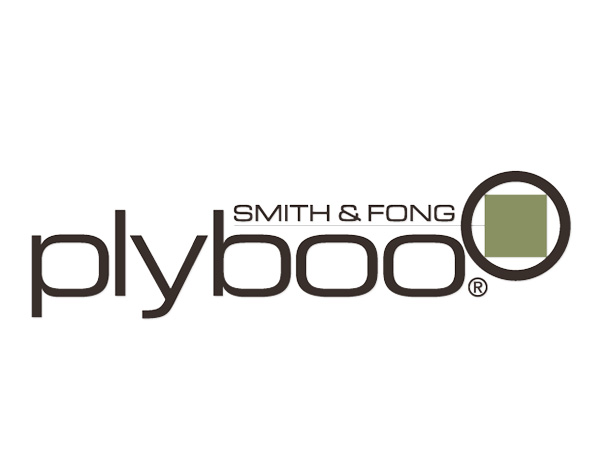
Woodworkers are constantly on the lookout for new and exciting species that are durable, attractive, easy to work with, and, dare I say it, environmentally correct, or “green.” That means wood that’s not endangered, grows quickly and is harvested in a renewable manner. If that’s a quest you’ve been on, take heart, because a perfect fit is here in the form of Plyboo. Available in both plywood-like sheets and blocks similar to solid wood, it’s made by Smith and Fong, a company started for and dedicated to bringing this reedy wood alternative to us woodworkers.
As catchy as it is, I must admit that the name “Plyboo,” a contraction of “plywood bamboo,” sounds more like a character from Winnie the Pooh than a construction material. Notwithstanding, it’s one heck of a good substitute and one that works very much like wood.
“It seems to have all the good traits of wood with very little of the bad,” explained Dan Smith, the Smith half of Smith and Fong. “It can be ripped, shaped, routed and molded like wood. It cuts, laminates and sands beautifully and takes joinery very well. Bamboo also has a tensile and crush strength far exceeding most woods, is twice as stable as oak, and, contrary to some early myths, it takes stain and all finishes exceptionally well.”
“Bamboo is a grass, or reed, not a tree. In fact, it is the largest grass that grows,” Dan pointed out, “and has a wonderful root system that holds soil in place and prevents erosion. It does not need irrigation, fertilization, or pesticides, and most is still harvested by hand. There are about 1500 different species, and it grows on every continent except Antarctica. Even the U.S. has three native species.”
“About 95 percent of the bamboo we use comes from China,” Dan continued. “It’s a species called ‘moso,’ or ‘timber bamboo,’ which grows about six inches in diameter and 40 feet high.” Ironically, moso is also good to eat. The locals dig up the bamboo shoots and sell them for use in Chinese food. As luck would have it, bamboo grows very fast. “Moso reproduces about 25 percent of itself each year and can be harvested in four to six years. You can harvest 20 percent of your bamboo forest yearly, or 100 percent every five years and do that indefinitely because it sends up new shoots each year.
“Older poles are heavier and contain a better quality of woody material, and because bamboo is sold by weight, the farmers prefer to cut bamboo mature enough to be at its best. As a result, farmers cull the crop by taking only the larger, more sellable stalks and harvest them every other year. That means if you harvest a stand of bamboo correctly, you will never run out of material. Furthermore, farmers are given a quota by the government controlling what they’re permitted to harvest, and the buyer must have the documentation that shows how many poles he bought from each seller. In short, the harvest is both regulated and totally sustainable.”
The company itself has an equally interesting provenance. Smith and Fong, the namesakes of the company, were language exchange partners at San Francisco State College. “Fong was studying English and I was studying Mandarin,” Smith explained. “He was here on an artistic scholarship in the early 1980s, something unusual for China at that time. When we graduated from college, we parted ways, but rejoined in 1989 and started Smith and Fong. We had been involved in a couple of other ventures previously, so we had a history together.”
Dan had worked as a carpenter prior to college, and had traveled extensively through Asia before returning to get a degree in Mandarin and business. The people he met on his travels are still working with him today. “I had spent some time in Taiwan and met people working with laminated bamboo, which was actually developed there. Though fairly new to us, the technology of laminated bamboo dates back nearly 100 years.” One Taipei university houses a major research center for the study of this bamboo.
Smith and Fong started importing a gift line of tea boxes, picture frames, and trays made of laminated bamboo sheets. Up until then, the U.S. had not been familiar with laminated bamboo. “People saw bamboo as a cheap component,” Dan pointed out, “and had a hard time accepting it as a valued raw material for woodworking. One day, Andy Rooney displayed one of our boxes on television, opening it online and commenting on the lovely scent it had.” That added a bit of exposure.
Around 1993, they got more heavily involved in bamboo flooring, which was just emerging in the U.S. market, and the same year, trademarked the name “Plyboo.” That’s also the year Fong left the company, opting instead to take over their other joint operation, a graphic design business. The company name stayed the same, though Smith now has a new partner named Angus Stocks. “We brought the bamboo flooring to the National Wood Flooring Association convention in the spring of 1994. For many people, it was their first exposure to bamboo. Then in 1996, we introduced our first bamboo plywood; a three-ply, three quarter inch thick sheet.”
Today they offer 20 different variations of bamboo flooring and at least 90 different bamboo sheet goods items. They range from normal thickness 6-mm veneers in 4×8 sheets, through 2 mm, ¼” inch, 3/8″, ½”inch, ¾” and 7/8″ sheets. There are also end blocks up to 1 ½” size, and linear single ply, which behaves rather like solid lumber, in ¼,” ½” and ¾” inch sheets. The various iterations are formed in face grain, side grain, end grain, and reconstituted shredded formats, each offering a different hardness and appearance.
Plyboo is available nationwide through a few local distributors, or direct from their web site. Because it started in the architectural market, it is not yet widely available at the consumer level, but you can expect to see more and more locations stocking Plyboo in the near future. “Our goal is to make Plyboo more easily available, while making the product itself better and better,” Dan said.
“With hundreds of laminations per sheet,” Dan cautioned, “the lamination process is quite critical. One failure can spell the end of the board. Hence, whom you buy from is equally critical. We have been personally involved in the design and manufacture of our products since 1994 and have more experience in the field than any other producer. As a result, we produce the best quality bamboo panel goods on the market.”
As with all laminated products, off-gassing formaldehyde is also a major concern. “At present, our bamboo sheet goods are already well below plywood in formaldehyde emissions, but we want to go even further. As a result, we are currently developing a proprietary formaldehyde-free lamination system that should be available in spring of 2007.
“More and more woodworkers are having good experiences with Plyboo,” Dan pointed out. “It is very affordable, a delight to work with, has an amazing aesthetic and offers a chance to promote a sustainable future with a beautiful end-product.”