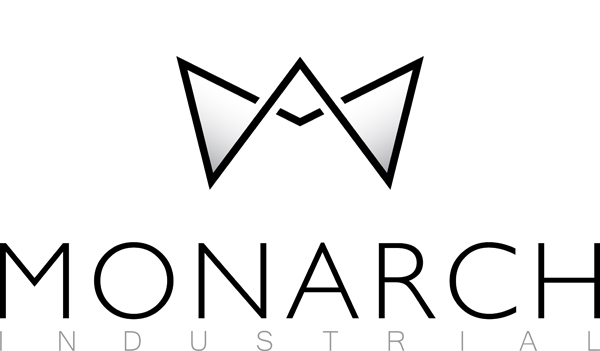
What’s your biggest frustration with using a band saw? For many woodworkers, it’s setting blade tension correctly. Too much tension risks breaking expensive blades. Too little tension, and blades can slip out of position on the wheels or cut poorly and wander — especially when resawing. To make matters even more challenging, we use a range of blade widths that each require a different level of tension. But the built-in tensioning gauges on many band saws provide only a “best guess” approximation of tension, and commercial tensioning gauges can be prohibitively expensive.
This was the design challenge Barry Schwaiger took to task two years ago when he launched his new company, Monarch Industrial, Inc. Schwaiger, a lifelong woodworker, also used to work for one of the leading tool manufacturers, so he’s is no stranger to the engineering conundrums that woodworking machinery presents.
“I became a ‘golfer getting to work in a golf club factory’ when I went to work for Powermatic in the late 90s. I spent 15 years doing product development on the cast-iron stuff,” Schwaiger recalls.
Three years ago, he left Powermatic to pursue several independent businesses — one, selling indigenous hardwoods and flooring to woodworkers in central Tennessee, where he lives, and the other to start up Monarch Industrial, his new tooling and manufacturing venture.
Schwaiger says that while Monarch will be serving some industrial customers, the second prong of his business model will be to develop truly innovative products for hobbyist and professional woodworkers. It seems the “golfer” in Schwaiger now owns the golf club company. And the drivers or putters he intends to make will be like no others on the market.
“Since Monarch is family-owned, with no external investors or boards of directors to answer to, we have the autonomy to chase practical solutions versus commerce objectives. If a product doesn’t first satisfy our own discerning eye as well as a host of other confidants in the woodworking world, then we simply will not pursue that idea,” Schwaiger explains.
And so it is with the new Monarch Gauge for tensioning band saw blades. It functions differently from the two common options we have for setting blade tension, which break down into either the integrated system within the band saw itself or aftermarket accessories.
“Integrated gauges, which typically work off the compression of the upper wheel spring, are just inherently clunky,” Schwaiger says. “They are indirectly indicating the tension of a blade and have introduced several variables, such as the upper wheel spring, the wheel itself, tires, tension slide mechanism, etc. All of these things just get you further away from the true measurement you are trying to get, which is: ‘What is going on with the actual blade?’”
Aftermarket tensioning gauges, on the other hand, focus primarily on how much a blade stretches under tension, which is a miniscule amount. It takes a sensitive and expensive instrument to measure this tension accurately. Most of these are based on dial indicators, which are better suited for machinists than hobbyist woodworkers.
“Most often a woodworker will find a more pressing need in the shop before they will purchase one of those instruments,” Schwaiger adds.
The inspiration for the Monarch Gauge is based on one of the methods many woodworkers use to “test” their level of blade tension, and maybe you do it this way too: pressing on the side of the blade to see how much it deflects from flat. The other method some of us use is to pluck the blade and evaluate tension based on the audible ring.
“Both of these techniques are certainly a subjective approach to something that can be standardized,” Schwaiger says. “Simply putting some repeatable mechanics to the ‘thumb’ test was the motivation (for the Monarch Gauge) in its simplest form.”
Here’s how the gauge works: Two stainless-steel plates pivot past one another and are connected by a tensioning spring. One plate has a pointer indicator, and the other has a numeric scale. The gauge clips to the blade with three pins — two straddle it on one side, and the third presses against it on the other side, under spring tension.
“The center pin is connected to an arm that exaggerates its movement to a scale that can be read for an indication of the ‘Monarch number.’”
Schwaiger says the numbers on the scale are arbitrary and do not correlate to a particular unit of measure. It’s intended to be a new frame of reference for setting blade tension and eliminates other complicated metrics related to PSI, pounds of force of a spring, small fractions of blade strain and so forth. Instead, the goal here is for a user to start with a blade tension that works well for them and then use the Monarch Gauge to check what that tension preference is — its Monarch number.
“Over the years, we have found that there is a broad range in what experienced users recommend for tension. Some are advocates for lower tension and others, higher tensions. In order to stay neutral on that front, we suggest to a user to find what works well for them in a particular application and then make a quick measurement and write the Monarch number on their blade box or inside door of their band saw,” Schwaiger says.
The jig’s instruction manual comes with a chart and suggestions for blade tensions over a continuum of blade sizes, for those users who do not have a “sweet spot” of blade tension already. It can serve as a starting point for finding the optimal Monarch number.
The Monarch Gauge sells for $79.99 in one version that will work for a full range of blade widths and compositions, from 1/8 in. up to 1 in. wide. The only caveat is that a saw must have a resaw capacity (vertical distance between the table and the upper blade guides raised to the highest level) of at least 5 in., in order for the Gauge to clip to the blade properly. Schwaiger adds that the gauge has even been tested on large portable sawmills and horizontal metalworking saws. “In each example we have found, the gauge reports a Monarch number that can be referenced and repeated in the future,” he adds.
Schwaiger hopes that the benefits of predictable blade performance, along with the possibility of longer blade life, will make the new Monarch Gauge a welcomed — and affordable — addition to any woodworking shop.
And aside from bringing a practical woodworking accessory to market, Schwaiger is also pleased to announce that it is an American-made product.
“I spent quite a few years in the corporate world engaged in transferring U.S.-made products to the Far East. While the economics of the time dictated such a shift, it never really felt quite right. Now that I have the ability to direct Monarch’s vision, I want to spend the second half of my career doing the opposite. There is such capability here in the States, and it feels so satisfying to call up a U.S. supplier with an order and support American families. That makes it all worth it.”
Learn more about Monarch Industrial, Inc., and the new Monarch Gauge by clicking here.