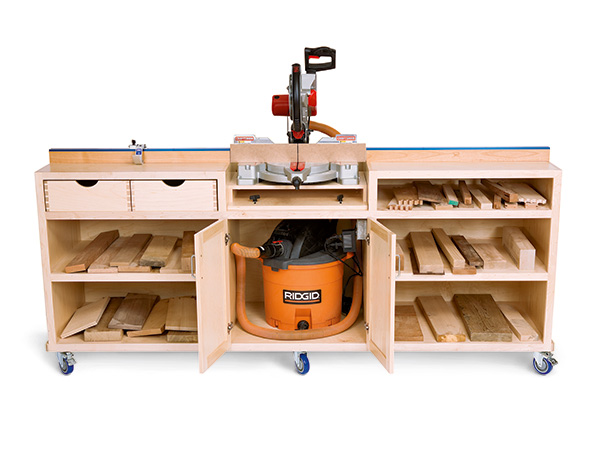
For all sorts of cross- and angle-cutting tasks, a miter saw is a woodworker’s friend. But, to really maximize its potential, you need a good home base for your saw — and that’s what this project delivers. It addresses what I feel are a miter saw’s biggest needs. The stand is a full 8 ft. long, in order to provide generous support tables on either side of the saw. They’ll help you cut down long stock with ease.
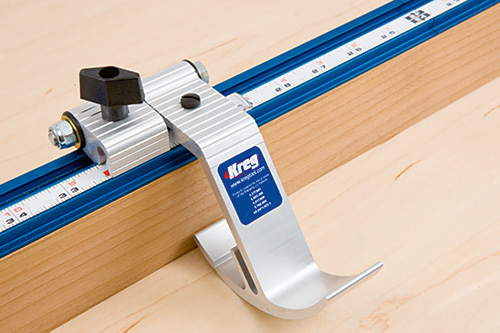
I’ve equipped the support table fences with Kreg’s aluminum track system and flip stop, for setting up precise cutoff lengths or carrying out repetitive cutting jobs. You’ll also notice that the saw is mounted on a center platform that slides back and forth and locks in place.
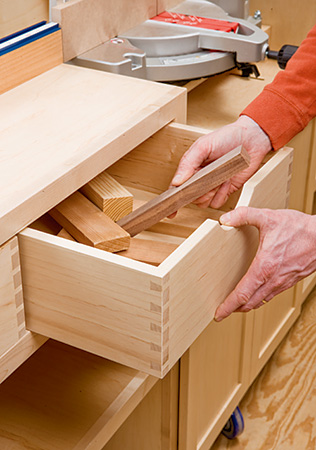
It enables you to mount a backup board directly to the saw’s metal fences for tearout-free cutting, then align the saw flush with the project’s fixed fences. When you need to tilt the machine for bevel cuts, just pull the platform forward of the fences and tip the saw as usual. No versatility lost here.
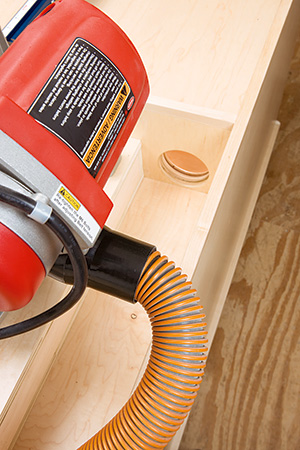
While a miter saw’s bag captures some sawdust, a shop vacuum works much better, so I’ve sized the stand’s enclosed cabinet to fit a vac with up to a 16-gallon capacity. The saw turns it on, thanks to a tool activated switch inside.
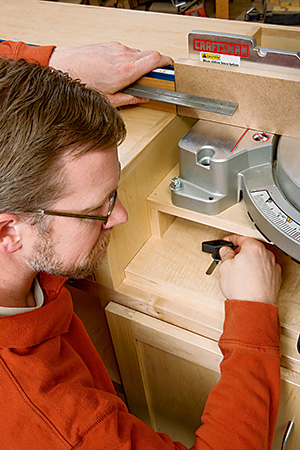
And, although you can’t see it in this large opening photo, a trough behind the saw helps collect whatever the shop vac doesn’t. A chamber runs behind the left support table, with openings on both ends, so you can hook up your dust collector and whisk the trough clean.
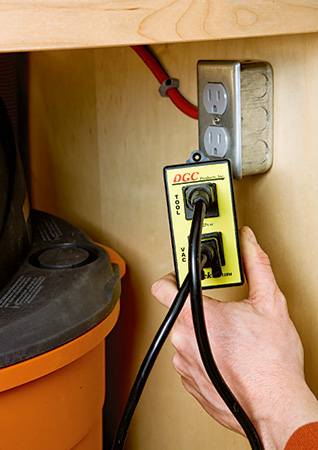
Six fixed shelves give you plenty of room for cutoff storage; I’ve even added two pull-out bins to mine that store those shorter scraps I can’t bear to throw away. Plus, heavy-duty casters make the cart easy to roll around when necessary.
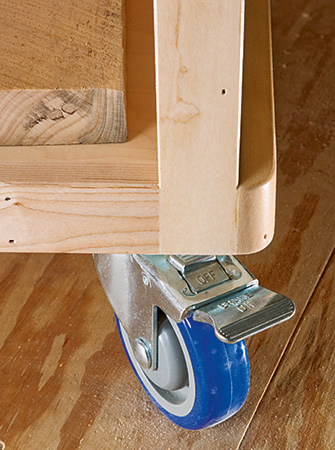
Ready to build one of these souped-up stations for your shop? Let’s get started!
Assembling the Carcass
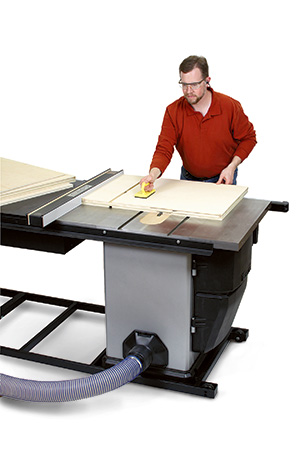
Follow the Material List dimensions to make six panels for the sides and dividers (pieces 1). I cut the two outer side panels to final size right away, but notice that the dividers are doubled up to form the walls of the inner cabinet. So, I cut two dividers to dimension, glued them to slightly oversized mates, and then used a flush-trim bit in my handheld router to bring them to a perfect matched fit. Take these four components to your table saw to mill dadoes for the four fixed shelves, plus the center panel that supports the saw platform. Refer to the Drawings to cut two large holes in the left divider and side panel for the dust chamber openings. A 3-1/2″-diameter hole saw in your drill press will do it nicely. Ease the edges of these holes.
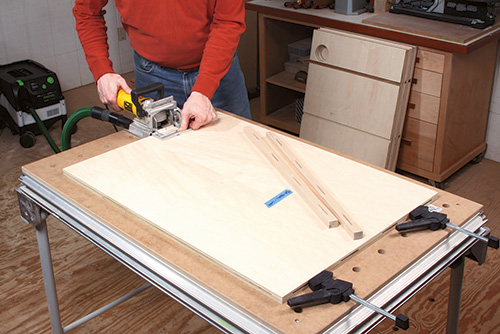
Set these panels aside, and cut the long top panels and back panel to shape (pieces 2 and 3). Although my buddy Bruce Kieffer favors thinner edging for his plywood projects, I like the durability and look of thicker edging. So, I wrapped the ends of the top panels, as well as the top and ends of the back panel, with beefier strips (pieces 4). Attach them with glue and #20 biscuits.
While the glue dries, you can proceed to cut the cabinet bottom, fixed shelves, short top panel and dust chamber wall (pieces 5 through 8) to shape. Bore a hole for your shop vac hose in the short top panel near the back right corner. As tempting as it may be to dive into the big assembly, the smarter approach is to sand all the inside surfaces of the cabinet panels now and finish them while the faces are still fully accessible.
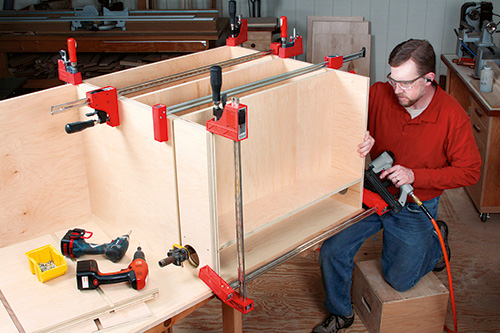
The carcass actually goes together quickly; you can form the joints with #8 countersunk wood screws or 2″ brad nails. No glue is really necessary. Here’s the process I followed, building one end of the cabinet, then the other: Screw the side panel to the bottom panel, then fasten the back panel to these two with more screws. (Note: The back panel extends below the bottom panel by 3/4″ to allow room for the bottom cleats, later.) Slip the shelves into their dadoes in the side panel, and set the divider into place. Drive screws through the divider’s top dado to pin it to the top shelf, and lock the shelves to the side panel with more brads. If you’re starting with the left bank of shelves, fit the dust chamber wall into position on the top shelf; attach it to the divider and top shelf with screws and to the side panel with brads. Now, repeat this whole assembly process on the other end of the cabinet for the side, shelves and divider.
When all of these components are fastened, slide the short top panel into place between the dividers. Attach the dividers, short top panel and shelves to the bottom and/or back panels with screws. Finally, seal the joints of the dust chamber with a bead of caulk before capping off the shelf banks with the two top panels. Use countersunk screws driven down into the dividers, sides and dust chamber wall, as well as through the back, to secure these joints. Cover all of the screw holes with wood plugs, and sand them flush when the glue dries. Your project is rolling along nicely now.
Adding the Face Frame & Wheels
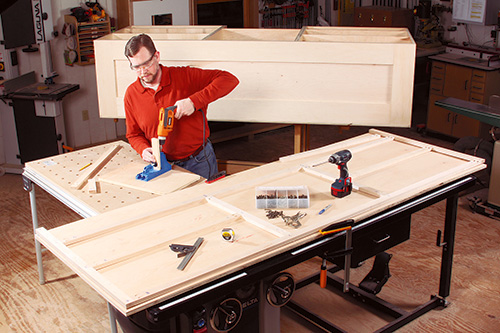
The face frame is a straightforward assembly. I built it entirely with pocket screws. But, before you rip and crosscut all of the face frame components (pieces 9 through 13), let me make a suggestion: while the Material List specifies that all of the face frame parts are 1-1/2″ wide — which on a perfect carcass will work just fine — make the short top and long bottom rails about 1/16″ wider and the end stiles about this much wider and 1/8″ longer than listed. That way, you’ll build in some “fudge factor” to adjust the finished frame on the carcass when it’s assembled.
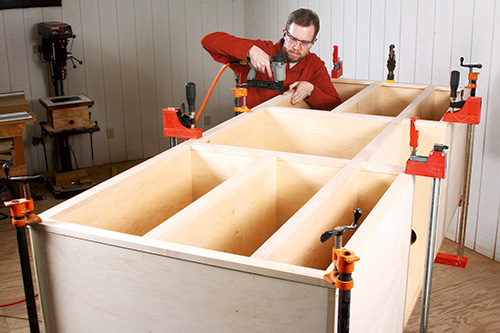
Cabinetmakers do this all the time. Trim and fit your face frame parts right on the carcass, holding them in place with clamps as needed, so you’ll be assured of their exact placement. Once all of the parts are created, label every joint carefully to keep their orientation clear before removing the loose rails and stiles and boring your pocket screw holes. Assemble the face frame with screws on a large worksurface. Then set and clamp it into position on the cabinet, and nail it home. Remove any overhang on the top and sides of the face frame with a trim router, block plane or belt sander.
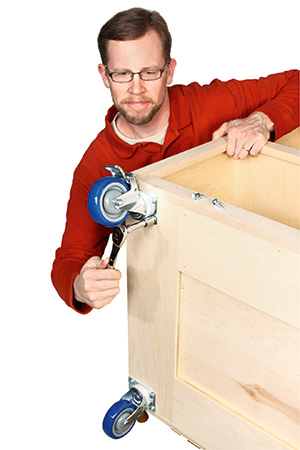
At this point, you’re nearly ready to tip the project upright — and you can leave it that way for the remainder of the construction process if you install the long and short bottom cleats (pieces 14 and 15) and the six casters (pieces 16) now. I glued and nailed the cleats in place and mounted the casters with 1″ lag screws and washers. Grab a buddy to help you right the stand onto its wheels. Add the side and back skirt boards (pieces 17 and 18) to hide the ends and edges of the bottom panel and cleats; I rounded the ends of the side skirt boards first at my disc sander before gluing and nailing the skirting in place.
Building and Hanging the Doors
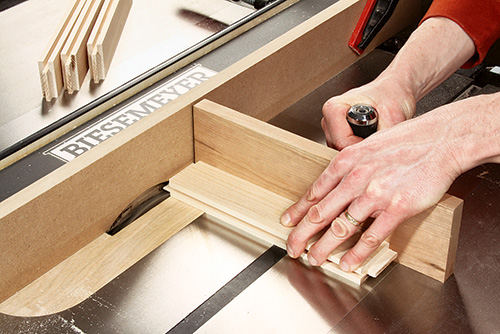
After all this big-panel construction, the doors will probably come as a pleasant reprieve. Cut the stiles, rails and door panels (pieces 19 through 21) to size, and head to your table saw to mill the panel grooves and stub tenons that hold the doors together. If your door panel plywood is slightly thinner than 1/4″ — and these days, it usually is — cut the rail and stile grooves to fit the panels snugly. Make the stub tenon thickness on the ends of the rails match the groove width, and mill the tenons 3/8″ long. Sand the door parts thoroughly before gluing and clamping them together. Follow the instructions that come with the 1/2″ overlay Euro hinges (pieces 22) that will mount these doors to the face frame.
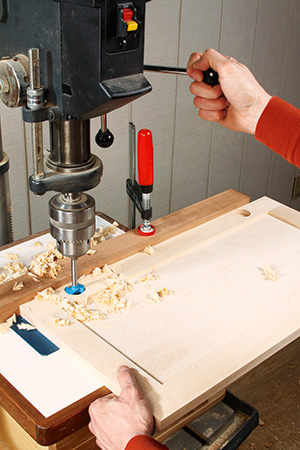
You’ll need to bore pairs of 35mm hinge cup holes into the door stiles, attach the hinge hardware and then mount the hinges and doors to the cabinet. It’s easier to do than you might think. Once the doors are in position on the project, adjust the hinges to align the doors with one another. Go ahead and install the door pulls, too (pieces 23).
Making the Saw Platform
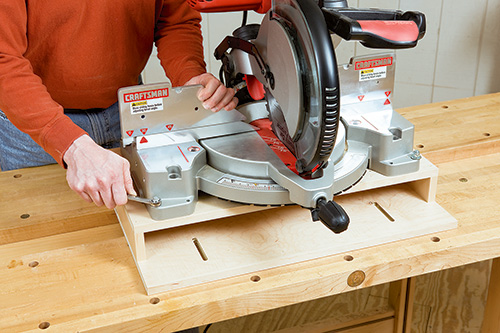
It’s time to outfit your saw for its new home, and that means building the moveable platform. Cut the platform base (piece 24) to size, and mill two slots for hanger bolts with a 3/8″-diameter straight or spiral bit in your router table. Now, glue strips of edging (pieces 28) to the base as well as to blanks of plywood for the platform top and sides (pieces 25 and 27). Trim the edging flush. Before you cut the sides and back (piece 26) to final width, verify this measurement considering the exact height of your saw’s base; you want to make sure the saw will meet the support tables flush when mounted on the platform. Sand and finish the platform parts now before screwing or nailing it together.
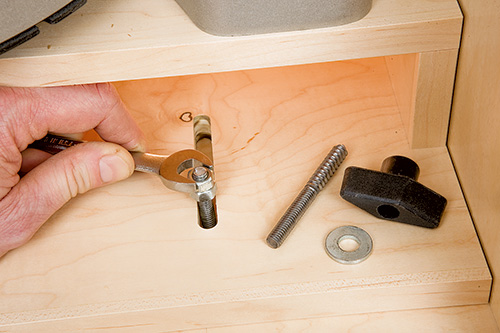
Drill holes in the platform to suit your saw’s mounting configuration, and bolt the saw to the platform. I used carriage bolts, washers and nylon lock nuts. Now, set the platform into place on the cabinet, and use the slots to reference where to drill pilot holes for the hanger bolts (pieces 30). Locate the bolts 4-1/2″ from the front of the cabinet. Before drilling those holes, fasten a backer board (piece 29) up inside the cabinet to give the hanger bolts a thicker mounting substrate. Install the hanger bolts.
Adding the Fences
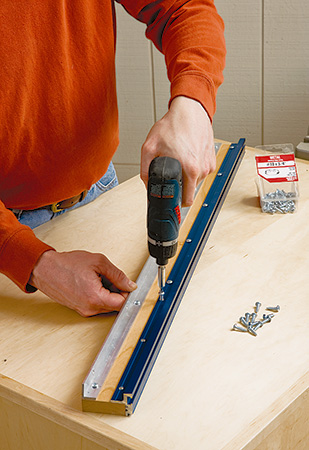
The fences consist of three parts: a wooden body (piece 32), a strip of aluminum angle (piece 33) that secures it to the cabinet and, of course, the Kreg aluminum flip-stop track on top (piece 34). Cut and assemble these fence parts with #10-3/4″ panhead sheet metal screws to create two long fence units. When mine were ready, I mounted them 9-1/2″ back from the front edge of the support tables with more panhead screws.
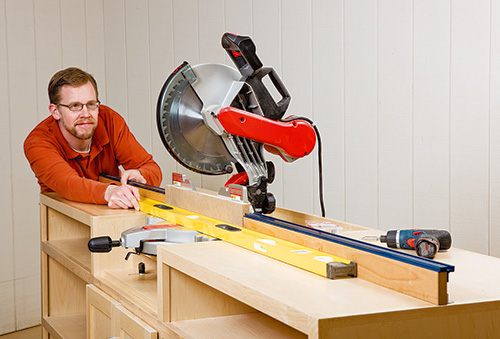
That fence placement enables my 12″-diameter miter saw to crosscut stock to its full capacity. It also allows enough room in the hanger bolt slots to move the platform backward for attaching backup boards to the saw fence or forward for opening the saw’s fences to make bevel cuts. You may need to adjust the location of these two fixed fences to suit your saw’s styling and cutting range.
Wrapping Things Up
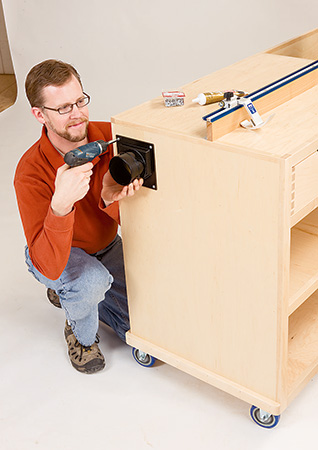
Whether you build scrap bins for your project like I did is up to you; you might want to devote the entire shelf space to longer cutoffs. If you do build bins, I sized mine to 15-3/4″ x 18″ and used through dovetails for joinery. There are measured drawings for the bins online.
As far as electricals go, I think Rockler’s i-Socket (piece 35) is a great add-on to this stand, because it activates the vacuum every time you squeeze the saw’s trigger. But, you’ll need to install a receptacle and long cord inside the cabinet to plug in the i-Socket, or use a power strip. I chose the former option and wired my outlet with a length of 12-gauge extension cord and male plug. It can handle the start-up amperage of both tools.
With all of the inside details now completed, give the outside of your project a thorough sanding, and apply finish to whatever surfaces are still bare. Install the dust port (piece 36) over the dust chamber hole on the left side of the cabinet with a bead of caulk to create an air seal, and attach it with four screws.
Whew, this was a big project, but one you won’t regret building. Now you’ve got a full-duty miter saw station and a handsome shop addition to boot. I hope you enjoy using it!
Click Here to Download the Drawings and Materials List.
Hard-to-Find Hardware:
4″ Caster (Locking) #23030
4″ Caster (swivel) #22410
1/2″ Overlay Face Frame Hinges #55910
Hanger Bolts (8 pack) #24430
i-Socket Switch #20890
Kreg Top Trak (2 required) #26358
Kreg Flip Stop #21938
Self-Stick Rule (L to R) #69116
Self-Stick Rule (R to L) #69124
Dust Right Combo Port #28666