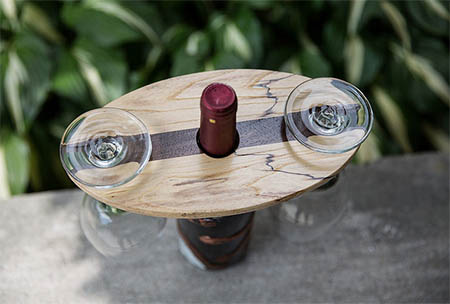
Pat Dolan has been woodworking for over 50 years – although what he builds has changed in that time.
A few years ago, “I was working around the house, building stuff for the kids, giving stuff away, all that kind of stuff,” he said. But, “The reason I’m doing crafty stuff now is my daughters said, ‘I don’t have room for any more presents. I don’t have wall space for picture frames. No more room for tables.’ So they convinced me that I should be making ‘crafty stuff’ and selling through consignment.”
Those three daughters also help him with his Fallen Tree Woodshop business. Caryn acts as photographer; Janel does a lot of the tagging and pricing; and graphic designer Becky does paperwork. Also, “Janel and Becky’ll both go to consignment shops with me to drop product or to craft shows. We’ll do two to three craft shows a year,” Pat said.
Those shows are within his local area of Columbus, Ohio – he gets enough travel in with his full-time job in sales for an Asian food products company. Fallen Tree Woodshop “is a part-time business on the side that I do.”
Prior to about 10 years ago, Pat said, like many woodworkers, “I would buy my lumber, my plywood, my hardwood at the big box store or the lumberyard and go from there.” That changed when one of his brothers called him and said, “‘Hey, I got some birch trees that have to come down before they fall down. Are you interested in the wood?’ I built them a kitchen table out of it and gave it back to them and said, ‘Here you go.’”
Shortly afterward, his brother’s wife was showing off the table to a bunch of friends at a party. Later that night, a storm hit the neighborhood, knocking down a large cherry tree, an oak tree, and two smaller cherry trees. “So I went back up there, harvested all that, and one thing led to another,” Pat said. “That’s how I get my lumber. I have trees that have to come down, or Mother Nature takes them down. And that’s where the name comes from, ‘Fallen Tree.’”
Compared to purchasing hardwood, Pat said, “It’s much less expensive to get rough cut,” although it does have its own quirks. “When you work with rough cut wood, you have to mill it first. It comes wavy and rough and splintery, and I’m on my second planer in 10 years.”
There’s also a storage issue. Although most of Pat’s wood comes from relatives, neighbors, or friends, Pat does have 11 brothers and sisters, plus 30-something nieces and nephews. “I’ve probably got about 5- or 6,000 board feet out in the backyard and under the deck and in the shed,” he said.
His 12’x12’ lumber storage area is protected with a roof and sides that allow for airflow; his 12’x10’ shed contains species like oak, cherry, honey locust and spalted ash. “Then I have another pile about the size of an SUV that has walnut and cherry,” which belonged to a brother in Wheeling, West Virginia, the area where Pat is originally from. He added, “I’ve got a sister that’s got a couple of trees that have to come down this fall, so I won’t have room for anybody else’s wood.”
Pat sometimes takes some wood to have it kiln-dried, “but for the most part, I’ve got so much backed up that I just let it sit out, for actually a couple years now.”
With such a large variety of wood options, Pat said, “I like the variety, but cherry and walnut are really hard to beat. My favorite, I’d have to say, is cherry. It’s just a beautiful wood. And it is easy to work. It’s just hard to get the scratches out of it – the sanding scratches, etc.”
One of his favorite projects, in fact, was a six-foot cherry bar that he built for one of his brothers. “The whole outside was solid cherry: the top and the bar and the rail and the footrail; all that was solid cherry.” He has also made a coffee table and a pair of end tables for one of his daughters from a cherry tree that had mineralized, “so it had black lines going up: where it should have been a little darker red, they were actually black. The bottom 20 feet of this tree – it was about 40 inches across – had that really interesting grain, and those tables came out really cool, because the grain does everything for it.”
Some of Pat’s newest products feature a design that spells out the word “Ohio” in coasters and wall plaques. “Have you ever seen the end grain coasters with a jumble of scrap wood? I do that, but in the middle of it, I’ve got O-H-I-O spelled out. It’s all the way through, so it’s solid wood.”
He’s also licensed by The Ohio State University to make products featuring their block “O” logo. “They’re pretty particular about that kind of thing,” he explained about the licensing process. “You have to pay your royalties upfront and have insurance, all that kind of nifty stuff, and they have to reapprove you every year. Now that I’ve been approved two years in a row, all I have to do is submit online and say, yeah, I want to continue. If there’s any new product, then there’s a whole system you go through. If they think it’ll sell, and they think you’re going to produce a good quality, they will license you.”
With the block “O,” Pat said, “I make a Christmas ornament with it, and I also make a freestanding O just so you can have it all year-round. I’m the only person with that design, and they tell me they won’t allow another person with the design that I use.”
While Pat enjoys woodworking – he started out at age three, following his journeyman carpenter father around “like a puppy” any time tools were in use – “I hate finishing it,” he said. “I have a guy that does finishing work for me. So, last week, I gave him seven sets of coasters and I think it was 25 plaques; he’ll give them back to me probably tomorrow with the finish on them. He works at a cabinet shop; his name’s Jacob Crossan.”
Still, all these years after getting his first drill for Christmas at age 10 (he got the drill bits to go with it eight months later, in August, “so I had nothing to do but spin the drill for eight months”), Pat said of his woodworking, “I like making it.”