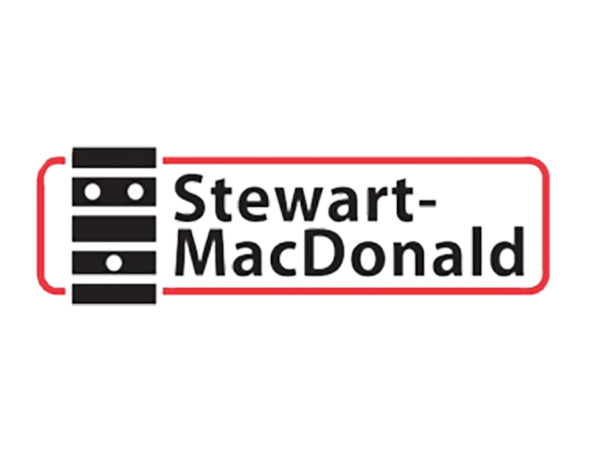
Have you ever had a hankering to build a guitar, banjo, or mandolin, but were at a loss as to where to begin? If so, do what the professionals do. Head on out to Stewart-MacDonald, the nation’s largest and best-known supplier for both professional and amateur “luthiers,” the term used to describe stringed instrument builders.
Known affectionately in the industry as Stew-Mac, both the store in Athens, Ohio, and the extensive website house a dizzying array of parts, wood, tools, accessories, instructional materials and a host of specialized items that only they offer. In short, you will find everything you need to make or repair musical instruments offered by a company that’s been keeping luthiers happy and productive for almost four decades.
The company was initially created by Kix Stewart and Bill MacDonald in 1968 to make and sell banjos. Stewart had a music store in Athens, Ohio, and MacDonald came in for repairs. They started a friendship and decided to build banjos together. Troubled by the fact that there was not a good banjo head on the market, they worked with a drum head manufacturer to develop what became their Five Star banjo head. It was their first product outside of banjos. They took the heads to music festivals, peddling them and other banjo parts. It wasn’t long before Bill realized that they were making more money selling parts than banjos.
The two expanded into selling complete banjo kits and were soon the happy victims of serendipity; the release of the movie Deliverance added a big shot in the arm to them as well as the rest of the banjo-loving world. At the same time, one of their suppliers, Waverly, who made banjo tuners and hardware, decided to sell out. They bought the company and moved it to Athens. Today, both men live in Bozeman, Montana. Kix, who is semi-retired, owns the company, while Bill consults for his old partner. The Waverly company has also made the move to Bozeman.
Stew-Mac continued to grow like Topsy, adding employees as needed. To hear company president Jay Hostettler tell it, these employees are responsible for making Stew-Mac so unique. In the late seventies, with about a dozen or so employees, they changed direction and started hiring experienced musical instrument builders. “That changed the face of the company,” Jay told me. “For example, hiring a mandolin maker got us into selling mandolin parts.” When Dan Erlewine, considered to be the most famous guitar repair person in the world, came on board in the mid eighties, his presence was the catalyst to get them not only deeper into repair tools, but into developing specialty tools as well. Today, the repair tools are the heart of the business, and they sell upwards of a hundred unique tools that they have developed.
One example, and one that has been adopted eagerly by woodworkers well outside the field of guitar repair, is their Precision Router Base (item 5260) designed for a Dremel tool. “We noticed that the normal base is not precise enough for inlay work,” Jay explained, “so we developed one with precise adjustments for height, as well as having better visibility and control. It also sports a dust blower.” Another tool, at the other end of the specialty spectrum, is their Erlewine Neck Jig (item 5252), designed to hold an unstrung guitar to simulate how it behaves under normal string tension. While this may seem obscure to woodworkers, luthiers know that the best way to finesse the fingerboard surface is to do it while the guitar is strung up. Unfortunately, the presence of the strings prevents working on the board under them. This jig allows for just that.
These days, some 55 employees handle more than 2500 items, selling everything from a single piece of fret wire to an entire kit to build an instrument, along with all the tools you’d need for the job. Perhaps even more important, they act as an invaluable source of information. “We pride ourselves on the fact that we answer all phone calls and e-mails,” Jay informed me.
Their customer-friendly policies led them into yet another avenue of product development. “Through tracking all the questions that came in, we concluded that there was a crying need for better instructional materials,” Jay explained. “At first, we produced general information videos called ‘Shop Talk.’ They touched on a wide range of subjects, but the feedback on them convinced us to produce more specific ones on techniques such as finishing, wiring, inlay, and even how to build a complete instrument from start to finish. At the same time, we started producing books on the same subject. They let us go into even more detail.” Of those, the best selling is their “Guitar Finishing Step-by-Step” book (item 5095), which even other woodworkers use for creating the heavily admired guitar finishes.
While the tool feedback fed instructional materials, those in turn generated more tool designs. “Through doing videos and writing books, we routinely discover that certain specialty tools are missing,” Jay pointed out. When that happens, they create whatever is necessary to fill the need.
Another critical product line comes from their Waverly manufacturing arm in Montana. Long revered in the industry for creating outstanding tuning machines, Waverly now makes a range of vintage-style cast, plated, and machined parts for guitars, mandolins, and banjos. Their main item is still tuners, the industry name for the geared mechanism used to tighten strings. “Our tuners are the most precise and accurate-looking vintage style tuners on the market,” Jay said with obvious pride. “They are perfect for those who want just the right look paired with outstanding performance.”
Athens also houses manufacturing facilities, though in a somewhat different vein. There, a woodworking shop processes specialized guitar woods into necks, fingerboards, bridges, backs and sides—in short, all the parts you’ll need for building a guitar. “Oddly enough,” Jay pointed out, “buying some parts, such as slotted, radiused ebony or rosewood fingerboards, is cheaper than doing it yourself, and thanks to our CNC machinery, it’s usually more accurate as well. Carved arched tops for mandolins, pre-bent guitar sides, and precisely thicknessed soundboards, backs and sides for acoustic guitars also fit into that category.”
The long and short of it is that Stew-Mac simply makes life easier for anyone—professional or neophyte—who wants to repair or build instruments. That’s a larger coterie than you might think.
“It’s amazing how many people want to build a guitar,” Jay explained. There’s a good reason for that. “It’s something you can build, then play and make music from. There’s nothing like giving wood new life by giving it a voice.”