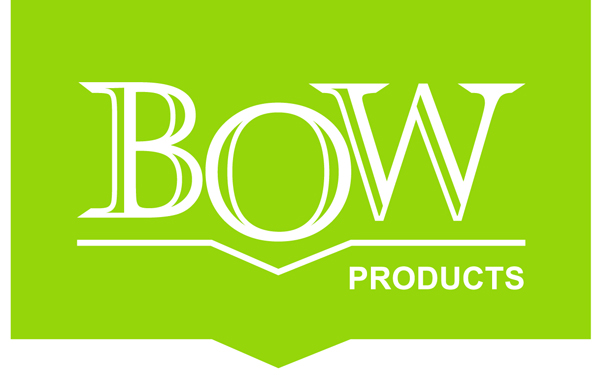
Anyone who’s been properly trained on table saw use knows the importance of featherboards. They press workpieces against the fence during rip cuts to help prevent kickbacks. And, you can position them much closer to the blade than your fingers dare go to provide that extra guiding pressure. It ensures that cuts stay on track and accurate.
But typical plastic or wood featherboards aren’t without their quirks. The hard plastic or wooden “spring” fingers can actually make workpieces difficult to feed through if the device is clamped too close to the fence. A featherboard can mar soft wood when the tension is too great. And, if it happens to come in contact with a blade or router bit, plastic versions can shatter with surprising violence. They might even damage carbide cutting edges.
So, we certainly need featherboards, but a truly better design seems in order. Yet, aside from a color change or possibly a new mounting option, when’s the last time you can recall seeing real innovation in featherboard engineering? It’s been a long while.
Sometimes, a brush with catastrophe provides the inspiration to go back to the drawing board — and that’s exactly how Keith Bow was shocked into awareness about featherboard safety two years ago. A near kickback situation at his table saw made him realize that conventional featherboards aren’t all they’re cracked up to be.
“When I started examining the performance of standard featherboards, I realized that the amount of resistance force when backward pressure is applied was only marginally better than the force required to push the board forward during infeed,” Keith says. “Translated to me, this meant that featherboards just aren’t designed with kickback in mind.”
Keith and his brother Ron operate Bow Products, a company that focuses on material handling solutions for forklifts. While Keith admits he’s just a “tinkerer” woodworker, his 9-to-5 expertise in material handling has given him working knowledge of a cushioning material called EVA. It’s a hardened foam that can support tons of load, yet provides a forklift platform that is soft and dampens vibration.
EVA is also a material common to shoe manufacturing, which, at one point, was Ron’s career.
When the two brothers began testing featherboard physics, they learned that the feathers must grab the wood as it moves backward in a kickback situation and yet be pliable enough to absorb the energy of the impact. Hardened plastic or wood won’t do this, but EVA seemed to be a perfect solution: it’s strong, pliable and yet easy to form. After several prototype trials, the Bows invented a “living hinge” type feather style from EVA that looks similar to a water wave pattern. The soft foam minimizes friction when wood is fed into a cut. But, if the wood should reverse course, the feathers hinge backward and become longer as they reach a perpendicular orientation to the fence. At that point, they bottom out into a stop, which pinches the wood against the fence. Then, the dense composition of the hardened foam absorbs the backward energy. A side benefit, too: EVA doesn’t damage cutters if a bit or blade slices into it.
“We realized then that our FeatherPRO EVA concept was legitimate and revolutionary,” Keith recalls.
Another innovation the Bows are ushering in with FeatherPRO’s design is the ability to replace the foam feathers if they should become damaged. While the body of FeatherPRO is hard plastic, the feathers fit into it “puzzle piece” style. They’re easy to push out of the plastic body in one piece and without tools.
The Bows are offering feather inserts in two densities. The “standard” model feather accommodates all pressure needs, Keith says. It’s colored dark gray. A light gray “ultralight” feather version is also available. “It’s a slightly softer material composition … that gives the operator a more sensitive feel over applied pressure. It’s better suited for soft woods or delicate cuts,” Keith says.
For many inventions, obtaining a patent involves extensive research and entering into a complex legal process. But that aspect of bringing FeatherPRO to market has been quite manageable, Keith admits. He says it’s because both the hinge design and feather material are novel in this application.
“It’s been more difficult to be precise in the claims of related applications,” Keith says. “You’ve got to study and understand what patents are out there and make sure you are unique in your solution, versus existing patents.”
And, you need to hire a good attorney, he adds.
Currently, FeatherPRO featherboards are available at FeatherPro.com and through some woodworking product dealers. The Bows plan to add more dealers as soon as they expand their woodworking product line further. And that goal is close to being realized: Bow Products will soon release a Double Stack FeatherPRO. It’s in the packaging stages of development now. Keith reveals that a push stick is also in the works. And, while FeatherPRO now has a pair of metal bars that tighten into 3/8- x 3/4-in. standard miter slots, a T-slot mounting system is coming, too.
The Bows are proud to be manufacturing FeatherPRO entirely from their Corfu, New York, facility, which Keith says allows them complete control over production and quality. But that’s not the most gratifying part of bringing a revolutionary new woodworking featherboard to market. Safety is.
“I think about it all the time: Was someone spared injury because of our product? That’s very satisfying. Beyond that, it’s coming up with a really important design that not only improves safety but also offers so many more benefits that traditional featherboards can’t.”
Learn more about FeatherPRO featherboards by clicking here.