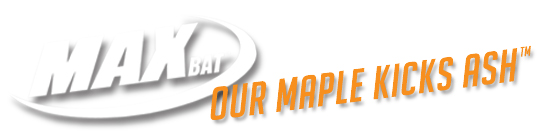
MaxBat started with the love of baseball and the imminent arrival of Jim Anderson’s first child. Today the company makes Major League Baseball approved bats in Minneapolis, Minnesota. They come in a range of colors with various diameters and lengths. But back in 2000, the only thing Jim Anderson expected was to create one special baseball bat. Though a long-time woodworker, Jim had never turned a bat nor even owed a lathe.
“I’d always wanted to make a bat, and when Max was born it was kind of a catalyst to do it. My best friend Scott coaxed me to come out to Seattle to turn my first bat in December of 2000,” Jim recalled. “He had a lathe. I didn’t. It wasn’t the greatest bat, but it turned out okay. But once our son Max was born, the bat just sat around. I was waiting for my Dad to come to town to do calligraphy on the bat with Max’s birth statistics. In the meantime, people who came over to see Max noticed this bat and started to ask if I could make one for them. Things just started to transpire from there.”
To make a bat for his own use — he plays in St. Paul adult league — Jim bought a lathe. It was nothing fancy, just an inexpensive Central Machinery model, but he did splurge on a nice set of Robert Sorby knives. When he started using that bat at games, even the guys from the other teams wanted one. At the time, Jim was living in Minneapolis and working as a rep for a startup publishing company in Ohio. The economic downturn that followed 9/11, however, shut the company down. Thirty-four- years-old, a new father, suddenly without a job and with the new perspective that 9/11 gave him, Jim decided it was time to finally follow a dream.
“I knew it was crazy, but I didn’t want to look back when I turned 50 and wish I’d done this back then,” Jim noted. “I just thought ‘I’m going to take a chance on this, and I’m going to try to make baseball bats for a living.'”
MaxBat was born. It was good timing, coinciding with the ban on aluminum bats throughout Minnesota’s adult leagues. Unlike your standard Louisville Slugger, which is made of ash, Jim decided to make all of his bats of maple.
“I didn’t want to spend two hours making a bat out of ash and then have someone bust it in two or three swings.” Jim explained, “Maple is a harder wood, and it’s going to last longer than an ash bat.”
His next step was to contact Major League Baseball and get the rules and regulations for making bats. At one time, there were 48 companies making approved bats, ; now it’s down to only 14. To become one of them, Jim sent in his prototype. To his shock, his bat was not approved.
“I called up Major League Baseball, and they told me everything was perfect & but my logo was a quarter inch higher on the barrel then than it should have been,” Jim recalled. “I had two days to finish a half dozen more bats with the logo in the correct position and send them in. I was up all night.”
The new version was approved. It was an exciting moment, but it also kind of freaked Jim out as he did the math.
“I thought to myself, ‘now, there are how many teams in Major League Baseball, and how many players? How many minor league teams with how many players?’ Remember the UPS commercial where the company is just starting up and they click the Internet site to check the orders and it clicks one and they are excited, then suddenly they’ve got a hundred thousand orders? That is how I felt. I realized I couldn’t spend two hours making each bat in my basement.”
The other problem would be hand turning a half dozen identical bats for the serious player. Jim’s solution was to subcontract with a couple of Minnesota companies specializing in wood turning who could add some automation to the process. They’d reproduce his handmade models, and he would have no overhead or inventory to worry about. That freed Jim up to pursue marketing the bats to major and minor league players. And his first client was Joe Mauer, the Minnesota Twins’ #1 overall pick in the 2001 draft. Pretty good start!
Today, Jim works with a single vendor to turn his bats. He offers seven basic models in 12 colors and plans to come out with two more models before spring training. Of course, he will hand turn the prototypes and test them in the batting cage before they go into production. As long as they stay within MLB guidelines, individual bats can be ordered with different diameter handles and barrels and different lengths.
“I haven’t had many odd requests, although I recently had a request from someone in Australia wanting a 37″ bat, which is really big! And I made two bats for Dave Winfield last spring that were 35-1/2″ long, and those things were really monsters.”
After the Sammy Sosa incident, Dave got a request from FOX TV to cork a bat for them to use on TV. He really appreciated them thinking of him, but didn’t want that kind of publicity associated with his bats.
To fill in the gaps as the business grows, Jim took a full-time job selling advertising for a local newspaper. But the business remains a family affair. Jim’s wife Lori is a graphic designer and put together all the company’s brochures, flyers, and web content. Now three years old, Max helps pack each MaxBat and get it ready for shipment. And Jim’s old friend Scott, who helped him get started, is still a key adviser and Webmaster of the MaxBat web site. Jim sees the demand for wood bats increasing and sees MaxBat becoming a full-time job for him within three to five years. In the meantime, he’s thoroughly enjoying the business.
“There are other companies out there that make bats and are very “cutthroat” about it,” Jim noted. “But I never approached getting into this business to make a lot of money. I do it because I love woodworking and baseball. Making baseball bats is still fun for me, and if I have the time and someone wants a bat with slight modifications, I will personally do it for them. Of course they will pay a little extra for this service. But I love actually putting my hands on that piece of wood and daydreaming that the player who ordered it is getting a hit with it. So there is a bit of romance there.”