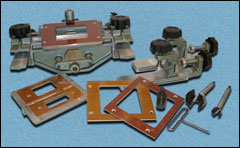
Originally trained as a metalworker in Germany, Siegmund Scholler ended up — via a detour through a few years in Canada — as a skilled carpenter building winding staircases and other high-end interiors for upscale homes in Michigan.
One of those tasks was hanging doors, which proved to be more frustrating than Siegmund thought it should. There had to be a way, he thought, that even an unskilled helper could do a perfect job in hanging a door right the first time. “Especially when we go to big doors, 8 foot doors at 2-1/4, 250 pounds, you don’t want to do them twice,” he said.
With that in mind, Siegmund spent eight years fooling around and trying to create the jig that he knew could exist. “When I started out, I was going to do something like a miter saw stand for cutting boards very precise. Then, when I see the stand, I thought I might as well put something under it that can do hinged doors with it.” He was looking for a mechanism — “I just wanted something simple,” he said — “and all of a sudden the idea came that I don’t need the miter saw. I just need the door itself as a rail. If I attach the jamb to the door, then I can make [the mortise for] each hinge.”
This self-aligning combination unit accurately mortises the door and jamb for the hinges, drills the holes for the lockset and rabbets the jambs for the header. It works with any router, although a larger router is necessary if you’re going to use larger hinges.
“You do the jamb and the door at the same time” and it doesn’t really matter where you put your hinge, Siegmund said: “those two always fit. An eighth of an inch one way or the other makes no difference, but that particular hinge always fits.”
After clamping your door, you place his jig onto it, attach a frame, then slide a hinge into position where you want it. “If the door is two feet long or 10 feet long, it makes no difference,” Siegmund said. “You slide it onto where you want to stop and put the hinge, and that’s where the hinge fits.”
He went through the patent process for his Sieg Jig, as he calls it, and has started marketing it through such venues as his web site, which includes a video demonstrating the SiegJig in action. At the moment, he’s trying to recoup his costs from patenting and development, and it’s his hope that the Jig will sell well enough that he can hand over his carpentry business to his assistants and focus on the SiegJig full-time. “I have some guys in the shop right now who could take over,” he said.
“Basically, I’m saying [the Jig] is for upscale finish carpenters or specialized millwork shops: guys that hang their own doors,” he said. With the Jig, though, they could hand off the task to their assistants, it is that simple.
Siegmund is currently making all of the Jigs himself, in his own shop. “I got a milling machine, and I got a lathe, and then I go to town,” he said. “I do maybe, say, thirty or forty at one crack right now until, you know, the production increases.”
His materials are aluminum castings, a steel spindle, and phenolic plastic for the routing templates. “The nice thing about it is, if you hit it with a router bit, you don’t damage the router bit,” he explained about his choice of phenolic. “You might dent the plastic, but the conventional way, if you had the metal, you lose your bit and your metal base.”
Cost considerations are what he hopes will appeal to those who might be in the market for a SiegJig, which currently retails for $670. But if you’re installing doors yourself, he said, “As soon as you go out of standard, then the whole cost picture changes.” If you’re going to install a specialty door, “you might as well hang it yourself because you have enough money in it.”