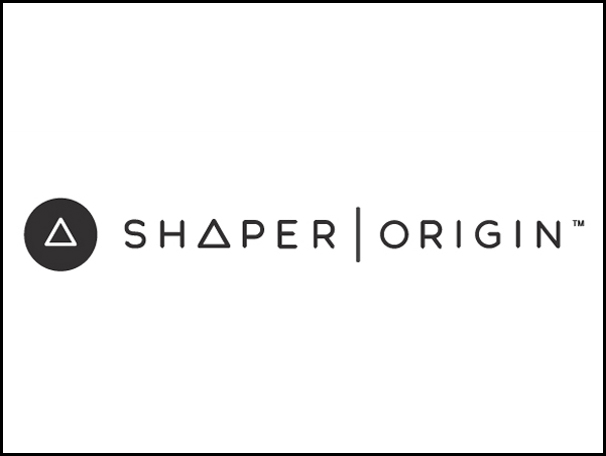
During last summer’s AWFS fair in Las Vegas, Woodworker’s Journal had the opportunity to interview Joe Hebenstreit, CEO of Shaper Tools, Inc., and see the company’s revolutionary Origin tool for the first time. If you didn’t catch our video of that experience, you can watch it now by clicking here.
Origin is the first routing tool that combines an onboard camera, touchscreen and three-axis positioning engine to add precision to handheld routing operations. Once a user applies adhesive-backed “ShaperTape” to a workpiece and allows Origin to scan the workspace, the tool effectively knows where the limits of its routing area are by following the tape. It will cut complex joinery, intricate inlays or shapes in any size in wood, soft metals, plastics and composites with a high degree of accuracy and repeatability. Origin can be programmed with common CAD or 2D vector software. Or, the user can design the cutting path with the tool’s built-in drawing program. Shaper Tools even has pre-formatted project designs in its ShaperHub library on the company website.
When Origin knows what you intend to cut, making that cut involves steering the 15-lb. tool along a path shown on its top viewing screen while the router spindle cuts side to side, front to back and up and down automatically. If you happen to veer off course, Origin will sense the change and retract its 1/4-in.-shank router bit to prevent you from making a mistake. So, even novices to routing can experience a higher degree of success with the tool. And, its portability and connection to the operator’s movement give it some unique advantages over traditional “hands-free” stationary CNC machines.
The company was founded by a couple of self-described “tinkers” — Alec Rivers and Ilan Moyer — who met through their studies at MIT.
Rivers says the origin of Origin began while he was taking some time off from graduate school to work in industry. Lacking a creative outlet for his free time, he picked up some woodworking tools from the local Rockler store in the Cambridge, Massachusetts, area and started making projects in his apartment. But he soon realized that acquiring the skills to use traditional woodworking tools well, as his grandfather had done when he was a boy, was going to take time and effort.
“I liked working with physical tools for a change,” Rivers recalls, “but I was immediately more interested in the tools themselves than the projects I was working on.”
After some hit-and-miss experiences with his tools and those first woodworking projects, Rivers began to experiment with the idea of combining the physical process of using a router with the precision and flexibility of a computer. As a hobbyist woodworker, he appreciated the physicality of using his hands but was frustrated by the inevitable learning curve and the all the mistakes that came with it.
“I still remember having trouble sleeping the night I thought of adding ‘snap to line’ to a router,” Rivers says. And, working in a confined apartment space with limited funds made a large and expensive CNC machine unrealistic. “A handheld power tool that could save me from my own mistakes, I thought, would fit me perfectly.”
Unlike Rivers, Moyer was already an experienced machinist by the time he entered MIT as an engineering student. He says that electronics fascinated him as a child, until a Micro-Mark small tools catalog showed up at his doorstep during high school.
“That opened my eyes to the possibilities afforded by personal-scale machine tools that expand our abilities to work precisely with wood and metal,” Moyer says.
He soon acquired a miniature milling machine and lathe and spent all of his free time learning and practicing machining. Those experiences “tipped the scales” for him to pursue mechanical engineering as an undergrad.
During the next three years, Moyer spent a lot of time in MIT’s Hobby Shop, where he expanded his skills with full-size woodworking machines to build projects. He also got involved with MIT’s Center for Bits and Atoms (CBA) that focuses on pioneering the future of digital fabrication.
“It was at the MIT CBA that I got really interested in building tools,” Mower recalls. “My undergrad thesis, entitled ‘Rapid Prototyping of Rapid Prototyping Machines,’ was focused on making tools that make it easier for individuals to build their own tools.”
After college, Moyer put those talents to use, developing miniature milling machines, 3D printers, a personal Jacquard loom and several positioning engines that are now used commercially. He met Rivers though a mutual friend who connected the two when Rivers was looking for mechanical engineering help to create an Origin prototype. That’s how the two joined forces and eventually founded the company in 2012.
During the years that have passed, Origin has gone through many prototyping iterations as Rivers and Moyer tackled its design challenges. Among them were how to engineer the tool’s mechanical correction mechanism and how to add a third axis for plunging and retracting the bit, while still keeping Origin compact and easy to use. There was also the financial hurdle of convincing investors to get involved with the company in the first place. Rivers says the very mention of developing a new woodworking tool at the time “caused most investors’ eyes to glaze over.”
But eventually, the funds were procured, and Hebenstreit was brought on board as CEO to help the fledgling Shaper Tools refine its production process for mass-producing Origin. That led to a “fleet” of the first 10 Origin tools and lots of time spent refining its capabilities with end users.
“Over the course of that fleet’s lifetime, we logged what was surely thousands of hours of testing, with a significant fraction being in the hands of people outside the company with a wide range of professional and hobbyist craft backgrounds,” Hebenstreit says. “That experience led to a complete ground-up redesign, resulting in the tool we’re shipping today.”
Currently, Shaper Tools has 21 full-time employees with a lot of combined experience in bringing reliable consumer products to market. Hebenstreit says their highly diverse career backgrounds range from consumer electronics at Apple, Amazon and Google to Tesla automotive. There are also staffers who have come from movie visual effects, industrial design and furniture fabrication.
“Perhaps surprisingly, none of us came from the power tool industry,” Hebenstreit adds. “But perhaps that’s also not surprising, as not having a preconceived notion about how something should or should not be done often leads to significant developmental breakthroughs.”
Clearly, Origin is unconventional when compared to typical woodworking machines and CNC platforms. Its uniqueness is also proving to be appealing to young people who are interested in making things with their hands and have grown up “digital native” already, Hebenstreit says. “They’re accustomed to letting a computer help them achieve their goals. Ultimately, we really believe Origin is the start of a new kind of human/digital hybrid workshop.”
Some may argue that traditional CNC machines already do what Shaper Origin can do. But, Hebenstreit differentiates Origin in several ways: Origin is portable; it doesn’t have a limited work envelope; and it can work on an already existing workpiece that couldn’t be put on a CNC table. At just under $2,100, it’s also cheaper than full-size CNC systems, so several could be used in the same shop for the cost of one CNC machine.
Then there’s the intangible effect of physically engaging with Shaper Origin. That also separates it from the CNC usual experience, because a human must drive the tool to accomplish the task.
“Operating a CNC machine feels more like printing a document than hand-writing a letter. We find that in practice, using Origin still feels human, like you did it yourself,” Hebenstreit explains. “You can see it in the face of people after they use Origin for the first time: ‘Look what I did!’ with a big smile.”
The company is in the process of shipping its first batch of Origin machines to pre-order customers, and Hebenstreit anticipates that it will be available for direct fulfillment by March of next year. He points out that the tool is also designed, developed and assembled in the USA from components sourced globally. You can watch a number of in-use applications of Origin that demonstrate its versatility. Among them is a video of an on-site wood floor repair (click here), engraving the knob of an axe handle (click here) and cutting mortise-and-tenon joints (click here).
“With Origin, we’re combining the intuitiveness of a hand-operated tool with the precision of a digital fabrication tool,” Hebenstreit says. “We’ve worked hard to ensure the technology fades to the background, but also ends up making you feel like you have a new workshop superpower.”
Learn more about Shaper Tools and Origin by clicking here.