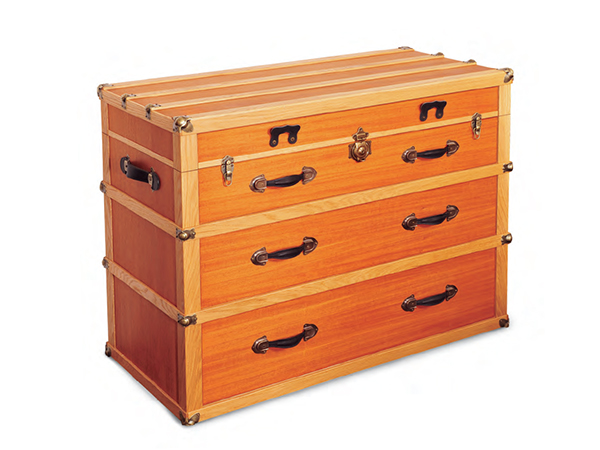
I always try to keep my promises…even if it takes me years to do so. Some time ago, I promised my wife that I’d build her a large dresser to replace the less-than-attractive modular wire bin unit that she’d patiently kept her clothes in (I’m pretty sure that’s grounds for divorce in some states, but fortunately, my wife is very understanding). Anyway, this past summer I decided to build the piece in time for her birthday. One challenge I had was coming up with a design that fit in with both the ornate antiques and modern furnishings we have in our bedroom.
A flash of inspiration came one day when I ran across some photos of Victorian-era steamer trunks on the website of a company that sold all the hardware necessary for restoring old trunks. What I like about these vintage travel chests is that they ooze nostalgic elegance yet they look right at home in a contemporary décor. It struck me that the arrangement of wooden slats and leather handles on the front of some trunks made them look a bit like they had drawers (they don’t — they’re all chest-like lidded trunks). A few sketches later, and I came up with the steamer trunk dresser design.
The piece is constructed like a basic modern dresser: A plywood carcass with an inset solid-wood face frame encloses a series of plywood drawers that run on metal glides. But it’s the wood slats, antique brass hardware and leather pulls (and a few surprise touches) that really give the piece a unique appearance and functionality. It took some effort to build, but I haven’t made a piece of furniture in a long time that has evoked so many nice compliments — and my wife just loves it.
The Drawers
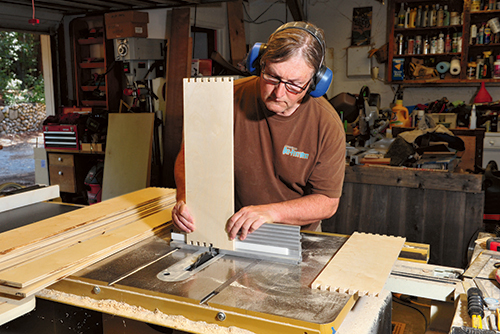
One of the really nice things about this dresser is its huge drawers, large enough to hold a ton of clothes. To make these drawers easier to install in the carcass, I constructed each drawer as a basic five-sided box — four sides and a bottom — and mounted a separate drawer face to the front (more on this later). To give these big drawers plenty of strength, the corners are box joined together. Box joints are easier to cut than dovetails, but they still add an attractive visible detail.
Start by cutting all the 1/2″ Baltic birch plywood drawer parts to size, following the Material List. You’ll notice that each of the sides, fronts and backs are 1/16″ longer than the final dimensions of the drawer. The idea is that you’ll make the pin portions of each box joint just a hair longer than the thickness of the plywood, then sand them flush after it’s assembled to get a clean final joint.
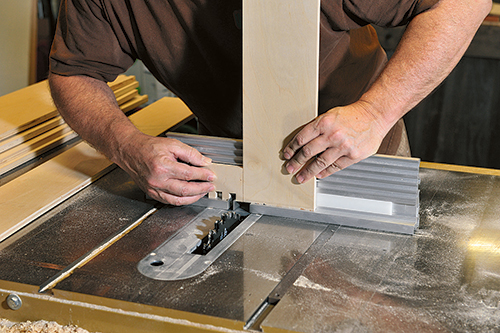
While there are many ways to cut the box joints, I prefer to cut them on the table saw, using either a commercial or shop-made sliding jig. The jig holds each workpiece vertically as it passes over a dado blade, set to cut slots 1/2″ wide — same as the pin portion of the joint. After each pass, the workpiece is moved sideways and the just-cut slot is seated onto the jig’s fixed reference pin. This pin is set so that the next cut slot cut creates a pin that’s the same width as the slot. Before cutting the drawer box parts, I make a test joint from Baltic birch scraps, to check the fit. If the joint is too tight, I set the reference pin a little closer to the blade, to make the pins a little slimmer; vice versa if the joint is too loose. I set the cutting depth of the dado blade so that each slot is cut 1/32″ deeper than the thickness of the plywood (to allow flush sanding later).
To keep things consistent and avoid joint cutting errors, I mark the top edge of each drawer back, front and side and always cut each joint starting from the upper-facing edge of the piece. I start by cutting all the drawer sides first. With the end of the side down in the jig and the upper-facing edge set flush against the pin, I cut the first slot, then slide the part over until the slot is on the jig’s reference pin and take the second cut. The process is repeated until all the slots/pins are cut.
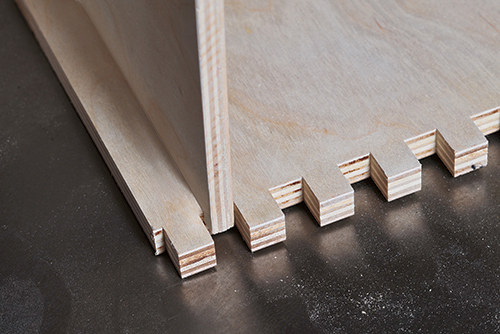
Once all the sides are done, the drawer fronts and backs are cut inverse to the sides, so that the joints interlock. This requires the use of a spacer — a short scrap of drawer stock that has been cut on the jig. Slide the spacer over the jig’s reference pin, then butt the top edge of the workpiece right up against it. Now remove the spacer and cut the first slot. Then, slide the part over the reference pin, and continue cutting as you did before.
Once all the joints are cut, plow a groove on the inside surfaces of the drawer parts to capture the drawer bottom. Because of the size of the drawers, I like to use 3/8″ thick (9.3mm) Baltic birch stock, which will support a good deal of weight without sagging. Using a dado blade in the table saw, plow a groove on the lower inside face of each drawer side, front and back part. The groove should be centered between two pins on the drawer’s front and back. This hides the groove on the sides of the assembled drawer.
Sand all the drawer parts smooth, then carefully dry-assemble each drawer box, to make sure that the bottom fits and that all the box joints go together easily (they’ll be tougher to put together after the glue swells the plywood). Working atop a bench or other reliably flat surface, brush glue into the joints on the two sides and the back of a drawer box, then assemble them. Now slide the drawer bottom into its groove and glue the front side of the drawer in place. Before applying clamps, check the squareness of the assembly by measuring its diagonals; they should be equal. Once all four drawers are done and the glue is dry, use a belt sander to sand the corner joints until all sides of the drawer are smooth and flat.
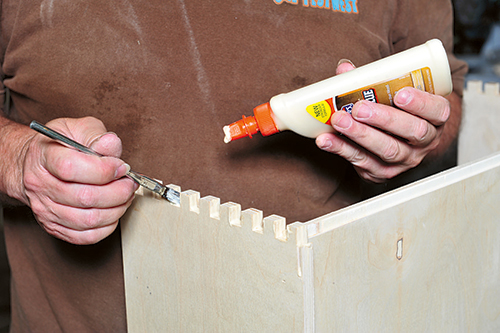
Now is a good time to cut out four drawer faces from the same plywood stock chosen for the dresser’s carcass. To hide the bare plywood edges, cut and plane some 1/8″-thick, 13/16″-wide banding strips from solid stock that matches the plywood. Brush glue sparingly on both the strip and plywood edge, then tape it in place. I recommend gluing the strips on the ends of the drawer faces first, then trimming them flush before gluing on the longer strips.
Building the Carcass
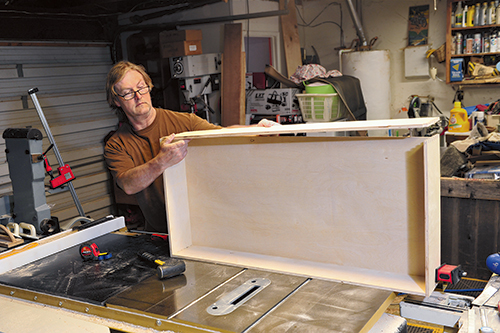
The carcass of this dresser is really very basic, consisting of just nine parts: A top, bottom, two sides, a back and four internal stretcher strips. Cut the top, back and sides out of a nice sheet of 3/4″ hardwood plywood, following the dimensions listed in the Material List. (I chose mahogany, one of my favorites.)
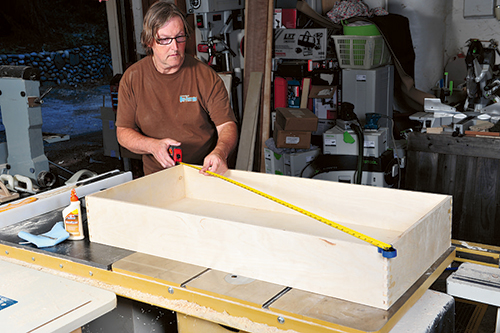
Also cut the four stretcher strips from any good 3/4″-thick plywood you have on hand. Now plow a 1/4″ wide, 3/8″ deep rabbet on the inside-facing, back edge of the top, bottom and sides (see the Drawings), using a dado blade in the table saw.
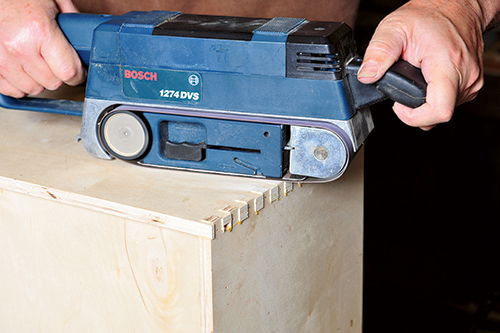
All the carcass parts are joined using biscuits. To make cutting the slots quicker, I first mark a scrap stick with the center points of the five #20 biscuits spaced evenly across the width of the carcass. Clamp this stick atop one of the dresser sides and plunge cut the slots that join the bottom into the inside-facing surface of the panel using a biscuit joiner.
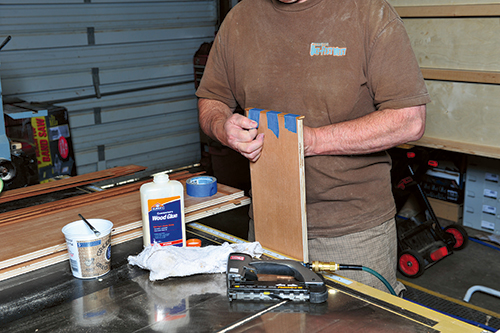
Now cut the slots for the stretchers, which are positioned as shown in the Drawings. Cut slots for joining the carcass top into the top edges of the sides, using the same biscuit spacing. Once both side parts are done, plunge cut the slots on the ends of the dresser bottom, and bottom-facing side of the top. Finally, cut a single centered slot on each end of all four stretchers.
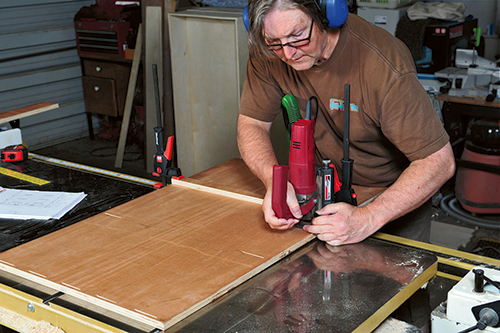
Assembly of the carcass is done as a two-part operation. First, the bottom and sides are glued together, along with all four stretchers. Dry assemble the parts to check their fit and make sure you have all the clamps (or extra sets of hands) you need before you start the glue-up.
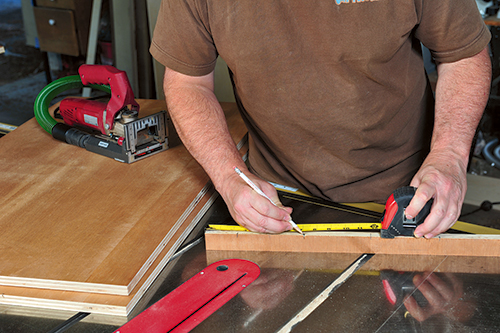
It’s easiest to set the whole assembly upside down on the floor and use bar clamps against scrap wood clamping cauls, to protect the plywood. Make sure that all the edges of the carcass are flush and allow the glue to cure.
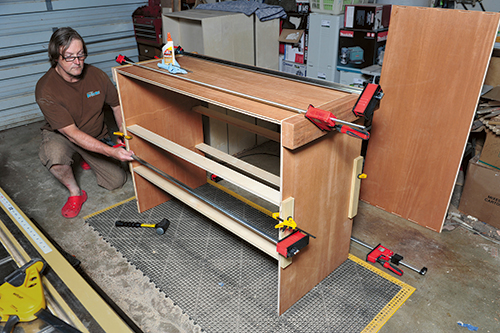
The second assembly step is to clamp the top onto the sides. As always, test fit the top first, to assure that its ends are perfectly flush to the sides. Then glue in the biscuits and clamp the top on, once again using bar clamps and cauls.
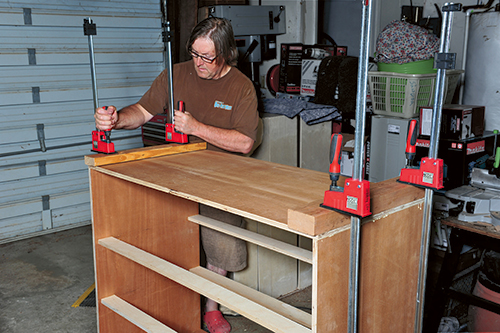
At this point, carefully finish sand the outside of the carcass (not the edges!), taking care not to sand too enthusiastically, lest you go through the plywood’s thin face veneers.
Add the Face Frame
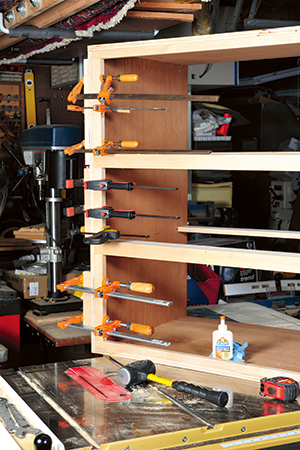
To add stability and strength, the carcass is next fitted with a face frame cut from a 3/4″-thick secondary wood. I used alder, but any wood that matches the tone of the wood you choose for making the slats is just fine (the reason for matching tone is that the frame may be seen slightly when the drawers are closed). Because the frame is inset into the front opening of the carcass, I don’t feel there’s a need for adding joinery to the frame members — believe me, the final assembly is notably strong. Start with the long frame rails, crosscutting each piece a tad overlong, then trim it until it fits snugly into place. The two 1″-wide rails fit at top and bottom; the 13⁄4″ rails get glued to the stretchers, with each rail’s top edge flush with the top of the stretcher. Next, cut, trim and glue in place the face frame stiles that fit along the inside edges of the sides between the rails. Make sure each stile member is flush with the face of the rails and plywood edge of the side before clamping it in place.
Fitting the Drawers and Slides
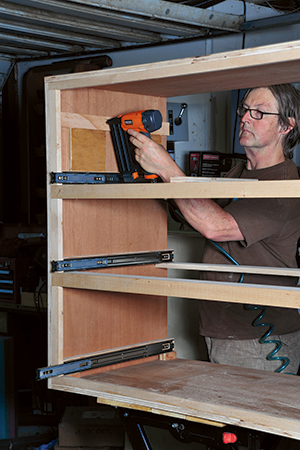
To allow total access to each of the large drawers, I hung them on full-extension drawer slides. In order to mount the glides flush with the inside of the face frames, 1-1⁄4″-thick spacers must be added to the inside of the carcass. The spacers for the two middle drawers are glued and nailed directly atop the stretchers. The bottom drawer spacer is positioned 1″ up from the carcass bottom. Use a pair of 1″-wide scraps to hold each spacer in place as you secure it. Use a pair of 5-5⁄8″-wide scrap blocks to position the spacers for the top drawer glides. Place the scrap blocks atop the spacers for the upper middle drawer, then fasten the top drawer spacers in place.
To attach the drawer slides, first separate each one into its inner and outer halves. The wider outer portion of the glide mounts on the inside of the carcass: Position each one so that its lower edge is flush with the bottom of the spacer and its front edge is 3/4″ back from the front of the carcass. For now, attach each slide with two screws driven through the horizontally-slotted holes, to allow front-to-back adjustments of the drawer later.
The narrow inner half of each drawer glide mounts to the sides of the drawers themselves. First, mark a line parallel to and 3/4″ up from the bottom of each drawer. Then, position the slide with its screw holes centered on this line and its front edge flush with the front of the drawer box (sans drawer face). Use two of the vertically slotted holes to screw each slide on to allow for vertical adjustments of the drawer.
Now slide all the drawer boxes into the carcass. The two halves of each slide should fit together easily. If the side-to-side fit is too loose, you may need to shim the spacers out a little. Each drawer box should be roughly level and parallel to the face frame rails. If it’s not, adjust the narrow glides up on one side or another as needed.
Mounting Drawer Faces
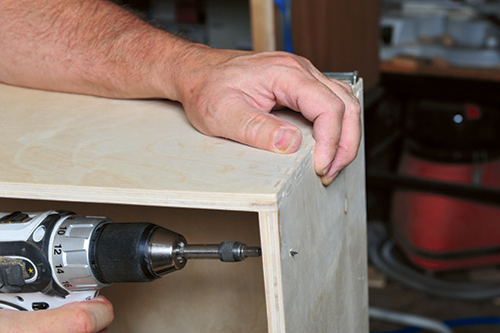
Now it’s time to mount the drawer faces to the drawer boxes. Start by boring a few pairs of holes through the front of each drawer box. Drill from the inside using a #8 countersinking drill bit. Drive a 1″ long #8 flathead screw into each hole only part way, leaving just about 1/8″ of its tip protruding. Slide the drawers back into the carcass, then carefully set the drawer faces into their frame openings, setting each atop a 3/32″ strip of wood to shim it up from the frame rail below it. For the top drawer, set your shim strip directly on top of the face of the drawer just below it to get the right spacing. Center each face in its frame opening, then use a couple of strips of wide masking tape to hold it in place. With one hand over an end of a drawer face, reach around back and give the drawer box a light but solid whack with a mallet. Repeat at the other end of the drawer, then do this with all the drawers. These hits should drive the tip of the screws just far enough into the back of the face to provide an exact positioning reference. Remove all the faces and drawers, and set each face on its drawer box until you feel the screw tips slip into place. Drive the screws fully home.
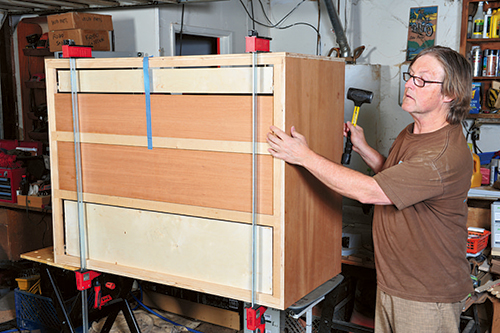
Slide all the drawers once again into the carcass and check to make sure they are still level, and that the space around each drawer face is even. Make any adjustments that are necessary by moving narrow glides up or down. Also check that each drawer closes fully. You may need to move the wide slides forward or backward slightly to adjust this. Once they’re right, drive several extra screws into the round holes in each glide to secure it.
Remove the drawers and finish-sand all drawer faces, as well as the top, sides and bottom of the carcass. Now is a good time to fit and attach the dresser’s 1/4″ plywood back by nailing or screwing it into its rabbet recess.
Adding Slats and Trunk Edges
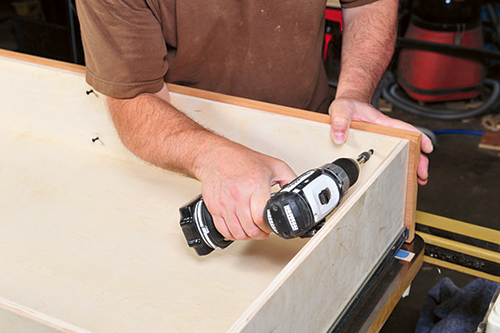
To help them stand up to the rigors of travel, traditional steamer trunks were reinforced with a series of wood slats across all surfaces. The slats were joined at the corners with “corner bumps” and “slat clamp” hardware that secured their ends and protected the trunk’s edges.
But before working on the slats, there’s one small detail to attend to: To create the illusion that the dresser is a real steamer trunk with a hinged lid, I add a groove and lip to the sides of the trunk, as well as a lip to the top drawer. With the trunk on the floor on its side, use a router fitted with an edge guide and V bit to rout a shallow, 1/16″-wide groove centered 6-9⁄32″ from the top edge. Then, rout the other side.
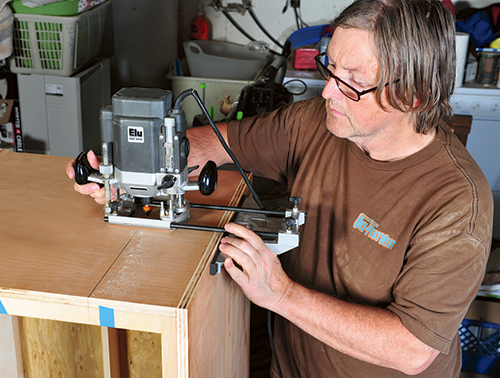
The slats for the trunk dresser are made from 5/16″-thick oak, resawn from 4/4 stock. After cutting all the long slats to length, put a 1/8″ roundover on the long edges of all the slats with this exception: round only one edge of the slats that go at the top and bottom edges of the front, sides and back. Finish-sand all the slats before attaching them. Mount the eight slats on the ends of the carcass first, using glue sparingly to minimize squeeze-out. Make sure each slat’s ends are flush with the front and back edges of the carcass. To secure the slats as the glue dries, I use a pneumatic pin gun that shoots very thin brads. The tiny holes that are left behind are virtually invisible.
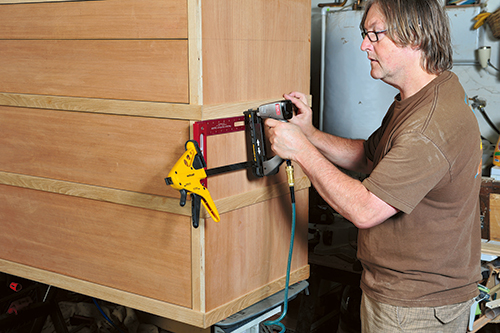
Next, cut and mount the long 1-3⁄4″-wide slats to the front and back of the dresser. Take care to keep the edges of the top slats flush with the carcass top. Once the glue dries, carefully scrape off any squeeze-out, then glue on the four 2-1⁄16″-wide slats: two at the top and two at the bottom. Finally, attach the two remaining 1-3⁄4″ slats on the middle of the top, spacing them evenly. Carefully inspect to make sure you haven’t missed any glue drips, then clean up the ends of the slats with sandpaper as necessary.
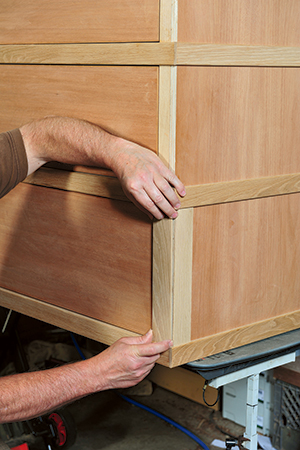
The next step is to add the 1/8″-thick wood vertical edging that fits between the horizontal slats. It’s a good idea to cut all the edge pieces just slightly over length, then trim each one to fit snugly into place. Start with the 2″-wide edges that go on the dresser’s sides. Sand each slat before gluing it in place and position it with its outer-facing edge flush with the carcass. Then secure it, either with a gun-driven pin or with masking tape. Make sure to leave a 1/16″ gap between the two upper-most edges (4-15⁄32″ and 7-15⁄32″) that lines up with the V-groove in the side. Now fit and glue on the 2-1⁄8″-wide edges to the front of the dresser. To continue the illusion of a lid groove, use a black marker pen to darken the face frame and plywood underneath the gap between the two uppermost edges.
Final Details and Finishing
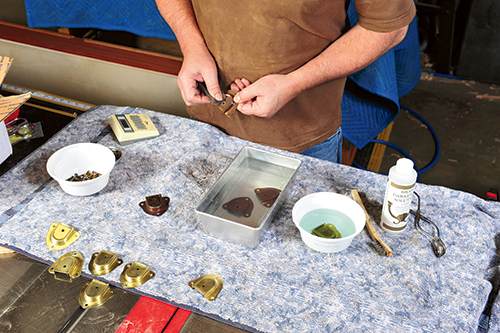
There are a few details to attend to before it’s time to apply a finish to the dresser. First, the trunk lock and draw bolts need to be cut to function with the dresser’s upper drawers. Using a hacksaw fitted with a fine-tooth blade, cut the protruding lobes off the lower edge of the top half of each drawbolt. The hinged hasp that connects the two halves of the trunk lock must also be cut. With the hasp locked in place, cut it in half along where the upper and lower portions of the lock meet, then file the cut edges smooth.
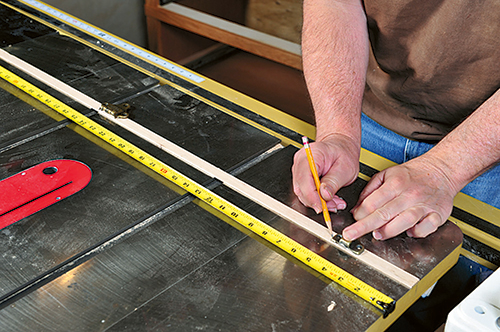
For the trunk’s false lip lid, cut the three 3/4″-wide strips from 1/8″ hardwood stock and sand them smooth. Glue on the two side strips first, locating the lower edge of each strip flush with the upper edge of the V-groove. For the lid strip that attaches to the drawer, you must cut the strip into three separate pieces that fit around the chest’s lock and draw bolts. Lay the upper portions of all three hardware pieces atop the strip, spacing them as shown. Trace around each with a fine pencil, then cut them with a band saw or scroll saw. Fit them into place flush with the lower edge of the top drawer front.
To give the trunk dresser an appropriately “rustic” finish, I finish all outer surfaces with Danish oil. I finish the drawer fronts with the drawers out of the carcass. To prevent the finish from tainting clothes stored in the dresser, I chose not to finish the drawer boxes themselves. After a few days of drying, I waxed all finished surfaces with paste wax, to give the dresser a vintage-looking sheen. It worked nicely.
Mounting the Hardware
Even though I was able to get all the special vintage trunk hardware from one source, I couldn’t get handle caps or mounting screws with the same antique brass finish as the other parts. I ended up treating these parts in a special brass darkening solution I also bought from Shenandoah. To give the caps a more antique look, I lightened up the edges by rubbing with a Scotch-Brite™ pad.
Mount all the hardware, locating the pieces as shown in the Drawings. This final task is easy and satisfying, but time-consuming: It takes more than 150 screws to mount all 27 metal pieces, plus the leather handles! Mount the trunk lock and drawbolts first, aligning all parts with the lip strip on the top drawer face. Tap the corner bumps and slat clamps into place with a rubber mallet until each is fully seated on the slats before setting the screws. Position the cap-style handle loops on the three lower drawer faces, as shown in the Drawing. Slip a leather handle into each pair of loops, then drive a #8, 1-1⁄4″-long screw through the top of each to secure the end of the handle. The open-ended loops mount on the sides of the dresser and capture the tab ends of the large leather handles. Mount the lid lifter handles with 3/4″-long #8 roundhead screws driven through brass washers.
Now you’re ready to put the dresser in place and fill it with clothes!