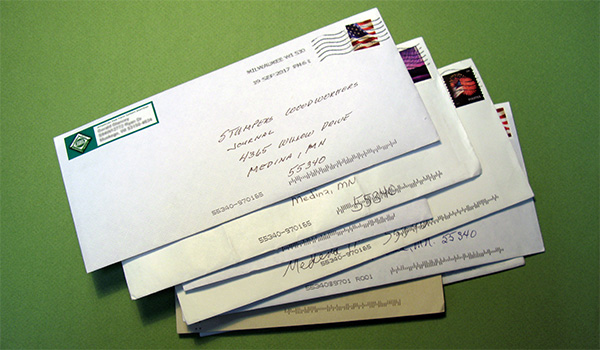
Dog Days Sawdust
In response to Rob’s editorial last time out regarding his tactics for shop time in the heat of a Minnesota summer – and his method of cleaning out sawdust with a leaf blower – we heard from several readers who had their own tips for hot times in the shop, but little sympathy. – Editor
“Speaking of heat and bugs, you can add humidity to the list, and lots of it. It always cracks me up to read about woodworkers who live in the northern parts of the country. Here in Houston, and most parts of the Gulf Coast, summer brings temps in the mid to high 90s (Fahrenheit, of course), humidity in the 90s (percentrelative) and mosquitoes. Unless you are lucky enough to have an air conditioned shop, you have to get accustomed to the conditions.
“Most of us work out of our garages since there are no basements here. This year is especially wonderful due to above average rainfall and tropical moisture blowing in off the Gulf of Mexico. The bugs are having a field day. When you step outside and your glasses constantly fog, you know it will be hot and muggy. Keeping the rust off your tools is a continual battle. ‘Weather permitting’ here starts sometime in October. Or you do like most of us and put a few big fans in the garage, spray on the DEET and go to work, making sure you drink plenty of fluids and head inside for a break when all your clothes are soaked with perspiration.
“The best part is this: We can work with our doors open all year long with the mild winters we have. And if you need a break from woodworking, head to the golf course. They’re open all year long!” – Gary Faries
“I enjoyed your article, ‘Hot and Dusty’ this week, on which I’d like to comment. I, too, enjoy woodworking in the summer. Although it gets pretty hot here in Florida during the day, I equip my work area with an industrial fan turned on high all of the time. I drag out my tools on their wheels to just outside the garage door where there is a little shade after 11 a.m. The fan blows most of the dust away from my work while helping to cool my body. I keep myself hydrated with an iced drink close by at all times. I stop whenever it is convenient to reward myself with a dip in the pool for about 15 minutes and then back to work until dinner time. In this way, I can enjoy my hobby and the beautiful weather at the same time. Make sawdust anytime of the year.” – Denny Mela
“Just a quick note to express my appreciation for your comments. I live in Becida, 20 miles southwest of Bemidji [Minnesota]. The time is 12:40 a.m.; I just went inside. I’ve been working on a Greene & Greene medicine cabinet in my shop. Temp was 71 deg. with a dew point of 70 when I went out at 7:00 PM, it’s 59 deg. right now. It just doesn’t get better than this. Yeah, the environment might be a challenge, but I wouldn’t want to live anywhere else.” – Brad Gensmer
“You needed someone else to tell you about the greatest garage cleaning system ever invented by man? I was wanting a garage-blower-outer (most people know them as leaf blowers) long before I even had one. One day, my next door neighbor was using his to clean off his patio, and I asked him if I could borrow it. He agreed, and I used it to blow out my garage. As soon as I was done and had returned it to him, I started researching garage-blower-outers. As luck would have it, one fell into my lap within a few days. While I do use it for other tasks, it was purchased primarily to blow out my garage shop.” – Wayne Jolly
Separator Story
One reader had a follow-up question on the separator vs. cyclone query from last issue’s Q&A section, based on his own experience. – Editor
Read the query from John Michaud about separator or cyclone. I have a similar 650 cfm unit and had built my own separator and was very pleased with its performance until, for air quality reasons, I purchased a canister filter for it. The air flow was dramatically improved to the point the collector actually sucked in the plastic garbage can’s sides AND most everything that previously had been separated. So, out with the separator. Air is better (also have an air cleaner), and I recovered about 2+ feet of wall space in my 300 sf shop. So, would a canister be a good recommendation for John’s situation, or is my experience unique, do you think? -John M.
Since I’m a child of the ’60’s, let me paraphrase an old saw and just say, “If it works good, do it!” Actually, a better answer might be centered around the kind of stuff you’re intending to be sucking up most. If it is big wood chips from jointers, planers etc., then a separator might do better. (Not to impugn a homemade one, but the commercially made ones work well.) If, on the other hand, sawdust and smaller things are in the target zone, then a filter might be a better choice. In the end, it is a personal choice – and if it works good, do it…” – Tim Inman
Scarf Joinery
These readers thought our experts missed the boat when talking about scarf joints in Q&A. – Editor
“The question referred to scarf joints as applied to boatbuilding. If this were cove molding in a house, the 45° cuts would be okay, but it won’t cut it at all in boatbuilding. The correct scarf joint for this application has a ratio of length to thickness of about 8:1. In other words, the length of the scarf should be eight times the thickness of the material being joined. This is what gives the joint the strength needed to hold together when bent around a curved edge such as the gunwale or inwale. This is also a good joint for making land-based curves on furniture or artwork if material is at a premium.” -Gordon Patnude
“If a scarf joint is going to be bent, and hence have continuous shear and/or strain placed on the epoxy joint, it must be backed up with a mechanical fastener. Epoxy is a plastic and will flow under pressure with time. Back 28 years ago, I was building a small sailboat, too (a Snipe) and wanted to scarf two eight-foot marine plywood sheets together, rather than using a very expensive 16-foot sheet. My boss at the time, a PhD mechanical engineer, warned me of the plastic stress failure mode, so I concocted an experiment to test this. Three identical lengths of marine ply were clamped at one end of my bench and extended outward unsupported. I attached a four-pound diver’s belt weight to the end of each one. One length was straight ply, one had a scarf bonded by epoxy only, and one had silicon bronze screws backing up epoxy. After one month, they all had the same droop as they did at the start, but the addition of a 4-oz. weight to each caused the epoxy-only piece to fail catastrophically and the other two to increase droop by approximately the same amount. The epoxy-only joint had lost almost all its strength. I was using a very good, wood penetrating epoxy from System Three, meant for use in boatbuiding/repair.
“Also note that saltwater will corrode stainless; not as fast as plain steel, but it still will corrode. Silicon bronze screws or ring nails hold up much, much better, and is “standard” for boatbuilders. If you seal the screw from water with your epoxy, it should hold up well, even if stainless or brass.” – Don Rumrill
Creating a Kiln
And this reader shared his story related to the third question from last issue’s Q&A, on building a kiln for bowl turning. – Editor
“I am adding my two cents on this. I read about different types of kilns and decided to convert an old dishwasher into a wood drying oven/kiln. I use this for my turning blanks, and about 80 percent of them do not crack or split. I got the dishwasher on Craigs List for free, and then put a bathroom vent fan, PVC and duct to pipe it in. I pulled the motor out of the bottom along with the washer arm, then just plumbed in the duct work from the bottom, connecting the wires from the old motor to the fan. So, when you turn on the dishwasher, the fan will start blowing in fresh air. Then I cut off all of the tines from the upper and lower racks and laid my wood on them with space around each piece. All of the moist air exits out of the top of the door vents. You can leave the heating element in, pumping up the internal temperature, or run it on economy cycle without the heat. The only drawback is, this method it will run about a half an hour at a time. Six pieces of a freshly cut log took about three months to dry, versus six months to a year.” – Bruce Branecki