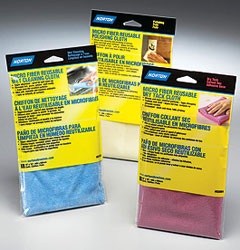
Look about your shop and, odds are, you will see the name Norton, and no wonder. A division of Saint-Gobain, they are the world’s largest abrasives company, offering loose grinding media, diamond abrasives, grinding and sharpening wheels, bench and slip stones, Bear-Tex nylon abrasive pads, and a huge range of sandpaper and sanding sponges. If it’s abrasive, Norton is probably involved, but oddly enough, the company did not start out that way.
Their story begins back in the 1830s, well before the Civil War, when Frank B. Norton started a stoneware crockery company. In those days, food was stored in fired clay crockery, so that was a good business to be in. However, customs change and, around the time of the Industrial Revolution, new technology resulted in the emerging popularity of tin cans for food storage. Soon, the need for crocks diminished.
During the same period, the development of a process for bonding aluminum oxide grit with fired vitreous ceramics gave rise to abrasive wheels, a necessity in metal grinding operations. As the need for one product waxed, the other waned, so Norton started making grinding wheels. Frank Norton, however, wanted to stick to crockery, so one of his employees, John Jepson, bought the fledgling grinding wheel division from Frank. The new company shared the Norton name, but soon, the pottery division folded, a victim of changing times, and all that remained was the Norton Grinding Company.
Meanwhile, in a small village in New Hampshire, a farmer was discovering that the mica schist stones in his pasture were ideal for sharpening farm implements and axes. In 1823, he founded the Pike Company, the first commercial supplier of natural sharpening stones in North America, and eventually expanded beyond the local offerings to include over 29 varieties of natural stone, including the famed Arkansas stones, mined from novaculite found only in that state.
Norton was not resting on their laurels, either. In about 1897, they pioneered the first synthesized sharpening stones in the world. They were made of either aluminum oxide, called India” stones, or silicone carbide, called Crystalon”, and were molded and fired with a vitreous bond similar to the technology used in wheels. Today’s stones are not substantially different from the ones made in those days. Although Norton has made synthetic oil stones since the turn of the century, they did not get involved in water stones until 1993.
For many years, starting around 1897, Pike and Norton enjoyed a very copacetic business relationship distributing each others’ products. In 1932, after a long and happy alliance, Norton bought Pike, making it a division of the company. As it turns out, Norton was quite good at acquiring other businesses. Over the course of the first 50 years of the last century, they picked up a coated abrasives division (Behr-Manning Company of Troy, NY) that made sandpaper and several smaller acquisitions in addition to Pike.
They also expanded operations not just in the U.S., but worldwide, becoming multinational very early in the 1900s, something unusual for that time. During the first decade of the 20th century, Norton established plants in Germany and England, and later expanded to the point they are today, with plants all over the world. Finally, in 1991, they were in turn bought by Saint-Gobain, a French company that deals in engineered materials ceramics, glass, building materials, abrasives, fiberglass and so on.
Part of the reason for Norton’s success is that innovation and quality control have long been hallmarks of their operations. Their recently introduced 3X line of sandpaper, for example, is a self-lubricated aluminum oxide medium that cuts much faster, doesn’t load, and has a backing that doesn’t crack when you fold it. Most important, according to the company, is that it lasts three times longer than other brands. They feel there is nothing else like it on the market. One way they maintain their quality is that, unlike many of their competitors who outsource most production, Norton continues to manufacture virtually everything they sell.
To get more insight into their products, and to find out the answers to a few questions that woodworkers seem loathe to agree on, I spoke with David Long, the North American Sales Manager for DIY/Contractor Sales. After 29 years with the company, he had a lot of good advice to share.
“When you get a new bench grinder for sharpening your chisels,” David suggested to me, “the first thing you should do is throw away the wheel that came with it. That gray grinding wheel is for stock removal of soft steel, not for sharpening tool steel. Replace it with a white or pink wheel, such as Norton’s 38A, a designation which indicates a certain type of aluminum oxide specifically designed to cut tool steel.”
Better yet, David said, would be to consider their new Premium 3X Blue Wheels, made with Norton’s patented SG grain, a ceramic alumina grit. They’re designed to last longer, cut quicker, and resist burning your tools, making it a real triple threat. “For turning tools,” David suggested, ” use a 40-or 60-grit wheel to rough and shape, and finish with 80- or 100-grit. With bench chisels, use a 60-grit wheel, then go directly to your bench stones.”
When I asked about the difference between oil and water stones, David explained that, while the grit in the two types of stones may be the same, oil stones have a higher binder to grit ratio (more bonding material) than water stones, making them a harder stone. “Oil is a much better lubricant than water, so you can use it with a harder stone. If you are going to use water as the lubricant, you need a softer stone. You could theoretically use water on a harder oil stone, but it would tend to glaze over quickly. Conversely, you could use oil on a water stone, but it would defeat the purpose of it. Water stones are designed to cut quickly, and need a lot of lubricant. That works with stones constantly flooded with a water bath, but is impractical with even thin oils.” The wrong lubricant won’t harm the stone itself, but it will make your job harder.
These days, most woodworkers use the faster cutting water stones, though some still swear by natural Arkansas stones. Listed from least desirable to most desirable, the natural stones include Washita, soft white Arkansas, hard white Arkansas, hard black Arkansas, and hard translucent, which comes in black, white, and pink. Norton sells only the premium translucent stones, which they feel give the best finish. “In theory, you could make a synthetic oil stone equivalent to translucent,” Long explained, “but because they already exist in nature, no one does it.” They do make water stones in such fine grits, though. “An 8,000-grit water stone will give you as good or better a finish as a hard translucent Arkansas, and is faster cutting to boot.”
Another new product that caught my eye was their Micro-Fiber cloth, a replacement for tack cloths. Standard tack cloths can leave a sticky residue that creates problems for some finishes and will leave a static charge on the surface that quickly draws more dust from the air. These new Micro Fiber tack cloths won’t leave any residue and don’t leave a static charge either. They pick up even the smallest bits of dust and hold it until you wash the cloth, which is reusable up to 500 times.
David pointed out that bringing more helpful products to the small user was one of the things Norton takes great pains to do. “We try to transfer the technology we develop for industrial woodworkers, who are looking for measurably higher productivity, to hobby woodworkers, small shops, and custom woodworkers.”
Perhaps that is why so many of us woodworkers see the name Norton whenever we flip on the lights in our shops.