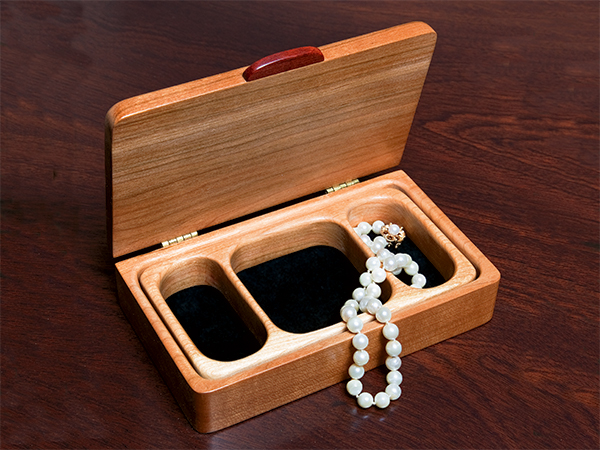
Jewelry boxes are often made with complex joinery to give them an air of sophistication and high style. But you can make a wonderful little heirloom without all the extra work, using just a scroll saw. Scroll saws often sit idle in many shops because we don’t stretch their potential. Here’s a fun way to put yours back into service and prove that it’s more versatile than you might think.
Forming the Box and Insert
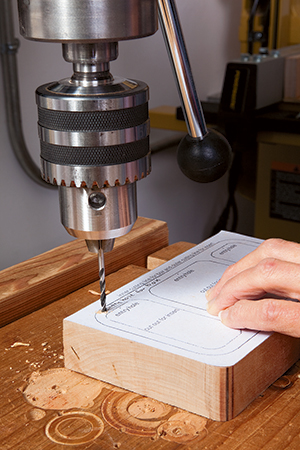
In selecting your wood for the box and the lid, look for a good color match between the two and an attractive grain pattern for the lid. I rough-cut both pieces to size and jointed the long edges that would become the back of the box, using a portable drum sander with a fence. Then make three copies of the pattern. Starting with the box body, I applied clear packing tape to the 1-1⁄8″-thick piece of cherry to help prevent burning when cutting it, then attached a copy of the pattern with temporary-bond adhesive, matching the jointed edge with the back of the pattern. Check your saw table to be sure it’s level before cutting the remaining three sides of the box’s perimeter using a #9 blade.
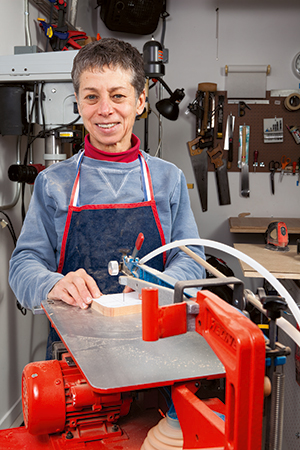
To complete the box body, drill an entry hole just inside the inner cutting line, insert the blade and follow the cut line to remove the center piece. Given the generous size of this waste piece, I set it aside to use for another project. I then sanded the inner and outer faces, using a spindle sander, detail sander and belt sander to remove any burn and blade marks that might be present.
Your next step is to make the insert and compartments, using the 5/8″-thick piece of cherry. I covered the wood with tape and attached a second copy of the pattern. Cut along the outer layout line for the insert first, then drill an entry hole in each compartment, and cut out the center compartments. After you sand the outer and inner faces completely smooth, place the insert into the box body to check the fit. Mark any edge areas that rub the box sides, and sand them down until the insert slides into the box easily.
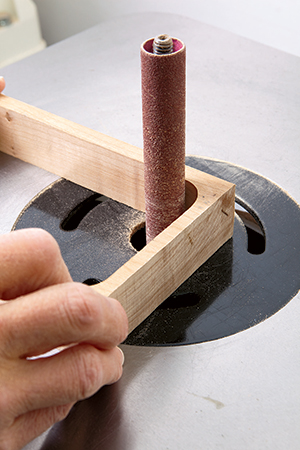
I rounded the top inside edge of the box and all the upper edges of the insert with a piloted roundover bit in my router table. The box interior and insert were given a final sanding, working progressively to 320-grit. But don’t sand the outside of the box at this time; it will receive further sanding after you attach the lid.
Creating the Bottom and Supports
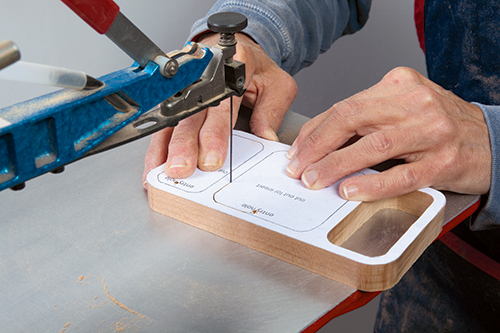
Next comes the plywood bottom. I traced the inner edge of the box body directly onto the piece of 1/8″ plywood to get a cutting line that reflected the sanded dimensions of the box interior. To make it easy to position this piece again after cutting it out, make a few reference marks on the side and the bottom. I cut along the line with a #3 blade and sanded the piece lightly to smooth the edges and adjust the fit. Now use the bottom panel as a pattern for the velvet liner by placing the plywood facedown on the paper side of the velvet and tracing its outline. Trim the velvet to size, and set it and the bottom aside for now.
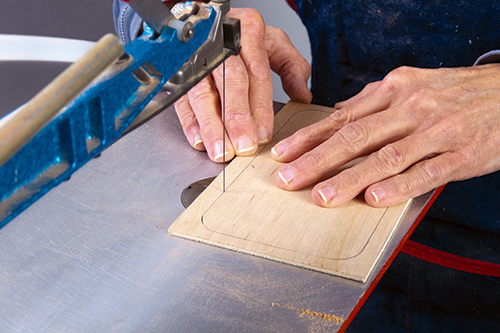
Making the box body from a single piece of wood is faster and easier than using conventional joinery, but it doesn’t allow for cutting the groove that typically holds the bottom in place. I compensated for this by providing support under the bottom, using 3/8″-wide strips of cherry, curved at the ends to conform to the rounded inside corners of the box. To cut these supports to shape, place the strips lengthwise under the box body, lining up their outer edges with the inner edges of the box. This will make it easier to trace the curve of the corners directly onto the strips. I marked the location of the strips, cut along the marked lines, and glued the strips into position so their bottom faces are flush to the box bottom. Small clamps hold them in place as the glue cures.
Once the glue dries on the supports, glue the bottom panel in place.
Adding the Lid

to shape using the box interior as a guide.
To make the lid, attach the third copy of the pattern to a 1/2″-thick piece of cherry, matching the cutting line for the back of the lid with the jointed rear edge. Cut the top out and sand it lightly to remove burn or blade marks. At this point, I compared the profiles of the lid and box, marked any lid overhang, and corrected significant discrepancies by sanding. Final matching will be done once the lid is installed.
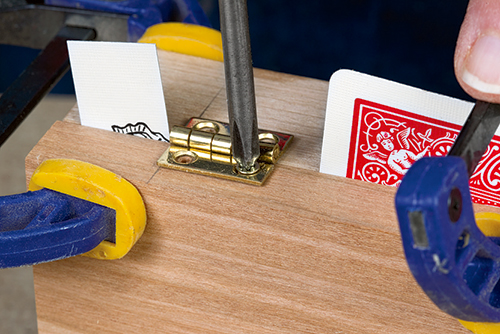
Before attaching the lid, take two precautionary steps. First, since the final thickness of the rear wall will depend on the amount of sanding you’ve done, and since the hinges mount from the back, check to be sure that your hinge screws will not protrude into the box body. If it looks too close for comfort, snip off their tips. Second, I cut two 3/4″-wide strips from a playing card, cutting crossways, and set them aside. These strips, and the remainder of the card, will be inserted between the box and lid on both sides of the hinges, to ensure that the lid will close properly. Once these preliminaries are completed, set the lid in place on the box and so their edges line up. Clamp them together. Draw a line 7/8″ from each side of the box, on both the box and lid, to mark the outward position of each hinge. Then insert the three pieces of playing card between the box and lid, position the hinges, and mark the screw holes with an awl. I put each piece to be drilled into a vise to hold it firmly and wrapped masking tape around the bit to serve as a depth stop. Now stabilize the hinges with a dot of epoxy, and screw them into place to mount the lid.
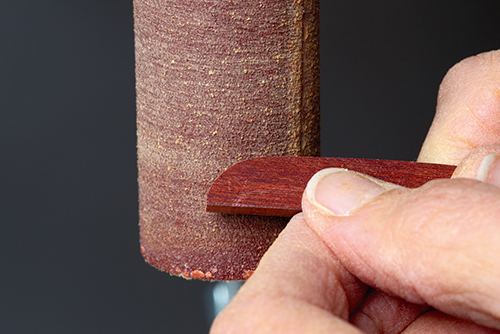
Sand flush any places on your jewelry box where the lid and box don’t line up. I then set my sander table to 45°, sanded a bevel around the front and side edges of the lid top, and rounded the bevel to form a gentle curve. (The bevel serves as a guide for sanding.) Once shaping is complete, give the exterior a final sanding, ending with 320-grit. Cut and sand your lid handle to shape — I used a scrap of bloodwood for mine. Mark the center of the lid, and glue the handle along the lower edge. When the glue dries, unscrew the hinges to prepare for final finishing.
Finishing Up
For my finishing process, I started with a light coat of shellac to seal the surfaces, then rubbed the wood down with 0000 steel wool and tacked it off to remove the dust. Several light coats of clear gloss spray lacquer followed. A final rubout with 0000 steel wool removed any irregularities and left an attractive matte finish.
Now place the velvet, backing still attached, into the box to see if it needs trimming. When you are satisfied with the fit, remove the backing and stick it to the bottom. Place the insert inside, and your project is ready for jewelry.