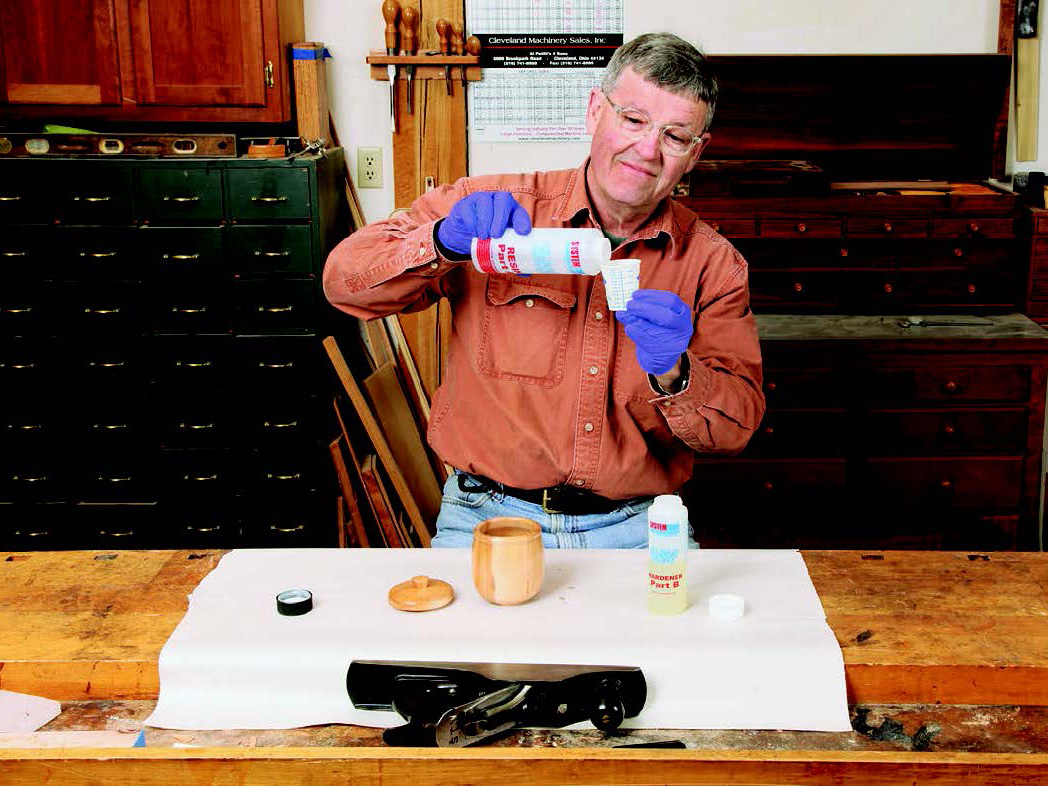
The finishing of turned work, be it bowls or treenware, presents special problems in terms of how the finish performs. The perfect finish for such items would have these following qualities:
1. Easy to apply, can be wiped or brushed on.
2. Protects the object during use and subsequent washing.
3. Nontoxic during application and once dry.
4. Brings out color, grain and figure of the wood.
5. Yields either a matte low luster finish or a mirror-like “piano” finish.
6. Tack dries quickly so dust in the air does not get trapped in the wet finish.
7. Easy to repair.
8. Sands easily between coats and does not clog sandpaper.
9. Odorless during application and drying.
10. Clear once applied and non-yellowing with age.
11. Unused portion stores without degradation.
Traditionally, oil finish is the finish of choice for bowls and treen. Non-polymerizing or slowly setting oils are the choice when the finish must be assured food-safe. Choices are mineral oil or vegetable oils, such as olive or walnut oil. These are easy to apply, give some protection, are food-safe and bring out the color in the wood — but are only low luster. They are easy to repair (just wipe more on), but they attract dirt with use so they don’t stay clear. They store indefinitely.
The quality that gives such oils both their good and bad properties is that they have no ability to polymerize. The best choice is walnut oil, which has some ability to polymerize but not to a very hard coating. It also hardens slowly … on the order of three weeks.
Raw linseed oil does form a hard film but also takes a long time. Traditionally, it was thermally treated by boiling, which increases its ability to polymerize, albeit to a yellow coating. Today, a better “boiled” linseed oil is made by adding a catalyst to cause polymerization — usually a heavy metal, which is toxic if ingested. Tung oil, which is extracted from the nut of an Asian tree, is also an oil that can be catalyzed and gives a much clearer finish than linseed oil does but takes many coats to build.
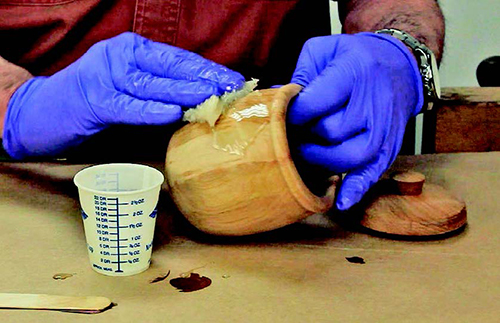
A harder finish can be obtained from so-called oil finishes sold commercially. They are either linseed and/or tung oil mixed with a varnish that wipes on easily. These varnishes are usually alkyd resins, which are polyester resins polymerized with natural oil, usually soybean. The resins are very thick by themselves, so they must be thinned with solvent to make them easier to apply. They dry really hard in about 24 hours, but they give off a lot of VOC (Volatile Organic Compound) vapors during application and drying. Application is a smelly process that can get you thrown out of the house. You can make your own by mixing equal amounts of linseed and/or tung oil, varnish and mineral spirits. Since all of these products have a propensity for spontaneous combustion, it’s bad shop practice to leave oil on rags for too long, as they can actually catch on fire from the heat oxidation reaction.
One huge disadvantage of all boiled linseed and tung oils, as well as any varnish, is that once the can is opened the finish will cure quite rapidly. The more air space and the warmer the storage area, the faster it will polymerize in the can. Since small amounts of finish are used in a turner’s average finishing session, this is a thorny problem. I have disposed of as much, maybe more, finish as the amount that I have used over the years.
A Problem Solved
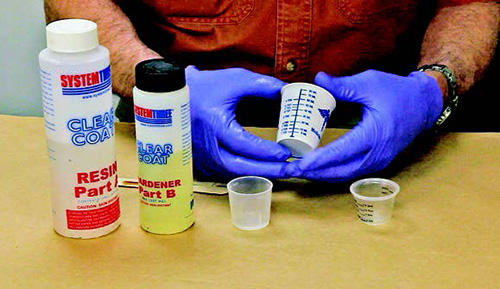
It was therefore with some excitement that I learned of a clear epoxy finish from System Three that was easy to apply like oil, had no VOCs and no heavy metal catalysts. Called Clear Coat, it is a two-part epoxy that has a long pot life but dries tough and hard. Although it tack dries in a couple of hours, full curing takes 72 hours. The long drying time is about the only drawback over oil finish. Second coats seem to dry faster than the first coat and temperature plays a big role. You need to keep the work at 70° for timely curing; however, higher temperatures speed things considerably. There is a halving of curing time for each 18°F, so 80° makes quick work of the process. If you must finish in a cold shop in the 40° to 60° range, System Three offers Turbo Cure, which reduces curing time to normal.
Exposure to bare skin of mixed or unmixed material should be avoided, for some people have an allergic reaction to epoxies. Also, it is very difficult to get off your hands, so I wear disposable nitrile gloves during all mixing and application. Unlike oil finishes and varnishes, which have a strong smell, Clear Coat has almost no odor at all. This is because it has no organic compounds vapors. I have applied it at my kitchen island on winter nights when the shop was oh-so-cold.
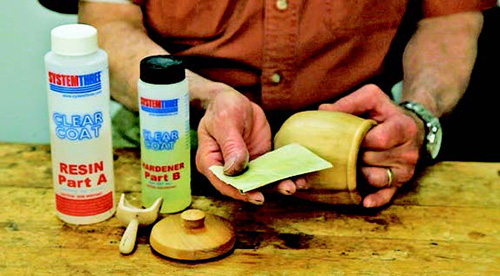
A huge advantage of Clear Coat is that very small amounts can be mixed as needed, and the unmixed product has an indefinite shelf life. I do take care to carefully wipe the threads of the bottles off with a paper towel before resealing or the lids become reluctant to unscrew. I have successfully mixed as little as 1.5 teaspoons but normally mix 3/4, 1-1⁄2 or 3 ounces. You must mix accurate proportions of one part hardener to two parts resin, and the easiest way to do this is with a dose cup. This is a transparent paper drinking cup with graduations in both metric and avoirdupois. Dose cups can be purchased from System Three, at woodworking stores or at good drugstores.
You can also purchase wood tongue depressors for mixing but, being the frugal woodworker, I fish sticks out of the scrap bin.
Application can be by brush, but I prefer to wipe Clear Coat on with a 2″ square of cloth towel. The environment should be as dust-free as possible. I soak the square with finish and wipe liberal amounts onto the work. I wipe on more finish as it soaks in, which also takes care of any holidays (bare spots). After about 10 minutes, I wipe off the excess with clean paper towel, using new pieces as they become soaked with finish.
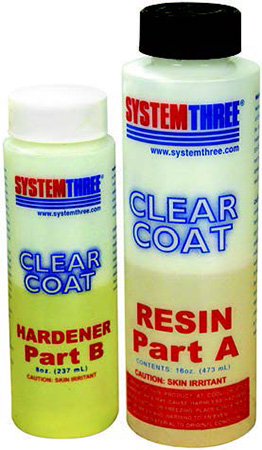
I have found sanding beyond 180-grit for the first coat is counterproductive. Prior to subsequent coats, I sand with 220-, 320- and 400-grit respectively. I have never had to put on more than four coats, and generally two or three do nicely. One of the best qualities of Clear Coat is its sand ability. It sands easily, leaving a white powder that does not clog sandpaper at all.
Conclusion
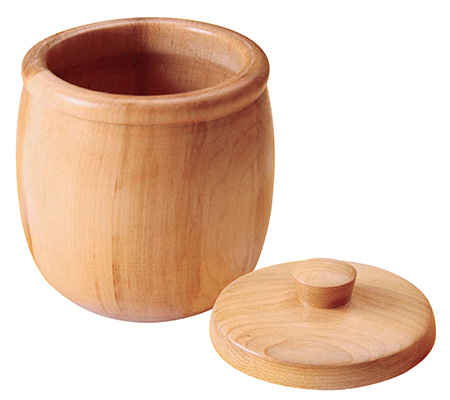
Of the list of eleven characteristics of a perfect treenware finish I provided at the beginning of this article, Clear Coat only comes up short on being nontoxic during application (possible allergen only) and drying quickly.
On the other side of the ledger, Clear Coat is the most durable finish I have found to date by any measure available. As an endurance test, I’ve actually run two test bowls through the automatic dishwasher on the pots and pans cycle five times with no discernable impact.