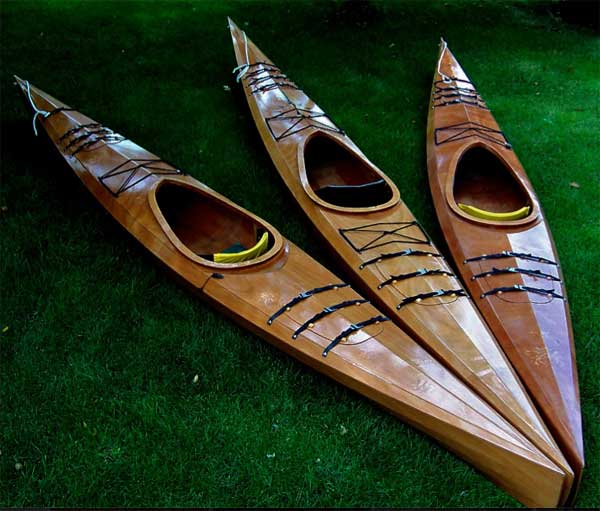
Mike Pfeifer has always been handy, and has always been interested in expressing his creativity. Those factors mattered when, about 25 years ago, he and his wife had their first child. Mike, they determined, could do woodworking from home while his wife climbed the corporate ladder.
He’s been running his woodworking business ever since, and is still operating out of a three-stall heated garage – one-third of which is currently taken up with his son’s Volkswagen restoration project. (For a brief time following the Ronald Reagan-era air traffic controllers strike, Mike considered being an air traffic controller – but didn’t make it all the way through the screening process).
His woodworking, and his business, grew out of experiences in high school shop classes, college summer jobs in house construction and, as for many woodworkers, an inability to afford good furniture early in his marriage.
“I’ve always been a handy guy,” he said. “When we were newlyweds, we couldn’t afford the furniture we wanted, so we’d go and look at furniture and then I’d come home and make exact replicas. Then the neighbors found out I could do woodworking, and it rippled out.”
Some of his early projects were creating shipping crates for a company Mike had previously worked for, which created 6 feet high by 16 feet long food pictures for grocery stores. It was hard to find containers to ship those in, so Mike made custom size crates, “hundreds and hundreds of these for that company. It was my bread and butter for years.”
These days, he’s branched out into a little bit of everything – whatever people ask him to make. “I don’t make stuff on spec,” he said. “I talk to clients and tell ‘em to flip through magazines or look online. The more information you can put into my head, the more likely it is I’m going to be able to make what you wanted. I tell clients, ‘If you can think of it, I can make it.’”
His current workload extends six months out; the last three projects have been bathroom vanities. Those projects were made of paint-grade lumber, like pine or yellow poplar, but even when working with woods like yellow poplar, Mike said, he’ll sometimes find pieces with interesting colors. He’ll save those pieces of wood and make small boxes from them.
For the most part, Mike works with fairly common domestic woods: oak, maple, cherry, walnut. “Because oak is so common around here [in Minnesota], I really don’t care to work with oak that much, but I still do. My favorite is cherry,” he said.
One of his most memorable projects was made of cherry, from a board his dad had given him which originally came from his sister’s place in Indiana. It was used to create a box for the ashes of a client’s husband. The woman and her mother came to Mike seeking something more personal than the commercially available containers and, after he finished the project, they both gave him a hug. “They were both crying, but I think they were happy,” he said.
That, and a Rangeley rowboat he built based on a chapter from Building Classic Small Craft by John Gardner are probably Mike’s most memorable projects. The Rangeley was fashioned after a type of boat originally manufactured in Maine during the late 1800s and early 1900s for a fisherman and his guide. Mike said the lines for the boat he made were slightly different from the historical model, because he incorporated lines from around 1908, just when outboard motors were coming into play.
The boat is made with lapstrake construction, with 4,000 copper rivets, every one of which Mike put in by hand. “It turned out beautiful,” Mike said. “It was a learning process, but it still turned out pretty dingdang nice.”
He has also made nine kayaks with kits from Pygmy Boats. Mike is on Pygmy’s builder’s list and says other people making boats from those kits have called to ask him questions, since he has so much experience, or to ask him to build a boat for them. “The book says it will take you 70 to 90 hours to build one, but I can do one now in about 30 to 40 hours, because I’ve done so many. I tell people that if you can tie your own shoes, you can make one of these boats.”
Mike enjoys doing inlay, and has included that feature on all nine of the kayaks he’s made. He’s also a kayaker himself.
“If I had my druthers, if I could, I would love to make wooden boats for a living,” Mike said, but, “Some projects you do just for the money, and some for fun. ”