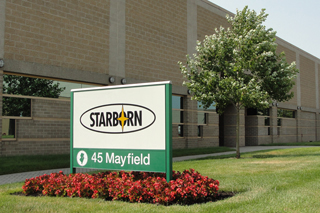
In just a few more turns of the calendar, summer will be upon us again. Maybe you’re planning to build a deck this season when the warmer weather returns. That project will involve screws … probably thousands and thousands of them. While you might see deck screws as simply a means to an end – a way to get those deck boards fastened down and and the project done – Paul Gertner and his staff at Starborn Industries spend a whole lot time thinking about how to make that fastener work more effectively, last longer and look better. Screws are the core of the company’s business and have been for more than 30 years.
Paul says his father, who founded Starborn back in the early 1960s, was a forward-thinking kind of guy. Initially, Starborn was a wood products company. His father imported wooden sliding door tracks from Asia, then began to have them made in the Brooklyn, New York area. That business bloomed into floating bracket and shelf systems when those came into vogue. Eventually, Starborn opened a woodworking plant that made wooden drapery hardware, butcher block tables and end tables. In fact, the Edison, New Jersey-based company still carries a variety of wood products such as dowels, paper-backed veneer and a few other items.
While business in wood products was good for Starborn, it seemed to reach a plateau. Then, in the early ’80s, dad set his sights on fasteners – specifically, drywall screws. “Up until this time, drywall was mostly nailed in place here in the United States, but my father had the idea to be one of the first importers of drywall screws. That quickly became the focus of our business as drywall fastening trends changed. The business began to grow again,” Gertner says. Paul, who was working in urban planning in California at the time, decided to “go back to his roots” and took the business over in 1986 when his parents retired.
Paul says with some amazement that that was 25 years ago already, but a lot of innovation in screws has happened at Starborn since. Back in the mid-’90s, Paul recalls there was a “sea change” of sorts taking place in the deck-building industry. “This was around the time when consumers began to view their decks as outdoor living areas that should looks as good as indoor rooms. We saw the need for fasteners that offered the quality and visual appeal that matched that aspiration.”
So, Starborn launched a line of epoxy-coated, hardened steel deck screws called Deckfast® in green and gray colors to match treated and aged deck lumber. As composite decking such as Trex took off, the Deckfast product line was expanded to include seven different screw colors to match the increasing variety of color options for composite decking. The screws were also modified with a special TransVerse(TM) double thread pattern to eliminate the tendency of screw heads to “mushroom” the wood fibers around their entry points. This thread pattern has since become the industry standard for composite-lumber screws.
Stainless-steel deck screws have been a premium option for high quality decking or marine applications for a long time, but Starborn took stainless one step further in 2003 when it brought Headcote® screws to market. “It was one of those ‘No duh’ inventions for us, really. Headcote was the first stainless-steel fastener with color-coated heads … Up until then, no one coated stainless steel screws because the only reason for coating (them) was for corrosion resistance. As soon as it was launched, it was a big hit,” Paul reports. Now Headcote comes in a rainbow of decking-matched colors, plus TransVerse-threaded composite screws, as well as a Razorback®version with square threads and a nibbed head to reduce the need for pre-drilling.
The company has kept pace with current evolutions of decking material into today’s coextruded, or capstock lumber. It’s made of a softer internal core PVC with a hardened outer plastic shell. Starborn just invented and will soon introduce a stainless line for coextruded decking called Cap-Tor. It will come in nine colors with a new thread and head design that Paul says will cut through the hard outer surface more effectively than other options.
Aside from improving deck screws, Starborn also focuses on developing better ways for driving and concealing them. Over the last 10 years or so, the trend in deckinghas been toward hidden fastening systems with a variety of metal clips that install from the side or below. But, Paul says there’s growing skepticism in the deck-building market about these hidden systems, because they don’t account adequately for wood movement, or the clips can lead to squeaking. So, more contractors are returning to conventional face-screwed installation. That in turn can involve time-consuming pre-drilling on hardwood decks for a clean countersink, and then labor-intensive plugging to hide the screw heads.
Starborn set out to address both limitations. The company created Smart-Bit®, which combines a countersinking drill bit with a free-spinning outer collar and a non-marring rubber bushing. It automatically sets the countersink depth for a variety of screw sizes and was designed to precisely sink Starborn screws. The drill bit has special parabolic flutes that purportedly bore through deck lumber more than twice as fast as standard wood bits. “For Smart-Bit, we decided to turn the problem of pre-drilling on its head. Instead of avoiding pre-drilling, we set out to make (the process) easier.”
For deckbuilders that need to plug those countersunk holes, Starborn’s newest innovation – the Pro Plug™ System – works in tandem with the Smart-Bit. It includes a modified glue bottle nozzle with a retracting sleeve that dispenses glue directly into the countersink. It fits 4- or 8-oz. Titebond® or Elmer’s® glue bottles. “The nozzle delivers glue to the sidewalls of the plug hole. The old technique of rolling your plugs in a dab of glue can now be a thing of the past.”
Starborn also engineers specialized wood plugs for Pro Plug that are flared just enough to fill the pocket left above the screw head and produce a good compression fit. They’re designed to meet the deck surface flush to eliminate sawing or chiseling off the excess. The plugs are available in nine different hardwood species for decks, including mahogany, ipe and various other exotics. Pro Plug is also suitable for interior flooring – a growing market for Starborn – and a dozen domestic and exotic wood plug species are made for this purpose. “We decided to go back to the basics of plugging to make it better and faster,” Gertner says.
All in all, Starborn’s innovation is rooted in practical solutions that save time and money but also work within the methodology that installers prefer. It’s innovation that seems to be driven by need instead of novelty. “We look for building methods and techniques that people want to use, but avoid because they are too labor-intensive or difficult. Then we figure out new ways to do old things better. It’s one of the key reasons we’ve thrived for so long … Plus, we really do love to invent stuff. It’s just fun.”