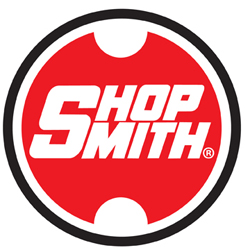
Maybe you’ve done the same double take as me if you’ve bought sandpaper from Lowe’s® in the past six months or so. It’s the new Shopsmith brand that caught my eye. Yep, Ali Industries has entered into a license agreement with Shopsmith®, that venerable company known for combination woodworking machines, to produce a branded line of industrial-grade sanding disks, sheets, belts and sanding blocks under the Shopsmith logo. And this isn’t just a new apples-to-apples sandpaper line to compete with other home center brands. I’m told they’re a significant cut above other consumer-grade sandpapers we find at the big retailers.
But Shopsmith … sandpaper? Not a pairing I would have guessed.
So, I gave Teri Masaschi a call to find out more. She’s a finishing and restoration expert and the consultant for Ali Industries, based near Dayton, Ohio. “At first, I was pretty surprised to learn about Shopsmith Abrasives, too,” she recalls, “but that brand name carries a strong image of working in the shop with grandpa, enjoying the woodworking process and, of course, sanding a project. People remember it fondly from years gone by.”
The Shopsmith legacy was certainly familiar to Terry Ali, president of Ali Industries. When the brand name became available several years ago, he entered into a licensing agreement with Shopsmith Corporation and started to develop the new sandpaper products. Ali, which makes a comprehensive family of Gator Finishing Products, plus abrasives for the automotive industry, has been in the abrasives business for more than 50 years. Several years ago, I paid a visit to their Fairborn, Ohio, headquarters. It was an impressive operation, and here’s a blog post to tell you more about it.
“Even though Ali makes a great line of consumer abrasives, Terry realized that there was a significant need for a premium grade of abrasives to give consumers something better than what they’ve ever been able to buy before … industrial-grade products,” Masaschi says.
The new Shopsmith line features “G2 Technology,” which purportedly makes them last up to four times longer than other consumer sandpapers. The disks, which come in a full range of grits, have a film backing to resist tearing. This plastic layer also increases the flexibility of the backing so abrasives near the edge don’t burn through as quickly, and it should help to protect sander pads from premature wear. Even the adhesive that holds the abrasive in place is industrial quality, and a no-load coating should improve cutting performance. Shopsmith’s sanding belts, available for 3- or 4-in. belt sanders, are covered with ceramic rather than aluminum oxide: a feature unique to consumer-grade sanding belt options. The belts are made of a heavy-duty polyester-cotton blend.
Shopsmith also offers several styles of soft-foam finishing blocks that accept hook-and-loop paper. They include a special feature Teri helped design. “I kept insisting that a good finishing block should not only fit in your hand comfortably but also needs to be flat on the bottom.” So now the finishing block has a steel plate embedded in the foam to ensure a flat contact surface between abrasive and workpiece, plus a layer of foam over the plate to provide some “give” for the backing paper, extending its usable life.
In addition to offering a professional-grade product line, however, Ali Industries also hopes a unique color-coded packaging system on the new Shopsmith products will better educate consumers about their sanding choices. A common complaint among woodworkers, of course, is that sanding takes too long in general, and good finish prep is a hit-or-miss proposition. Part of the problem, Masaschi says, stems from “all the tribal knowledge and misinformation about sanding that gets passed through the pipeline.”
It’s the mixed messages that might have a fellow woodworker or a big box employee telling you “you can skip grits. You don’t need 150-grit, just 120 and 220.” That’s a misnomer she’s heard firsthand. “That kind of misinformation is unfortunate, because it is typical of a DIYer that skips grits and wonders why the stain looks so awful or the project doesn’t finish well.”
To help consumers make better decisions about what products to choose and use, Shopsmith abrasives are grouped by four packaging colors and a “Step Finishing System” approach. The first step, “Removal,” is coded green and covers coarse grits 40 to 100. Sanding and Surface Preparation, which comprises Step 2, is coded orange and includes grits 120, 150 and 180. “Finishing” is Step 3 of the process, with 220-, 320- and 400-grit and coded yellow. Each grit has a clear description on the package of what the abrasive is intended to do. Step 4, coded blue, constitutes the final finishing step: rubbing out and polishing. That product family, Masaschi says, is in its infancy right now, but it will be filled out soon. At present, Step 4 products include a tack cloth and an ultra-fine non-woven abrasive pad. Very fine abrasives, liquid polishes and more non-woven replacements for steel wool are in the works.
Ali Industries is also investing in a video series with Teri as host, to support sanding and finishing education. Currently, video topics include hand-sanding basics, power sanding, building a piano finish on a waterfall bubinga board and more. The company plans to continue making more videos, and Masaschi sees the potential range of topics to be extensive. You can see these videos on a YouTube channel by searching either for Gator Finishing or Shopsmith Abrasives.
Teri says that Shopsmith Abrasives are catching on well within the woodworking community. And, the time has come for a new and better understanding of both the sanding and finishing process. With clearer consumer information and quality abrasives, sanding doesn’t have to be drudgery anymore. More importantly, the process of sanding effectively is time well-spent, Teri adds. “I like to tell people, a piece well sanded is already half finished.”
Learn more about Shopsmith Abrasives by clicking here.