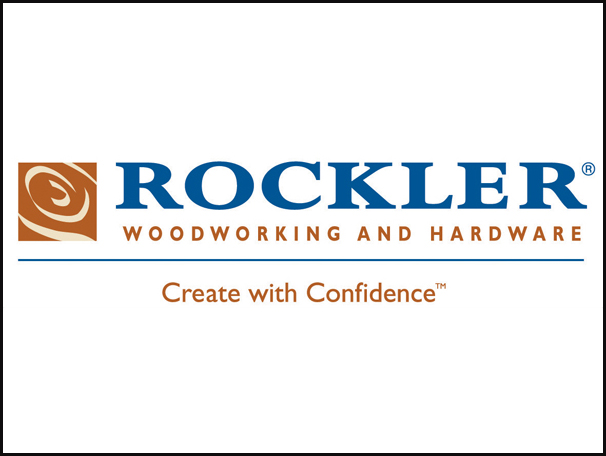
For Steve Krohmer, vice president of merchandising and product development, and the rest of Rockler’s product development team, creating new and better widgets for woodworkers is the marching order every business day. And, on many levels, that’s no small challenge.
“In the product development community, we often hear it takes 100 ideas to come up with one really good product,” Krohmer says. “I think we have a higher hit ratio than that, but it does take a lot of ideas before you end up with one that hasn’t already been developed, that meets a real need, and that can be manufactured at a cost that allows us to make a profit and sell it for a reasonable price.”
Still, for more than 60 years, Rockler has been pushing the envelope with new and innovative products that make woodworking more enjoyable, safer and accessible for everyone. Take, for instance, Rockler’s new Bandy Clamps™ (item 54258). If you’re familiar with the typical three-way metal C-clamps for installing edge banding, Rockler now offers a fresh take on a clamp style that’s been in need of improvement for a very long time.
There are several problems with conventional screw-type, three-way clamps. First, they’re difficult to install when working alone. You have to hold the edge banding with one hand, position the clamp and then tighten at least two screws to hold it in place. Once installed, the metal clamp heads don’t always provide enough grip strength to press the edging material or a face frame firmly against the contact surface without slipping. And, if you should happen to overtighten the clamps to compensate for this situation, they can mar the work surface. All in all, using these old standbys can be frustrating.
Bandy Clamps, by comparison, are based on lightweight plastic spring clamps instead of C-clamps. Between their jaws, a rubber band-type web stretches to form the lateral force that presses edging material against the substrate. The reinforced pliable web offers several advantages, Krohmer explains. First, it eliminates the risk of denting the molding or other edging material being applied. It also conforms to multiple profile shapes, and even to live-edge strips, while still applying enough pressure to hold them in place.
During the early prototyping stages of Bandy Clamp, Krohmer and his team tried to “dumb down” the design as much as possible to land on a simple, low-cost solution. One idea held promise: using a heavy-duty rubber band and an ordinary spring clamp together. But, the approach still turned into a three-handed juggling session of positioning the band, clamp and edging.
“The concept was a great idea but nearly impossible to use, especially if you need more than one clamp for the task, which you always do. The glue would be dry before you’d get all the clamps in place!”
But, attaching the webbing directly to the clamp jaws provided a straightforward solution, simplifying a three-handed job to two. Installing edging with Bandy Clamps is as easy as squeezing the clamp open, pressing the webbing against the molding and releasing.
“It takes two seconds, literally, to clamp edging to plywood with the Bandy Clamp,” Krohmer says.
Gripping strength proved to be another early challenge. To compensate, Rockler has enlarged the pads on Bandy Clamps so they’re significantly bigger than those on a standard spring clamp. “Then we added a non-slip material to the jaws, somewhat like the material we use on our Bench Cookies, to make them super grippy.”
Since Bandy Clamp’s launch this past spring, Krohmer says customer response has been very positive and has included “Why didn’t I think of that?” as the general sentiment. “It’s so easy to use, doesn’t damage the molding and is inexpensive. Why wouldn’t you use a Bandy Clamp?” he adds.
Also new in the product inventory this summer is Rockler’s Dust Right® Universal Small Port Hose Kit (item 48212). If you’ve ever tried to connect your router or random-orbit sander to a shop vac hose, the usual problem may have presented itself immediately. Unless your tool came with an adapter, you may have had to resort to your own devices to make that coupling possible. From brand to brand and tool to tool, dust port sizes and shapes vary widely.
“We’ve all dealt with the ‘Brand X vs. Brand Y’ hose sizes and port shapes. Trying to keep the right hose for the right tool handy when you need it is nearly impossible. And in reality, we give up, put on a dust mask and move on.”
The challenge of connecting tools to dust collection is one Rockler has been addressing for years with its Dust Right® product line. The new Universal Small Port Hose Kit actually is based on the same general principle as Rockler’s Dust Right Tool Port (item 25516). Similar to a plumbing fitting, the Tool Port has a heavy but flexible rubber boot that conforms to different machine port sizes. The Port’s other plastic end has a 4-in. fitting that connects to Rockler’s Dust Right Handle (item 22643), effectively standardizing any stationary tool for dust collection and also providing a quick-release function for the dust hose.
In lieu of there being a universal port size or sizes for smaller power tools, Rockler’s new Small Port Hose Kit provides similar adaptability. The kit comes with two flexible boots that have 1-in. and 1-1/2-in.-diameter openings. The stretchable material can bridge many tool-port sizes and shapes. That makes tool-specific, hard plastic adapters unnecessary.
“When we were exploring different tools on the market, we realized that these two (boot) sizes would cover 99 percent of the tools … The wall thickness is actually designed so the boots not only fit over most ports, but they actually fit inside others.”
The other end of each boot reverse-threads into a length of premium hose (included) that stretches from 3 to 15 ft. It connects to a standard shop vac hose with a 2-1/4-in. swiveling port.
Krohmer says that while many of Rockler’s product innovations actually come from customer suggestions, the new Universal Small Port Hose Kit “was just the next problem in line that we wanted to solve” on the tool connectivity front. But he adds, customer input and suggestions for new products is vital. “We love getting new ideas from woodworkers and working with them to develop new Rockler products.”
“We can make anything we develop,” Krohmer adds, thanks to Rockler’s team of industrial designers, working with its partners in manufacturing. “The key, really, is getting the ideas to work with.”
Innovation is a commitment that motivated Rockler to create its product development team, “and it drives everything we do,” Krohmer says. “The entire company has a passion for woodworking and serving woodworkers. Developing our own problem-solving products is just one of the ways we continue to fulfill (founder) Nordy Rockler’s mission to serve the woodworking market.”