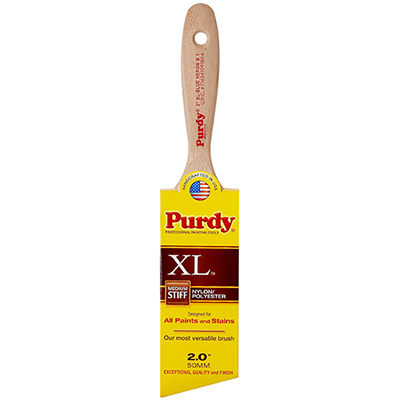
Last month, my son and I each made a brush. Not just any paintbrush, mind you, but a top-of-the-line, handmade, alderwood handled, natural white China bristle, butt chisel varnish brush.
We visited the Purdy brush company in Portland, Oregon, where technical support manager Bruce Schneider gave us a tour of the facility, then sat us down with a veteran brush maker for a hands-on lesson. If you’ve read my books or articles, you probably already know that I am a devoted fan of Purdy brushes, and use them almost exclusively. That’s because I’ve long felt they are the best brushes on the market. Now, having seen how they are made, I understand why.
The most telling thing about this 80-year-old company is that even in this day of sophisticated machinery and mass production, Purdy brushes are still made by hand. The assembly section of their ultra-clean and well ordered facility reminded me of a Cuban cigar factory, with rows of artisans sitting at small tables, turning out handmade brushes, one at a time. Each bench had fairly primitive tools; a scale, some sized rods, a level work surface, and a splitter jig for setting wedges.
The process starts when the hair or fiber enters the building. Purdy makes both natural bristle brushes, using hog and ox hair, and a host of synthetic fiber ones. They buy several types of white and black Chinese hog hair, called China bristle, and ox hair, which is much softer. The synthetic bristles are custom-made for them in a variety of materials, each crafted for specific characteristics.
Natural brushes are considered the best for solvent and oil based coatings, but because they get floppy when wet, are not used with waterbased finishes. Synthetic bristles run the gamut from resilient and springy to buttery soft. Syntox, one of Purdy’s newer offerings, is considered the best of both worlds. A synthetic fiber mix that will work with waterbased coatings, it is soft enough for oil based, cheaper than natural fiber, and lasts longer to boot.
All incoming bristles get inspected for length, quality, suppleness, and taper. Natural hair tapers toward the tip, while synthetic fibers are crafted to do the same thing. Both types are measured to ensure the taper meets Purdy’s specifications. Only fibers that pass their tough standards are kept for use in brushes. Ultimately, the big end of the hair will go toward the handle, and the taper toward the tip of the brush.
“We ‘flag’ our synthetic filaments to imitate natural China Bristle” Schneider told me. “This creates a razor sharp cutting edge and gives the painter more control over the application of any finish.” Flagging splits the ends of the fiber into several fingers, making it less likely to leave brush marks. It’s what hairdressers call “split ends.”
Various fibers are sorted and mixed for the many styles of brushes, then piles of hair join bins of ferrules, wedges, and clips at the assembly tables.
Taking care to keep all the thin ends in one direction, a brushmaker weighs out just the right amount of hair, deftly slips it into the ferule, levels it, and inserts a wedge. The tapered wood wedge, one in most brushes but two in larger ones, forms a hollow area in the center of the brush to help hold and deliver finish evenly.
Good varnish brushes are always chisel shaped at the tip. While some companies cut the chisel, ruining the fine tapered end, Purdy builds it into the body of the brush. “Rather than cutting the chiseled round top shape into the brush we actually pull the chisel into the tool by hand with what is known as a pull down. This leaves the tip and flag intact,” explained Schneider.
Creating that butt chisel was the hardest part for me, and on my brush, I had to redo that step several times. Once the shape is right, the bristles are gently combed, then a retaining clip is inserted before it goes to the plugging station. There, a specially formulated epoxy seeps around the base of the hair to hold it firmly in place so the bristles won’t come out while you are working. An alderwood handle is added, and the brush goes through cleaning and “breaking in” processes before it is packaged. Each brush is inspected at every step in the process, and again at the end, so that each Purdy brush is perfect.
So, how was my handiwork? In spite of our kindly teachers telling us “you did great for your first brush,” I know better. I’ll keep the brush I made, but I doubt that I will use it. After all, I’m used to a much higher standard. I’m used to Purdy brushes.
For more information about Purdy brushes, visit their web site at http://www.purdycorp.com/.