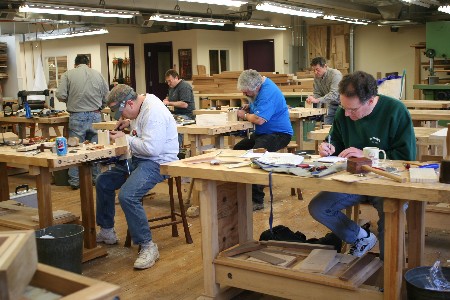
Call Alan Turner in the early hours of the morning, and you are likely to find him hard at work as a lawyer, one of two day jobs that split his time. Come afternoon, though, and he’ll be wearing his other hat: that of the owner of Philadelphia Furniture Workshop, a relatively new and definitely thriving woodworking school in the heart of Philadelphia.
“I have always been a courtroom lawyer,” explained Alan, “but it’s a job that creates conflict, tension and strategy. While that is intellectually challenging, it is very stressful. Woodworking is in complete contrast to that. There is no conflict, but rather extreme concentration, something that causes you to clear your mind of your day job, and of all things non-woodworking.”
Fortunately, Turner has both the chops and the background for both. “I was born in Miami, Oklahoma, and my father was an insurance salesman who was also an excellent amateur cabinetmaker. I grew up with a table saw and can’t remember not having one in the basement. I was ‘take-off’ man on the saw at age seven, and started working on power tools at age 10.”
After graduating from the University of Colorado and Rutgers University law school, he became a public defender in Camden, New Jersey. Later, he was a federal public defender in Philadelphia and a partner in a law firm before going out on his own in 1992. Through it all, he never gave up woodworking. “In 1976, I found myself with a bit under a thousand dollars burning a hole in my pocket and decided to buy a table saw. With that, my woodworking hobby was reborn. By 2002, my family had all the furniture they could tolerate, so I hung out a shingle as a cabinetmaker.
“At the same time, I began teaching an adult education course at night for a local charity in what was formerly a high school woodshop. All the machines had been removed, but there were workbenches, so all I could teach was hand tool usage. That inspired me to learn more about using hand tools, and while I was working on a Newport kneehole desk for myself I took a course to learn carving. Learning hand tools increased the quality of my own woodworking many fold. You can set up a table saw and rip one-hundredth of an inch, but with a hand plane I can do one-thousandth. I can fair a curve with a radius bottom spokeshave faster and better than I can with a spindle sander.
“I had always worked in a basement shop in my home, which was ill-suited for a shop, in part because it floods several times a year. As a result, I was soon looking for shop space, and had a few friends who were also. We got together and bought an industrial building. I took 4,100 square feet of it. By now I had decided I wanted to run a school. I was sure it would be a success because during the years I taught at the night school my courses always had excess enrollment. Besides, having the shop would kill two birds with one stone, allowing me a space to do my own woodworking and have classes.
“As I was opening the school I was introduced to Mario Rodriguez, a noted woodworker, teacher and author, and he agreed to join us in 2006, the year we had our first class. Mario is now a full-time instructor and partner in the school. For now, it is both a school and a commercial woodworking shop, and has two part-time employees. That is because when we first opened the school, we had no guarantee that we would have any enrollment, so I undertook a large millwork job to keep us busy. We will probably never undertake such a large commission again. After about nine months of operation, we got nearly full enrollment for all courses. At this point, the school is busy and doing well, but this does not surprise me. There is, for the most part, no other school like this in the Philadelphia area, and we draw students not only from the city, but from eastern Pennsylvania, Delaware, New Jersey, New York, and even from Virginia and Rhode Island.
“Presently, most of our students are hobby woodworkers. We offer them three types of courses. ‘Foundation skills’ are beginner’s courses covering sharpening, plane craft, milling wood, and both hand tools and machines. ‘Tools and techniques’ focuses on things like veneering, carving, joinery, jigs and fixtures and finishing. The third type consists of project-based courses. In the future, we hope to add a one-year comprehensive course for those who want to pursue a career in furniture making.
“This is a dream shop for me,” Alan admitted, “filled with ‘old iron’ that represents the best of the tool making craft.” Clearly, though, it is the work and, even more, the students who afford him the most pleasure. “We love to see our students’ successes. When you watch the expression on the face of someone putting together his or her first dovetail, it is very rewarding.
“One of the things I like most about woodworking is the incredible honesty of woodworkers. They are straight shooters, and that is because of the nature of their work. Woodworking is not a competitive activity, but is a community based one. When someone does something well, everyone wins.” That, as Alan explained, is one of the things that sets this activity apart from his other day job.
“In law, you can win by sounding credible and being loud, but when it comes to woodworking, it is a different story. After all, you can’t talk a joint into being tight.”