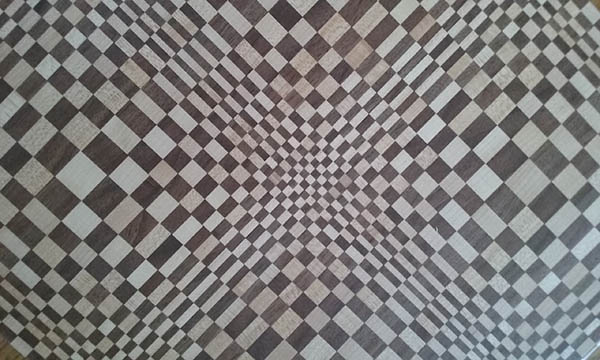
Steve Kelzer’s woodworking specialty is parquetry.
It’s an interest he discovered a few years ago, after taking a couple of classes from a local woodworker, and after a lifetime – well, at least since 4-H Club – of doing all sorts of woodworking, including furniture, kitchen cabinets, and woodturning – as a hobby and a means to gift family and friends.
Parquetry, according to Steve, is creating geometric figures and designs, whereas “marquetry” is creating pictures – a natural scene, a face – with veneer. “They do kind of cross over a little bit; you’ll see some marquetry pictures with a little bit of parquetry in them,” he said. Plus, “They all use the same raw material; it’s just a different spin on it of working with veneer.”
That’s one of the things Steve likes about parquetry: the opportunity to use all kinds of wood, in different colors. He has what he calls a “real good collection” of veneer, including dyed veneer and exotic woods, and some of his pieces can have 15 to 20 different varieties in them.
As for his designs, “I’ve kind of developed my own style,” Steve said. With “not a lot out there to go on” in reference to parquetry, he said, “I’m mostly influenced by quilt patterns,” particularly traditional patterns with repeating geometric elements, such as Tumbling Blocks. “Over half the things I do are the Tumbling Blocks pattern. I do a lot of things with it” – including using three different colors of veneer on each block, or playing with the pattern by putting designs inside the blocks.
“I had gone to some quilting shows and seen how they were creating optical illusions with quilts, too,” Steve said. That’s one of his goals with his work. He wants somebody to “walk by and look at it, and say, ‘How did he do that?’”
While Steve sometimes uses a DeWALT scroll saw to make a “sandwich” from half a dozen or so different colors of veneer, on which he draws a picture and then randomly cuts it out and reassembles it, he has also developed his own techniques for creating parquetry.
At first, he said, he was cutting out strips, but he has discovered that using shelf paper with a sticky back on one side allows him to “cut out a bunch of pieces, and then stick them down and assemble them. You can put all the pieces on the shelf paper and move them around and they stick.” He also places a grid behind the shelf paper to ensure accuracy, a factor he says is critical in working with these small pieces to ensure seamlessness and avoid gaps. A tool similar to a paper cutter allows him to cut his most common angles on the workpieces: 60 degrees and 45 degrees.
After finalizing his design on the shelving paper, Steve presses it together with a veneer press, using yellow glue for assembly.
With the sticky-back shelving paper, Steve said, he can also leave a project set up. “The nice thing about parquetry is it’s something you can do at your kitchen table, or in your living room, like a puzzle, instead of being in a shop with all the machines and dust. People can be walking by and say, ‘Why don’t you put this piece here?’”
Steve has participated in an “Art Wander” that showcases local artists, where he sets up a table in his shop to show people how he does his work; he’s also exhibited at some local libraries and participated in the Minnesota Woodworkers’ Guild’s Northern Woods Exhibition.
His parquetry, he said, has “been a big hit; people are pretty interested” – but that doesn’t mean he’s selling a lot of it. “It’s so labor-intensive, a piece may take 8, 10, 12 hours; then if you want $100, people are like ‘I don’t think so.’” Instead, he has incorporated it into furniture in order to showcase the parquetry work.
“Once you have the concept of what it is, you can go off in different directions,” Steve said.