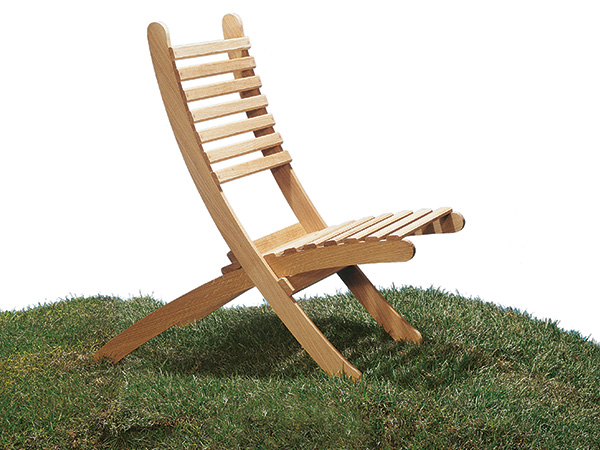
Whether you’re sitting around a warm fire after a day in the boat, cooling your heels at camp after chasing upland game, or just leaning back and soaking up a couple of cold ones after you mow the lawn, it’s nice to have a comfortable place to take a load off. These slide-together outdoor chairs are not a new idea; in fact, the inspiration for this updated white oak version was rolled out years ago in the May/June 1984 issue of Woodworker’s Journal. I did spruce up the design a bit (with some help from my cohorts here at the Journal) by making them more compact when they are nested together for storage. We also added a few strategically placed double-screwed cleats, to eliminate the chance of racking.
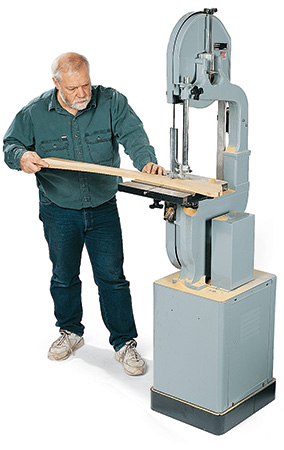
I chose white oak for my material because it’s so durable and because these chairs really don’t eat up a lot of material … there are only about 12 board feet in each one, and I raided my scrap bin for some of that. At a little over $3.00 a board foot, these chairs come in at a very reasonable price. Spanish cedar or cypress would also work well.
Guide to Template Routing
As contributing editor Mike McGlynn once said, “Template routing is a great way to ensure multiple pieces are identically shaped. It’s also a great way to destroy parts; and injure yourself if you are not careful.”
Here are four rules you should always follow:
1. Leave a bare 1/16″ of stock to mill off.
2. Keep your hands well away from the cutter.
3. Attach your template firmly to your stock.
4. Be keenly aware of the bit’s rotation before you begin trimming.
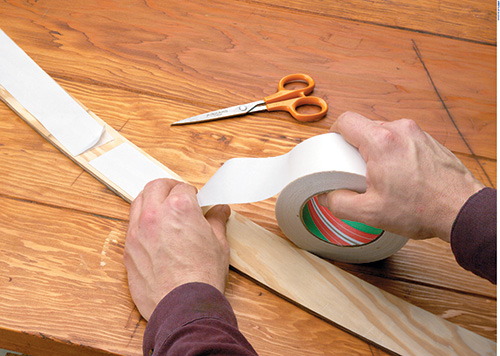
One final caution: Template routing at each end of a piece (across the end grain) must be done slowly and with the utmost care. Rick ruined one of his side pieces before he got the hang of this aspect of the task. We suggest you make a test run on scrap before you move to the real ting.
Deadly Combo: Router Bits and End Grain
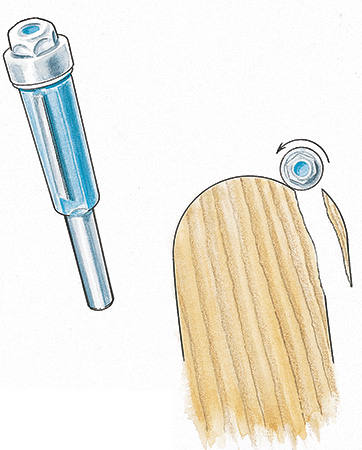
Using a flush-trimming, bearing-guided router bit to cut across end grain can lead to big trouble. Limiting the depth of the cut (thus reducing the penetration of the cutter’s blade) will greatly reduce your chance of splitting the wood.
Getting Started With a Pair of Templates
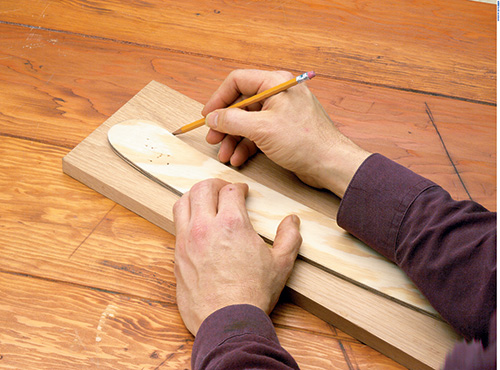
I wanted to make a few of these chairs, and the thought of making all the curved side pieces one at a time was out of the question. Instead, I made a couple of perfectly-sized templates and traced around them to lay out a series of paired seat and backrest sides (pieces 1 and 2) on my hardwood stock. Then I carefully cut these pieces to shape on the band saw, staying just a hair outside of the pencil line. I used double sided carpet tape to attach the templates to the stock for template routing and added three small brads – just for insurance.
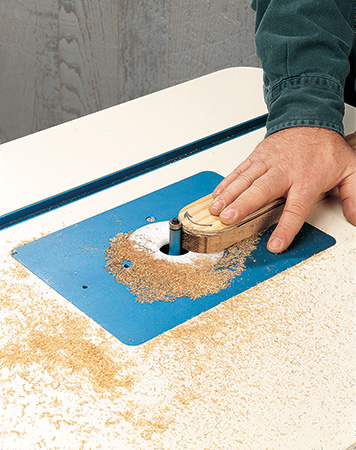
With a 1/2″ flush-trimming bearing guided router bit mounted in my router table, I was ready to rout. The only problem I had with this whole project was when I first attempted to trim a rounded end of a seat side. With my template firmly in place, I started to trim across the grain at the end of the part. In the wink of an eye the bit caught and shattered the stock.
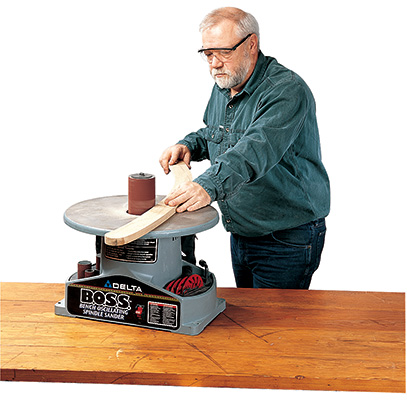
It was like the wood exploded! My second and third attempts (on scrap wood) ended in the same dramatic fashion. After a little more experimenting, I came up with a successful technique for this task. The key is to band saw your stock, particularly at the ends, so that you leave just the barest bit to be trimmed away by the flush trim cutter. Equally important, go slow and hang on tight! If your bit creates a bit of a burn on the ends, don’t worry, it sands off easily. I sanded the edges on a oscillating spindle sander. Go ahead and make all the shaped parts at one time.
Moving on to the Seat and Back Slats
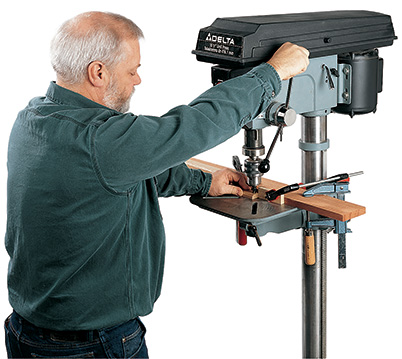
The seat and back slats (pieces 3 and 4) have the same thickness and width, but differ in length. Rip a sufficient quantity of slat stock and then cut them to their appropriate lengths. Again, if like me you are making more than one chair, set up and cut them in groups. (Maybe even make one or two extra in case of a machining error … not that I’ve ever had that sort of problem!) I drilled counterbored holes centered at each end of the slats (one setup works for both types of slats). Later these holes would be plugged to hide the screws.
As long as you are ripping and drilling, go ahead and make the seat and backrest cleats (pieces 5 and 6) from 3/4″ stock. The cleats are wider than the slats and have two screws in each end. They keeps the backrest and seat assemblies from racking, although their main function is locking the chair securely in each of the various seat positions possible with this design. Cut them to size and bore the screw holes. Now grab the slats and cleats and move over to your router table. Chuck a chamfering bit in the router and get busy easing the edges of the combined slats and cleats. (And if you happen to be unlucky and machine the wrong side of one of the slats … don’t worry; remember you made extra … I wish I had.)
Putting it All Together
If you have two drill/drivers, get them ready. First make a 7/8″ x 7/8″ x 20″ spacer. Start attaching the seat and back slats as shown in the Elevation Drawings, and use the spacer to locate each successive slat. Drill a pilot hole with the first drill and then drive it home with the second. When you place the final seat slat, use the spacer again to locate the seat cleat. Make sure you square up the assembly before you drive these screws home. Simple as pie. When you’ve placed the last back slat, you need to go to the Elevation Drawings once more to locate the backrest cleats.
Plug the screw holes (use a water resistant glue), and after the glue has cured, give the chair assemblies a complete sanding. You are almost ready to sit back and make yourself comfortable.
Finish and Upkeep
I thought through a few finishing options for my chairs, but settled on an easily applied outdoor oil finish. I think an exterior grade polyurethane or spar varnish would look great on these white oak beauties … but it would scratch and chip with the use I had in mind for them. I like the oil for many reasons: it is easy to get into nooks and crannies formed by the slats and cleats, it looks great and, most important to me, it is simple to touch up and renew. You will need to reapply the finish on any piece of outdoor furniture, and oil is the easiest way to go, in my opinion. A good cleaning and then a quick rubdown with a coat of oil, and your chairs will be ready for another season of outdoor adventures. Whether that would include a trip to the Boundary Waters Canoe Area or setting them up in your outdoor Brew Area, is entirely up to you.