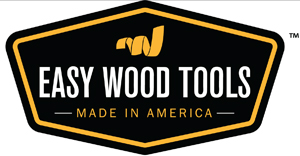
If you’re an avid woodturner, you’re probably familiar with Easy Wood Tools™ (EWT) line of Roughing, Finishing, Detailing and Hollowing tools. They feature replaceable carbide inserts that never need sharpening. Easy Wood Tools was first-to-market with carbide-insert turning tools in 2008, and since then, some other companies have replicated the style with similar products. Or, during the past couple of years, maybe you’ve added an Easy Chuck to your turning accessories. Easy Wood Tools launched it around Christmas 2012 with a number of innovative features not found on other four-jaw scroll chucks. In fact, nothing that comes out of EWT’s Lexington, Kentucky, facility is quite like any other woodturning product already on the market — and that’s exactly the way company founder Craig Jackson wants it. If EWT innovation isn’t truly “breakthrough,” Jackson won’t develop it.
“When we design a product, we start from scratch and not where company B left off,” Jackson says. “We never look at what others are doing because that way of business makes companies followers instead of leaders. We always go our own direction and don’t stop until we have a true solution.”
That mission toward unique innovation is what drove Easy Wood Tools to essentially throw away the “mold” oftraditional four-jaw scroll chucks when it began to design the Easy Chuck in 2009. Jackson estimates that it took about 18 months to develop the product — a fairly typical timeframe he and his staff have experienced for most EWT products. But the time spent at the drawing board to develop a “better” chuck was worth it for Craig, considering Easy Chuck’s advancements over other options. For one, the chuck features EWT’s patent-pending Snap-Lock Technology™. It allows a user to swap jaws in and out of the chuck in about 20 seconds, because there are no jaw screws to remove and reinstall. Instead, you press a keeper latch in the chuck and the jaw slides out. It reinstalls by sliding into place until it audibly snaps and locks. The jaws are heat-treated, and the chuck’s components are hardened for maximum durability.
“I also wanted a chuck I could operate quickly with one hand instead of having to crank a chuck key 30 times,” Jackson says. So, EWT added a Zoom Ring™ to the chuck so it can quickly be brought to initial tension on a workpiece by turning an outer collar instead of twisting a T-wrench. To make Easy Chuck evenmore user-friendly, its Easy Jaws™ have rounded corners to prevent knuckle injuries. So far as Jackson is aware, Easy Chuck is the first chuck on the market with a rounded jaw design. It’s also the only American-made woodturning chuck, Jackson says, “and we are the only company ever to make a woodturning chuck in the U.S.”
To date, Jackson reports, Easy Wood Tools has not had a single Easy Chuck owner return his or her chuck because of dissatisfaction with it. Instead, customers tend to report that they appreciate the ease of use and that the chuck emanates less vibration than other chucks, which leads to smoother cuts.
This month, Easy Wood Tools is taking another big step with its Easy Chuck program by releasing two sets of oversized jaws and jaw extensions. The new “Big Easy Jaws” will come in both 12- and 16-in. sizes, as well as 20-in. Big Easy Extensions that attach to the 16-in. jaw option. The new jaws will enable lathes with 12 to 20-in. swings to grip the outside edges of platters and bowl rims using a set of dovetail-shaped, urethane grippers. Similar in function to traditional “Cole” or “jumbo” jaws, EWT Big Easy Jaws will instead feature the company’s Snap-Lock technology so they can be mounted or removed from an Easy Chuck in under a minute. The plates are made of aircraft aluminum, and the base jaws onto which they mount will be medium carbon steel.
Jackson believes that, aside from the convenience of easy installation, what also will set Big Easy Jaws apart from other oversized chuck jaws is the better configuration of mounting holes for the grippers. “All the major manufacturers we looked at do not have the gripper holes in their jaw plates with a close enough spacing that you can grip any diameter. We do.”
But Big Easy Jaws aren’t the only new product that will hit the turning market this month. Jackson is also pleased to report that, after about four or five years of planning, Easy Wood Tools will now have an Easy Parting Tool™ as a new addition to its carbide-insert family of cutting tools. But, the process for developing a replaceable cutter for the parting tool was more complex than other options because its 1/8-in. cutting width was too narrow to fit a mounting screw.
Instead of a screw-install system, the new Easy Parting Tool’s carbide cutter slides into a stopped pocket in the end of the tool shaft. The more pressure that’s applied during cutting, the more tightly the insert is nested in the tool. V-grooves in the carbide interface with the rim of the pocket, forming “kind of a triple V-lock design,” Jackson says. The design also makes it impossible for the insert to move side to side in the pocket.
However, as with the other Easy Wood Tool carbide inserts, the cutter in the Parting Tool eventually will need to be replaced. At that point, another unique innovation comes into play. Removing and installing a new cutter is accomplished by way of a
Flex Key that is included with the Parting Tool. The Key has a pair of protruding pins that engage a hole in the tool shaft and either the tip or the back edge of the insert. Levering the key one way or the other either presses the new insert into place or pops it out and free. When used during installation of a new insert, the point at which the Key literally flexes in hand is an indication that the correct installation force has been applied.
Jackson delayed the product’s launch by a month in order to develop the new key and make it even easier for end users to install the inserts correctly. “When I was writing the manual, I found myself saying ‘press the cutter into the cutter pocket with 7 to 10 pounds of force against a soft piece of wood.’ I finally realized that’s crazy to ask my customers to figure out how much seven to 10 pounds of force even is!”
Craig says ETW pushes for a level of customer intuition about a
product that goes beyond what some competitors consider to be enough. If a product isn’t truly easy to figure out and use, the failure, according to according to Jackson, is with the product’s design — not the end user’s understanding. He also feels it shouldn’t take a manual to learn how to use an EWT tool.
“When you are done with a product design, you are maybe halfway there…We don’t make the customer suffer through our inability to design simple products by stopping short of making it as simple and user-friendly as possible. We have not done our job if we pass on complexity to the customer,” Jackson says.
Taking on the challenges of perpetually “reinventing wheels” when it comes to new turning tools is not for everyone. Generally speaking, Jackson says his company starts a design where his competitors leave off, but “my staff knows that it takes a long time to do things right.” So, despite his hope that eventually a new product might take less than a year or more to develop, he doubts that will ever happen.
“Some call it the ‘bleeding’ edge instead of the leading edge when you are the first to go to market, because you are the one that does 90 percent of the bloody work … But the other side of it is that you are the only one that truly understands every possible facet of what is important about the design. And only you have that deep understanding enough to make a true solution.”
And a solution done well, as EWT can attest, leads to satisfied woodturners.
To learn more about Easy Wood Tools products, click here.