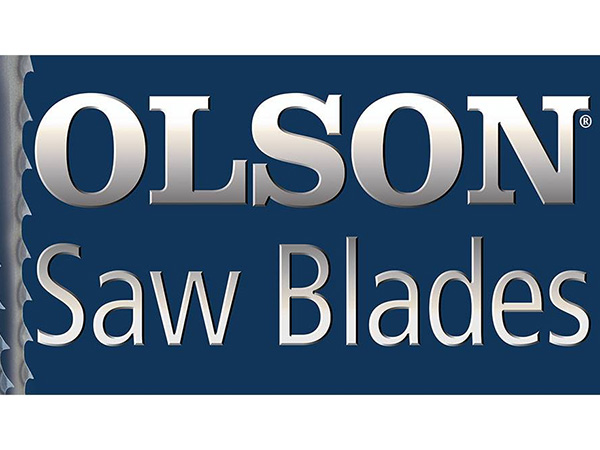
Chuck Olson’s succinct description of the Olson Saw Company‘s business might sound a bit presumptive … until you grasp the depth and range of the company’s ties to the woodworking industry. Olson band and scroll saw blades, plus countless accessories and saw frames, are used in virtually all domestic and imported scroll/jig saws. That includes saws sold by Delta, DeWalt, Dremel, Skil, Rockwell, Pro-Tech, Powermatic, RB Industries, Hegner, Sakura, Shopsmith, Excalibur, Rexon, Ryobi, Sears Craftsman, and Makita!
In fact, according to Chuck, the company has no domestic manufacturing competition for scroll saw blades. You may not realize you’re using an Olson saw blade, since a majority of their business is in OEM or private labeling for other companies. The other percentage is produced, packaged, sold, and marketed under the Olson name through stores such as Rockler, Klingspor’s Woodworking Shop, and ACE and True Value hardware stores.
And Chuck Olson, the company’s director of sales and marketing, ought to know about Olson blades. His grandfather and four great uncles started the company in Brooklyn, NY, back in 1918. In time, his grandfather became sole owner and eventually his offspring — Chuck’s father, aunt and uncle — went into the business. By that time, the company was a going concern, making blades for many different industries, creating innovations, and discovering how quickly the business can change. Chuck recalled a bit of company history to illustrate.
“After World War II ended, we made a six-in-one handsaw,” he explained, “It had one wooden handle with six good blades that could be interchanged. It originally sold for approximately $3.95. But we soon found we couldn’t compete with the Japanese who were exporting a similar product for about a dollar. We couldn’t buy the steel for that price and ended up getting out of the business.”
That was only the beginning of overseas competition.
“Another of our claims to innovation fame came in the 60s,” Chuck noted. “We had a customer who used our blades to cut out wooden puzzles. They were 1/8″ thick and they’d stack 10 of them up and use a 24″ Delta or Powermatic scroll saw to cut the design out. But because scroll saws cut in only one downward direction, the bottom piece was always splintered and had to be thrown away. So we came up with a design that had opposing teeth … pointing up at the bottom of the blade that fit into their existing saws and effectively eliminated the tearout on the bottom piece. We saved them 11 percent that was being wasted and sold them about 5,000 blades a week! We were the first to produce a reverse-teeth saw blade that everyone copies today.”
Jump ahead to 1976 and one of the Olson’s customers is the Cutall Company, a division of Blackstone Industries. When Blackstone became interested in acquiring Olson, the three sibling owners were nearing retirement age and took them up on the offer. About the same time the company moved from Brooklyn to its present location in the quiet residential town of Bethel, Connecticut. And today it employs about 100 people in Bethel and takes its responsibility to the community very seriously.
“For every person working for Olson,” Chuck noted, “we’re supporting four family members in the community.”
Unlike so many U.S. tool manufacturers, most Olson products are still made in Connecticut … with a few products also being made in Germany. And through its Blackstone parent, Olson shares the woodworking market with Zona Hobby Tools and Foredom Electric Company. Zona offers an extensive line of hand tools used for modeling, hobbies, arts and crafts and woodworking. Foredom, a well-known name among serious woodcarvers, makes flexible shaft power for hand grinding, deburring, sanding, cleaning, carving, buffing and polishing all types of materials. The brands not only complement each other, but according to Chuck, they offer lots of opportunities for crossover sales.
Even though his company has kept manufacturing in the US, all the tools that are now made offshore concerns Chuck.
“Traditionally, manufacturing was the only industry where anyone could come on board a company with little or no skills and work his way up the organization. When all those jobs go overseas, what will we have left here?” he asks.
At Olson, though, the shift in manufacturing has not been all one way.
“Coping saw blades, like a lot of OEM, had gone to off-shore manufacturers,” Chuck recalled, “Then about 15 years ago, we became more competitive by modernizing our own equipment, increasing productivity and making it easier to buy from us to recapture that business. Now we make millions of them. Sometimes I wonder who could be using all those blades every year!”
As for the scroll saw blade business, the company continues to take an innovative approach to staying competitive. About eight years ago they came out with a precision ground tooth scroll saw, the first of its kind in the Western hemisphere. They developed and designed an in-house, grinding process called PGTĀ® (Precision Ground Tooth). The blades were immediately copied by overseas competitors, but using an older, less costly milling process. The company continues to offer the PGT version, but made a decision to copy the copies and came out with their own milled and less expensive version … effectively beating the competition!
Even more recently, the company came out with an upscale All-Pro” brand of band saw blades.
“It has a super hard edge, and its increased tool steel content allows us to increase tooth hardness. Plus it has a tempered back that adds precision and accuracy to the woodcutting process,” Chuck said. “When it’s been demonstrated at the Woodworkers Choice booth at the Woodworking Shows, we’ve had great success getting people to switch from a $9 hobby blade to our premium blade … even with a $14 to $16 price. We’ve never had a negative comment about the blade.”
With that kind of commitment to quality, customers, and employees, you may spend more for an Olson blade … but it’s going to be worth it!