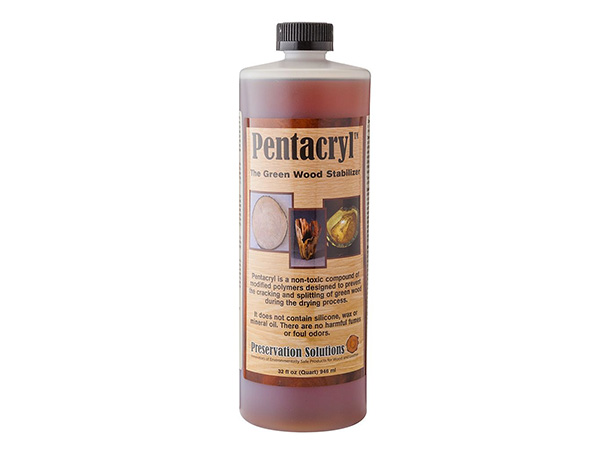
After combing the woods, you’ve found the perfect block or burl for the turning or carving of your dreams. Now, if you can only coax it to dry without cracking.
That is where Dale and Beverly Knobloch come in. They own and run Preservation Solutions, the company that makes Pentacryl, the premier stabilizer for green wood, and the salvation of many of us woodworkers. It’s a material that works so well, it sounds almost too good to be true; but it is.
Pentacryl is an environmentally friendly liquid that penetrates green wood and prevents it from cracking or checking as it dries. It cleans up with either soap and water or mineral spirits, will not discolor the wood, is non-hygroscopic, and will not oxidize, decompose, or migrate when exposed to different degrees of temperature and relative humidity. After it is dry, you can finish over Pentacryl impregnated wood with any type of finish, or glue it with any type of glue.
Dale and Beverly Knobloch started Preservation Solutions about seven years ago, not long after selling a company that made chemicals for the leather tanning industry. Prior to that, Dale went to school to study police science, but instead, went to work as a sculptor, and also worked for his father in the construction business. While doing sculpture for a taxidermy supply company, he developed a one-step chemical for leather tanning, and soon he and Beverly were selling tanning chemicals.
One day, Dale got a call from his friend Bruce Bourque, the head archeologist for the state of Maine. While draining a lake in Newport, Maine, they found six hundred Native American weir stakes; wood pikes set into lakes to act as a weir, or fish corral. They wanted to preserve them, but the only available treatment at the time was with PEG (polyethylene glycol), and that was both too expensive and too time-consuming. Bruce asked Dale to come up with an alternative, and using one of the weir stakes for tests, he developed Pentacryl. Eventually, it was used to treat the vast majority of the stakes.
Soak a chunk of green wood in Pentacryl and the solution will quickly impregnate the entire piece, penetrating at the rate of about one inch per minute in end grain. A typical turning block will usually penetrate overnight, and be ready go on the lathe the next day. Once impregnated, the wood will dry gradually without cracking or checking with a success rate of over 95%. One well-known Canadian turner reports that he has reduced his drying times by two thirds, and has lost less than 1% of the 382 pieces he has turned since he switched to Pentacryl. That’s the sort of odds we like to bet on. Wander the Preservation Solutions’ easy-to-navigate website and in addition to Pentacryl, you will find Wood Juice, for dry or semi-dry wood, and Polycryl, a product designed to fortify spongy or punky wood, such as spalted maple. You can buy directly from the website, but you’ll also find their products at most woodworking specialty stores including Rockler Woodworking and Hardware. My favorite website feature is a nifty online program that lets you calculate how much Pentacryl you will need to stabilize your piece of wood. Pop in the dimensions of a log or slab, identify the type of wood, and in seconds, you’ve got both the volume of wood and the amount of Pentacryl you’ll need to buy.
“Carvers and wood turners are the biggest users,” Dale told me, “followed by green wood furniture makers. They love it, because in addition to preventing cracking, Pentacryl also acts a lubricant, making carving and turning easier. They get much less warping as well, and often none at all.”
How does it work? “While PEG works by plugging up wood cells,” Dale explained to me, “Pentacryl coats the cell walls of green wood to keep them from shrinking or collapsing during drying.” Non-uniform shrinking, with more occurring around the circumference, is what causes cracking. A disk of green wood, for example, is the hardest thing to dry in one piece. Most of the drying is through the end grain, so a cross grain disk will dry faster than a long grain board, and fast drying, at least without treatment, is a recipe for cracking.
Unlike Pentacryl, which is a liquid, PEG 1000 is a solid wax at room temperature. “PEG must be heated during use to make it liquid,” continued Dale, “and can take more than 120 times longer to penetrate wood than does Pentacryl. Even after it dries, PEG is hygroscopic, so it draws in water and gets sticky in warm, humid conditions. Pentacryl works at room temperature, soaks through quickly, and is hydrophobic, so it will not pick up moisture from the air. The result is that it actually keeps the treated wood more stable.”
Once wood is saturated with Pentacryl, it should dry slowly in a cool, damp room. Ideally, that means 60 degrees F and at least 60 percent relative humidity, with the wood propped up so that air gets to all sides. “If you don’t have an appropriate room,” suggests Dale, “get a large cardboard box, like something a washer or dryer might come in, and set it atop the drying wood. That will help keep the moisture in and slow down the drying. You want it to breathe, so don’t wrap it in plastic, but you want the moisture to escape slowly. Expect drying to take about three months per inch of slab thickness.”
Another unexpected bonus is the ability to get accurate feedback during drying. Because it is hydrophobic, you can get accurate readings from a moisture meter during the entire drying process, even though the Pentacryl is still wet.
All in all, I’d say that Pentacryl is certainly doing its part to preserve our woods.