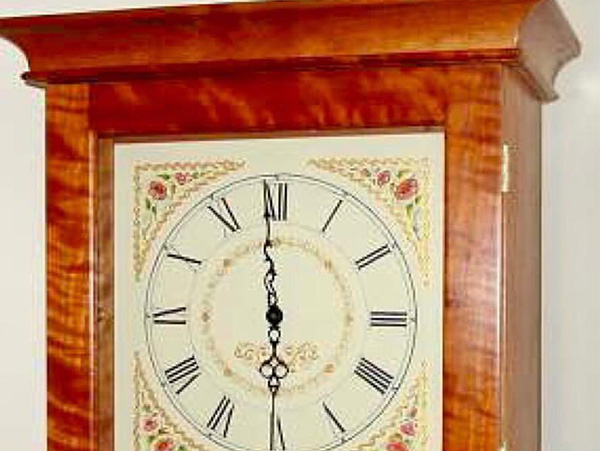
It all started at a lumberyard. Mike Lynch found a piece of cherry with beautiful figuring. He bought it, took it home, but didn’t know what he was going to do with it. So it sat in his basement in Charlestown, Rhode Island, for the next five years.
Flash forward to today, and Mike has transformed that piece (and a few others) into a beautiful cherry tall clock. Even more dramatic, over that same time period, Mike has transformed himself from an hobbyist woodworker into a professional. Shortly after he bought the cherry, he walked into Zuckermann Harpsichords International and — with just a few snapshots of the hobby pieces he’d made for his home and family — was hired as a woodworker. It was just the change he needed from his previous career where he spent 18 years as a meat cutter!
“I spent so many years taking things apart,” Mike joked, “that I decided to put things together for a change.”
Zuckermann, located in Stonington, Connecticut, is know worldwide for their musical instruments – sold finished or as kits. But they also own another business, Village Woodwright, and that’s where Mike first worked for them as an antique restorer. In the process, he got a real education in past construction techniques.
“It was fascinating to see how a 200-year-old chest of drawers was made,” Mike recalled. “And you never know what you’re going to have to do next. I might have to figure out how to carve a missing piece of molding or repair a veneer. I did lots of research in woodworking magazines and books at the library.”
With experience came confidence – which Mike believes is the key to moving from amateur to professional. Plus he got plenty of advice from his workmates who were happy to stop and answer his questions.
Which brings us back to that piece of cherry – Mike decided he was ready to do something with it. Inspiration arrived when a few antique clocks come into the restoration shop. As he thought about the clock that he’d like to make, he noticed something interesting about one of the old clock’s dimensions. Excluding the feet, the top piece was the same dimension as the bottom. Mike incorporated the feature into his design, along with ideas from several Shaker-style clocks.
Once the design was complete, Mike set to work in his home shop – equipped with an 8″ joiner, DeWalt planer, JET 14″ bandsaw, and lots of hand tools. Each step presented a new challenge. He didn’t have a lot of the figured cherry. To get as much as possible out of it he carefully sliced the inch-thick piece into 3/8″ inch boards. When it came to creating the cove molding, Mike faced a dilemma. Traditionally, furniture makers used a pine backer behind a relatively small amount of hardwood for coves. Deciding to buck that tradition, Mike decided to make his cove out of solid cherry. Among some old planes he’d been collecting was a cove-molding plane. It was still in pretty good shape and just needed a little sharpening. Uncertain how it would work, Mike began using it on his cove stock.
“It was kind of cool,” Mike recalled. “The shaving were going all over the place and before long it really started to look like the cove I wanted. When I finished it didn’t turn out exactly uniform like machine cut, but had a wonderful homemade look. I was really happy with the way it turned out.”
The clock was finished with Minwax Antique Oil, although sunlight has played a key role in darkening the piece. The clockworks are from Germany, and a co-worker painted the face.
Mike’s latest home shop purchase was a Delta Unisaw, and his next project sounds interesting: a rooster-shaped rocking chair based on a family antique. But whether he’s working for his own pleasure at home or at work, Mike Lynch considers himself a very lucky man.