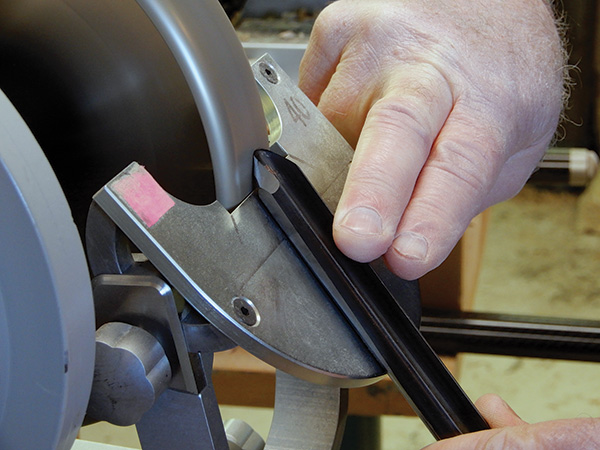
This article, “Modern Tool Steels and Grinders,” is from the pages of American Woodturner and is brought to you by the American Association of Woodturners (AAW) in partnership with Woodworker’s Journal.
There have been many changes in both the steels used in woodturning tools and in the grinding wheels we use to sharpen them. These changes have created confusion among woodturners. We wonder why we sometimes don’t get the results we expect from expensive new tools. Following is a summary of how tool steels have changed and what it means for woodturners.
Evolving Tool Steels
For many years, M2 has been the most widely used and successful conventional high-speed steel (HSS) used for woodturning tools. M2 revolutionized woodturning by providing tools that were much more resistant to both wear and heat than previous tools. More recently, we have seen growth in the popularity of M42, another conventional HSS. We have also seen the introduction of particle-metal tools (also called powder-metal tools). Tools with steels such as M4 and A11 (Crucible Industries’ version of which is called CPM 10V) have become widely available and are gaining in popularity.
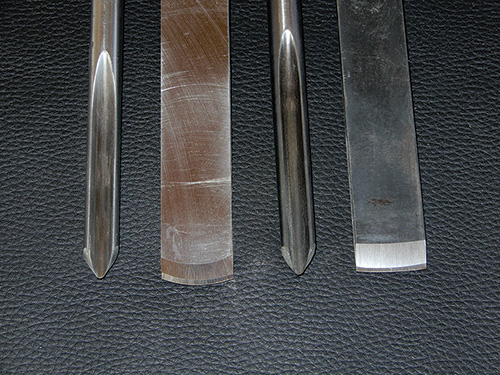
What are the differences between conventional high-speed steels such as M2 and M42, and particle metals such as M4 and CPM 10V (A11)? Which are the better choices? It helps to understand how they are made.
In manufacturing conventional HSS, iron and carbon are melted in a furnace, and alloys are added to the molten steel. The molten steel is then poured into molds and allowed to cool. The alloys make the steel more resistant to abrasion (wear) and to damage by excessive heat, as well as tougher and more resistant to breakage. Since alloys in steel make it better, logically we would like to add more. But there is a limit to the percentage of alloys we can add to conventional HSS. As the steel cools, atoms of some of the alloys chemically bond with atoms of carbon, forming what are called carbides. Carbides contribute positively to abrasion resistance, heat resistance, and toughness and are much harder than the surrounding steel. But the higher the percentage of carbide-producing alloys, the larger the carbides become. Excessively large carbides create two problems: they are too hard to be ground (sharpened) with most conventional grinding wheels and they rob the surrounding steel of their benefits.
What we’d like is steel with very small, very hard, abrasion-resistant carbides that are abundant and well-distributed. The carbides of vanadium are particularly hard and contribute very positively to abrasion resistance. That’s why steels high in vanadium stay sharp longer. The carbides of molybdenum contribute to wear-resistance, and molybdenum contributes to toughness. Carbides of chromium and tungsten contribute positively, too. How can we add all the alloy we would like and at the same time avoid excessively large carbides? Enter particle-metal technology.
In the manufacture of particle metals, iron and carbon are melted in a furnace, and the alloys are added. But instead of pouring the molten steel into molds and allowing excessively large carbides to form as the molten steel cools, the molten steel is blown through a nozzle, creating microscopic droplets of steel. The droplets are on the order of 6 to 10 microns in diameter, and the carbides within the droplets are 2 to 3 microns in size. One micron is one-millionth of a meter. The steel powder is then put into a metal canister and subjected to extremely high pressure, at forging temperatures, in a process called hot isostatic pressing (HIP), transforming the powder into solid steel. The particles bond together so thoroughly that the resulting steel is very dense, with almost no porosity. We now have solid particle metal with very small, very hard, well-distributed carbides. Particle metals have revolutionized woodturning tools.
A Closer Look

The above chart shows the chemical composition of M2 and M42 conventional HSSs, as defined by the American Iron and Steel Institute (AISI). M2 contains vanadium, molybdenum, tungsten, and chromium, all of which contribute to the formation of carbides, making M2 quite abrasion-resistant and tough. M42 also contains molybdenum and chromium, and smaller percentages of vanadium and tungsten. To compensate for its lower percentage of vanadium, whose carbides are very abrasion-resistant, M42 has 8% cobalt, which contributes to hardness. What M42 lacks in vanadium carbides, it compensates for with greater hardness. M2 is very widely used in woodturning tools. M42 is less widely used, but its popularity is growing.

This chart shows the chemical composition of M4 and CPM 10V (AISI A11) particle metals. M4 is an excellent particle metal but has been adopted by a relatively small number of tool manufacturers. CPM 10V (AISI A11) has been adopted by more tool manufacturers, and its market acceptance is growing. There are other particle metals, but for purposes of brevity, we will limit our discussion to these two excellent examples.
Grinding Wheels
While particle metals perform exceptionally well, the carbides within them have created new challenges. Most conventional grinding wheels are unable to sharpen particle-metal tools to a keen edge. That’s why conventional wisdom says we cannot get particle- metal tools as sharp as HSS tools. But that’s no longer true—enter cubic boron nitride (CBN) grinding wheels.
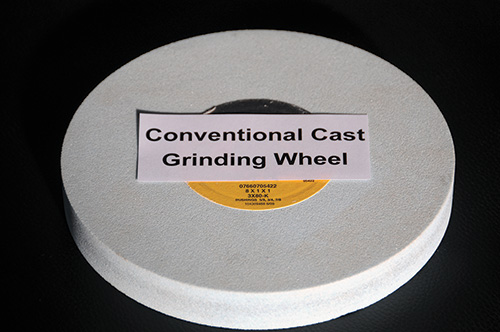
CBN abrasive is almost as hard as natural diamond and is highly resistant to abrasion; it maintains its sharp edges so it cuts quickly and efficiently. The CBN abrasive is typically bonded to the surface of a steel or aluminum grinding wheel, so the abrasive sits proud of the wheel. When grinding with a CBN wheel, just the abrasive touches the tool, cutting faster and cooler. The abrasive in a conventional, vitrified cast wheel, on the other hand, is mixed in with a bonding matrix (called the bond) that holds the wheel together. Since both the bond and the abrasive rub on the tool as it is being ground, conventional wheels don’t cut as quickly, and they get the tool hotter than do CBN wheels.
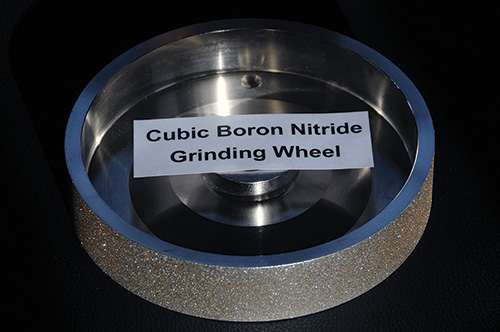
Since the abrasive in most conventional wheels isn’t hard or sharp enough to cut through the carbides, it either shatters the carbides or knocks. them out of the cutting edge, leaving a microscopically ragged cutting edge. It simply isn’t possible to get a particle-metal tool as sharp with most conventional wheels as it is with CBN. And CBN wheels work wonderfully on M2 and M42 as well as on particle-metal tools, getting both steels much sharper.
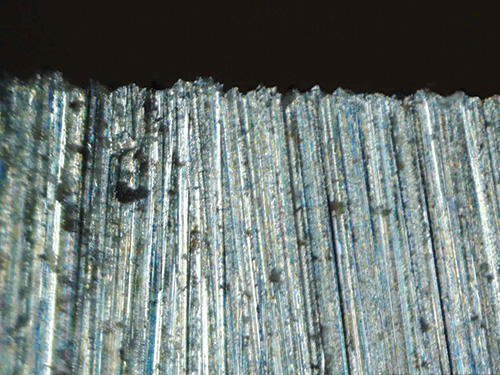
CBN wheels have three other great advantages. First, they are much better balanced than conventional wheels, so they run more smoothly. Even though conventional wheels can be balanced, as soon as they are dressed, the balance changes. It is almost impossible to keep conventional wheels balanced, and the vibration makes it more difficult to grind accurately. Smooth-running CBN wheels facilitate better grinds. Second, CBN wheels never need to be dressed, so their diameter never changes. For those who use jigs when grinding, the cutting angles on tools change every time a conventional wheel is dressed because the diameter of the wheel is reduced. Unless the jig is readjusted frequently, cutting angles are changing. With conventional wheels, your jig’s grinds may not be nearly as repeatable and consistent as you think. With CBN wheels, the angles don’t change. Third, CBN wheels produce far less dust than conventional wheels. Breathing the dust produced by dressing conventional wheels and by grinding tools on them can be a health hazard.
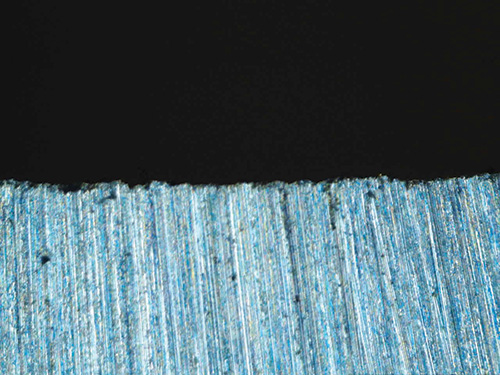
One other difference with CBN wheels is that they are readily available in much finer grits than conventional wheels, including 80, 180, 350, 600, and 1000 grits. When a tool is ground on an 80-grit conventional wheel, the scratch pattern on the bevel produced by the abrasive in the wheel creates a series of “teeth” along the cutting edge of the tool. These teeth are clearly visible under a microscope. If the same tool is ground on a 600-grit CBN wheel, the teeth are sharper and more uniform, and there are many more teeth across the cutting edge. The tips of the teeth do the cutting and therefore wear down as the tool cuts wood and gradually becomes dull. With many more teeth across the cutting edge, the tool sharpened on a very fine CBN wheel will not only be sharper, it will dull more slowly. That gives a fine-grit CBN wheel a big advantage over an 80-grit conventional wheel.
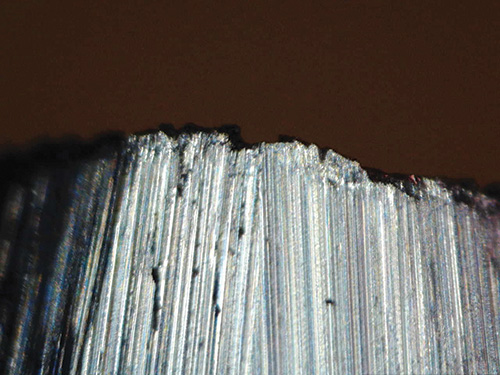
Now consider that with particle-metal tools, each tooth has hundreds of carbides within it that are finer, harder, and more evenly distributed. Conventional HSS tools also have many carbides within each tooth, but the carbides are larger and not as well distributed within the metal. Therefore, even though there is an advantage in grinding both conventional and particle-metal tools on fine grit CBN wheels, the particle-metal tool is the winner.
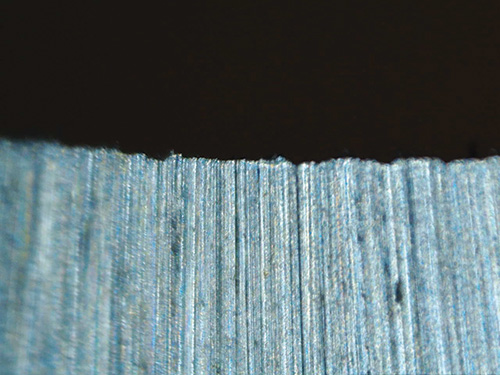
What grits do I use in my workshop? I have two 8″ (200mm), 1725- rpm grinders with two CBN wheels on each: an 80- and 180-grit on one grinder, and a 350- and 600-grit on the other. I use the 80-grit for rough-shaping tools. It cuts fast and cool. I use the 180-grit primarily for general sharpening and to sharpen my negative-rake scrapers. The 180- grit wheel produces a burr that is just right for negative-rake scraping. I use my 350-grit wheel to sharpen gouges used for rough-shaping platters and bowls, and I use the 600-grit wheel for sharpening gouges used for finishing cuts, where a smooth surface with no tearout is essential. If I had only one grinder, I would choose 180- and 600- grit CBN wheels.
A Note About Heat Treatment of Steel
All woodturning tools must be heat-treated in order to fully develop the microstructure of the steel to yield its desired characteristics of hardness, toughness, and resistance to wear. During heat treatment, tools are heated in a furnace to a precise temperature, then quenched to rapidly lower the temperature of the steel to make it hard. Cryogenic treatment is sometimes employed in the quenching process. Tools are then tempered to reduce stresses in the hardened steel, enhancing toughness and resistance to shock. No matter how good the steel, if tools are not heat-treated using accurately controlled processes, tools will not perform effectively. A full description of heat treatment processes is quite involved and too lengthy for inclusion in this article.
Conclusion
If you have M2 tools, continue to use them proudly. M2 has been the most successful steel for woodturning tools for many years. But when it’s time to buy new tools, take advantage of developments in modern tool steels. And with CBN grinding wheels, you can get particle-metal tools every bit as sharp as conventional HSS tools, and they stay sharp longer. Invest in CBN grinding wheels as soon as your budget allows. And consider getting at least one very fine-grit CBN wheel to grind gouges used for finishing cuts. A dull tool will always produce tearout, always! The sharper the tool, the better it will perform. Fine-grit CBN wheels produce superior grinds. Modern woodturners should take advantage of evolving technologies in tool steels and grinders.
Tom Wirsing is a physicist who has had a lifelong interest in metallurgy and woodturning. He enjoys teaching woodturning and has taught at regional and national symposia, as well as at numerous AAW chapter events across the U.S. and Canada. Tom is a past president of the AAW. For more, visit thomaswirsing.com.