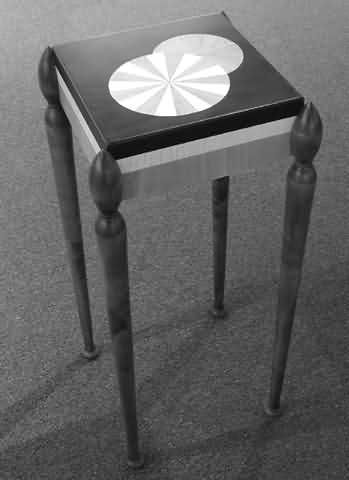
Reid Leonard had some rosewood plywood he was interested in, but when he got there, it was all out. The guy talked him into some veneer. “I didn’t know anything about veneer, so I took a whole bunch of it home and started playing with it,” says Reid.
The table business took off at least ten years later when his son moved into town. He had been working in a furniture factory, so he had a lot of knowledge about production techniques and economies of scale. He runs his own shop in Pensacola and Reid now works for him. Together they designed what Reid calls October Tables. His son does a lot of the assembly and the whole operation is pretty automated. For instance, the legs for the tabletops are fairly interchangeable, so the same table can be built for a foyer, with long legs, or for other uses when paired with shorter legs.
Reid does all the veneer work and all the designs. “Those patterns are complicated,” he admits, “some of those are sons of guns to make.” He says that he’ll feel like he knows what he’s doing in another 20 years.
The October tables were ideal for many reasons. In terms of taking work to shows, they were easy to carry and sold pretty well. They also gave Reid a palette for the wide variety of design trapped in his head. With more than 900 tables to his credit, he says he rarely uses the same pattern twice.
But with 30 years to collect veneers and more than 150 different varieties in his workshop, he’s got a lot of material to work with. For example, he just came across a log of, get this, bird’seye eucalyptus that is being cut into veneer. It’s hard to know where it came from, he admits, because the importer was in Spain and the veneer mill that cut it was in Switzerland. It could be from Australia, but he can’t be sure. “This is the neat thing about the veneer business ? sometimes I think they ship the veneer around the world a couple of times,” says Reid. According to his sources, this is the first time in 18 years anyone has seen bird’s-eye eucalyptus.
But that’s not the rarest veneer he’s ever encountered. He actually still has some tortoise shell poplar from a tree cut 30 years ago. It was, says Reid, a strange green poplar that acquired a blister pattern that emulated a tortoise shell. “I just collect veneers,” says Reid, “I guess it’s gotten out of control.”
The chemist in him comes out when you talk about adhesives and finishes. When he was first playing around with veneers, he used contact cement. Now he uses urea formaldehyde with a cold catalyst. That gives him plenty of time to set things up. Then he clamps it up in a screw press – he almost never uses a vacuum press – and leaves it over night. The press he and his son designed is 3′ by 8′, so he clamps up multiple tops at the same time and cuts the board into table tops after it dries. He also runs a dehumidifier in the room as the veneer sets.
In terms of finish, he and his son have recently hit on the Gougeon Brothers’ West System®, an epoxy resin that they need to load on the tabletops with a trowel. It’s a finish from the world of marine finishes and actually sinks into the wood somewhat. After it cures, they just do a quick spray with catalyzed varnish with no rubbing.
Reid just returned from the home show in Charlotte and has been going to the Philadelphia show since its first year. The shows tend to be expensive compared to the sales, but it does give him a chance to hunt out even more veneers. “This really isn’t a hobby anymore,” admits Reid.
– Bob Filipczak