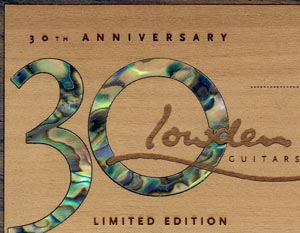
When word came of the disastrous fire at the Gurian Guitar plant, a lot of fellow guitar makers felt something more than mere sympathy. After all, Michael Gurian was an icon in the rebirth of the fledgling handmade guitar field. But like the legendary phoenix, he, too, was destined to rise from the ashes.
The late 1960s and early 1970s ushered in a renewed interest in arts and crafts, specifically woodworking. With it came the then-radical idea that individuals could build not only furniture, but guitars as well. For many, myself included, Michael Gurian provided both the inspiration and the model for us to take our first tentative steps into building handmade acoustic guitars not merely as a hobby, but as a life’s work.
To this day, much of what is now seen as the “old guard” of handmade guitar makers regards Gurian as a trailblazer and mentor. A surprising number of well-known custom guitar makers got their start either working for him or studying under his former employees. Just about all of us learned techniques from Michael, and were also regular customers of the specialized tools, bindings, fittings and inlays that he sold. They made it vastly easier for us to create beautiful instruments in small, often poorly equipped, hole-in-the-wall shops. He’s still at it, continuing on the West Coast with a tale that began back East in the 1960s.
“I graduated as an art major from university,” Michael recounted to me, “but while I was still in school, I got involved in both building guitars and working in a furniture shop. In 1965, I opened a lutherie (guitar making) shop in lower Manhattan. It started as a one-person shop with paid apprentices, which in essence means they were employees. We eventually expanded to two shops in New York City building lutes, guitars and ouds (a lute-like Arabic instrument), and doing repair work. By 1971, I moved the business into a 35,000 square foot building in Hinsdale, New Hampshire after the state offered us perks to locate there.
“Over time, we made about five thousand Gurian Guitars. They were quite well respected, and are still very sought after if you can find one. The label, itself a piece of 70’s period curiosity, said on it: ‘Gurian Guitars, Earth, Third planet from the Sun.’
“In 1976, we bought another piece of property, built a sawmill, and started wholesale wood sales to the furniture and music industries. We supplied Steinway, Martin Archery, a bow maker, many guitar making companies such as Martin and Gibson, and a host of wood retailers and furniture makers. We also had a mail order company selling wood and parts for musical instruments, and many emerging guitar makers bought from us. All told, we had about 75 employees, and developed a substantial reputation.
“In 1979, the main guitar plant burned down in a major fire. Part of the problem was that the town did not have enough water to supply our sprinkler system, and the fire trucks could not get water when they arrived. Eventually they hooked up lines to the river, but it was too little, too late. We had two insurance policies, but one of the insurers skipped town with the paperwork and did not pay off. Nevertheless, six months later we had built a new plant in a nearby town and were up and running again. However, we closed the doors for good in 1982, partly because of my health problems and partly because of the recession, which just about destroyed the guitar market.
“With the company closed, I did some film work and architectural work independently, and opened a small company called Gurian Instruments to make parts for musical instruments to sell to other makers. The company grew and relocated; I took on one employee and moved to Seattle in 1992. It was time for a change, and along with the change in venue came upgrades. We bought our first laser and started doing more computer design work and custom work for customers.
“Here in Seattle, we endured two earthquakes and got ‘gentrified’ out of our loft. We couldn’t find a new place to rent, which resulted in some creative thinking. The solution was on the water. I bought a 115-foot-long, 40-foot-wide barge and built a three-story shop on it. The shop address was now a marina slip, and the prospect of being forced to move, which in fact happened again due to waterside gentrification, became much less daunting.
“Moving day, which happens now and then, is frightfully easy. The tools stay bolted down. All you do is disconnect the power and water, get towed to the new marina or slip, and hook up again. On our last move we were only down for one day, and once we started up, everything was still in its place. We did not even have to take anything off the shelves.
“We now have 11 employees and a bunch of modern new equipment. Because of our location, we do a lot of marine work, making fancy backlit custom panels of figured woods. We offer architectural woodworking companies and furniture makers custom wood parts, turnings, inlay strips, stringers, banding and marquetry scenes with both shell and wood. We also do laser engraving in wood, glass and stone that gets incorporated into tables, built-ins and so on. Because we work in a lot of different materials, we can do everything from Old World woodworking to the most modern alternatives.
“We’ve done grills, laser- and CNC-engraved doors, barrettes, combs, coasters, conference tables, dollhouse furniture, architectural models, letter openers, ornaments and even key chains. In short, we can make just about any sort of inlay or part you can dream up. We’re a one-stop shop for fancy inlay and furniture decoration.
“Our biggest market is still the music industry, and we sell all over the world. For them, we make bridge and end pins, headstocks, purfling, pickguards, pickup bobbins, bullwinkles, jigs, fret files, knobs, backstrips, bindings, heel caps, rosettes and many other specialty items. Our customers include Martin, Gibson, Taylor, Fender, Santa Cruz, Ramirez, Collings, Larrivee, Kamaka Ukes and others.
“On the furniture side, we sell through Rockler and other woodworking specialty stores, and direct to woodworkers through our website. At this point, we are pretty much the only company that can do unique custom work on this scale for the marine, architectural woodworking, furniture and guitar fields.
“Our equipment includes three lasers, two CNC turning centers, a four-head CNC machine center (similar to a vertical mill) two centerless grinders, a full pressing room for laying up laminates and a wealth of custom machinery that I designed and built. There’s one homemade machine that fabricates, inlays, slots and polishes guitar bridge pins. We even have special heated presses and high production tooling that works with heat-activated glue for fast construction of complex parts and assemblages, such as guitar rosettes. Of course, there’s a full machine shop on the barge as well, and a mill room for woodworking with all the typical heavy woodworking machinery you would see in any land-bound shop. We even grind and maintain our own cutting blades.
“What is most important, though, is that we take care of our customers properly. I have customers who have been buying from me for over 40 years. That’s got to tell you something.”