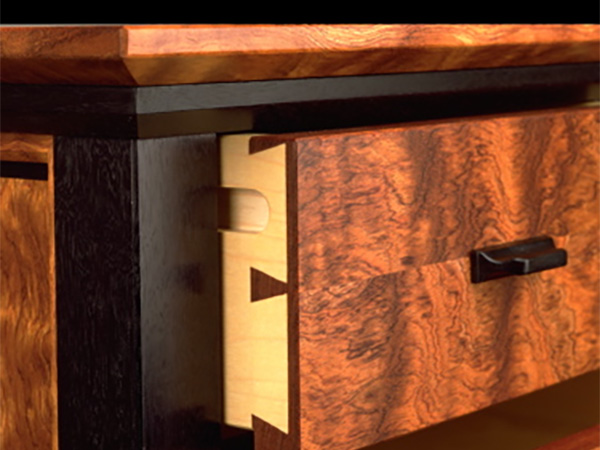
When Michael Waldchen ordered a piece of exotic bubinga a few years back, he wasn’t prepared for what he got. The beautiful, highly figured piece that arrived was 2 inches thick, 48 inches wide and 12 feet long. It took more than four men to carry it. “When I first saw that slab of wood, I bought two more pieces just like it just to have it in my stash. I think that’s the kind of wood that someone like me will only come across once or twice in a lifetime.”
Michael, the owner of Xylem Furniture Studio in Ann Arbor, Michigan, decided to make the most of this opportunity and turned this massive block of wood into veneer, resawing it on his old industrial band saw. He has built a writing desk and matching credenza from this veneer and the desk is still his favorite project.
“The reverence I have for something that old and that huge,” says Michael, “that comes from some other part of the world that I probably won’t even be able to visit ? I was just amazed. I said to myself, ‘this deserves to be treated with a great deal of respect.’ I think the idea of using wood sparingly is a good way to respect those resources and use them wisely.”
Inspired by Queen Anne
Michael also remembers precisely when he decided he wanted to be a professional woodworker and furniture maker. About 20 years ago, he was taking an education course for industrial arts so he could become a shop teacher. One of his fellow students made a Queen Anne gateleg table as his project, and when Michael saw how beautiful it was, he decided that one day he would be able to build a table just like it.
Shop teachers who knew the building trades were in real demand at the time, so he went off to get a couple of years of experience in construction. He liked it so much, he never got around to going back and trying his hand as a teacher. His career steered him toward more cabinet and stair work while he built furniture in his spare time. Then one cold day in January, he quit his job as a carpenter and locked himself in the shop. He told himself, “When I come out of here, I’m going to have enough pieces built that I can put together a portfolio.”
And that’s what he did. He’s now got a thriving furniture making business and iscontemplating his original plan to teach woodworking to others. Now that he knows what he knows about making furniture and running a business, he’s getting more interested in educating others. “I’m becoming more interested in sharing what I’ve learned and the joy I get from woodworking with other people,” says Michael.
– Bob Filipczak