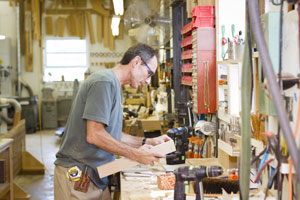
Masterpiece Woodworks, now operating out of an industrial park “within striking distance” of the city of Boston, had its origins over 30 years ago, when founders Daryl Evans and Rick Hulme were in high school industrial arts classes together. After graduating, Rick got a job as an apprentice to a craftsman of Italian heritage who was building custom furniture, and brought Daryl into the business as well.
“It was a place where you either learn, or you’re out the door,” Daryl said. “We learned a lot.” They worked for Mario for a while, then for his nephew, and “after several years, we decided we could do it on our own.”
Based on their experience, Daryl and Rick have always specialized in selling furniture wholesale to the interior design trade. “It keeps it on a professional level,” Daryl said. Plus, while he noted the technical requirements of woodworking, “you can do a lot of work, and if the design isn’t there, it just doesn’t look appropriate.”
A couple of recent built-in projects, for which they worked closely with the architect, involved a pair or armoires for a Boston brownstone foyer, and, for the same architect, a pair of crystal cabinets in a receiving room located between a dining room and living room. Of the armoires, Daryl said, “there wasn’t a straight line on the things, with the serpentine front. It was a lot of shaping, since they were fitted right to the walls, to mirror each other left and right.”
While the armoires were meant to take guests’ coats as they entered the home, the purpose of the crystal cabinets was for mixing and serving drinks. They had concave side panels of crotch mahogany, with marble tops at counter height for the service, and upper sections of curved, divided leaded glass. The cabinets were canted into the corners at a 30 degree angle.
While acknowledging the impressive factor of projects like that — and his appreciation that their high-end clientele has let Masterpiece Woodworks weather most recessions — Daryl said, “I’d rather just build freestanding stuff in the shop. It’s a little less stressful.”
The shop has six employees at this point: three builders (one of whom is Daryl), two finishers (Rick Hulme, the other founding partner, is in charge of the finish room) and one designer/office staff. Each builder gets assigned a specific project — or sometimes two if they’re small, such as coffee tables — with the assignments based on capabilities. For instance, one person is better at the lacquered linen wrapping that they sometimes do as a finish, while Daryl himself tends to do most of the cabinets with TV lifts.
Those are media cabinets in the style that accommodates the newer, thinner TVs, often with a motor lift mechanism that sometimes swivels. Speaking of traditional media centers, Daryl said, “Those deep cabinets, everybody retrofitted those cabinets or got rid of them — which was good for business.”
“Furniture is trendy,” Daryl said. “It’s like fashion, but a longer cycle.” While his shop still does some traditional pieces, “Right now, we’re doing a lot of contemporary pieces, pieces with clean, straight lines.” And some of the vintage type requests they get are for the sort of mid-century furniture which has lines that can work with a modern interior. The goal nowadays, Daryl said, is to create a certain shape or silhouette. That doesn’t mean it’s easier. “Simple lines can be more difficult,” he said. “There’s a reason for tradition: they’d put layers of molding over joinery to hide things.”
Other current trends include incorporating metal components into wood projects: things like metal feet for legs, hinges, etc. Masterpiece Woodworks works with a metal fabricator that “speaks the same language we do, the same quality of work,” Daryl said. Recently, they created their own metal guides out of aluminum to support the tracking system for the leaves of a 12′ long, 4′ wide dining table that extended to 20′ long with leaves on either end. The ends, Daryl said, had the appearance of breadboard ends. “So it was modern, but it had breadboard ends.”
Woods used by Masterpiece Woodworks include a lot of riftsawn oak and walnut, Daryl said. With the riftsawn oak, they often apply a ceruse finish — sometimes called liming — in which an overlay of color, usually white, fills and reveals grain lines. Withthe walnut, they will bleach it back to “a lighter wood that we can bleach and dye and stain.”
While finishing “is like a whole other trade, like chemistry,” that he himself doesn’t keep up with as much as the other aspects of woodworking, “finish is one of our shop’s assets,” Daryl said. Sheens and patinas can be critical in certain designs, and the shop has done finishes that incorporate a variety of materials, including parchment, glass, stone, and even shagreen finishes, made out of the calcium carbonate belly of a stingray.
“The finish is everything: ittells us what kind of material to use, what kind of joinery, what materials won’t crack the topcoat, the correct adhesive to secure it to the substrate…,” Daryl said. Taking those considerations into mind, “There’s more work upfront to a project,” he said. “Building it is almost secondary by the time we do all the shop drawings. We use a lot of mock-ups. We’ve got one shot to do it right, because every project is different.”
Most of the time, that work is being done in a 7,200 square foot shop. An addition about four years ago doubled the space, but about 1,000 feet is dedicated to office and showroom space, and “it’s never enough space,” Daryl said.
Tools found in that shop include two sliding panel saws — which Daryl described as “awesome” — a 36″ band saw, 16″ jointer, 24″ planer, Festool drills and more. What they don’t have, but is next on the list, according to Daryl, is a wide-belt sander. They also don’t have a CNC [computer numerically controlled] router — but a neighboring business is a sign fabricator with that capability, who works with them. “It works. I don’t have to spend 100 grand,” Daryl said. “But if I had one, I probably would use it more.”
Overall, Daryl said of Masterpiece Woodworks’ custom woodworking, “It’s a great business. It’s not the most lucrative business, but it’s certainly fun and interesting.” His advice for those thinking of getting started? “Take a business course. Business skills are important for anybody.”
And, as for himself? “It keeps it interesting because it’s always changing. It keeps the juices going.”