, and show pictures of the tree before it was cut down.'”
“I try and expand every time I do something: try a different joint or technique, think outside the box: challenge myself,” Ted said. He does admit, however, that some projects are “about buying special tools” — and that he has specifically taken a class at a local college in order to have access to their larger machines.
Working in a one-car garage (the car now lives outside), Ted faces space challenges which, he says, make cabinet type projects difficult. He sees the purchase of tools for that shop as investments. For instance, Ted said, “I’ve done a lot of sewing in the past, so I bought an expensive commercial grade sewing machine. It’s paid for itself many times over, since it will sew whatever I run through it” — such as leather, for covers for the outdoor benches he makes.
His most recent specifically woodworking tool acquisition was a track saw. “I think it’s the best thing since sliced butter,” Ted said.
As he makes projects with that saw, “I strive for multipurpose: if I can get some device to do more than one thing, that’s always my challenge,” Ted said. Portable redwood panels with stained glass insets are more than yard decor for one photographer client: they also serve as movable backdrops for outdoor photo sessions.
Another challenge Ted has set for himself is to use as much wood as possible — ideally, using up the entire piece of wood. He demonstrated this ideal in a “Surfboard Table” project: the table, made from hackberry wood, is shaped like a surfboard. Ted used the portions of the “tail” that were rounded off to create that shape to create the table’s legs, and a tray with additional scraps. “I essentially used every piece of the wood,” he said.
When it comes to woodworking, “for me, it’s about a full-time career, and a full-time discipline,” Ted said. “It really makes me excited when I see happy customers.”