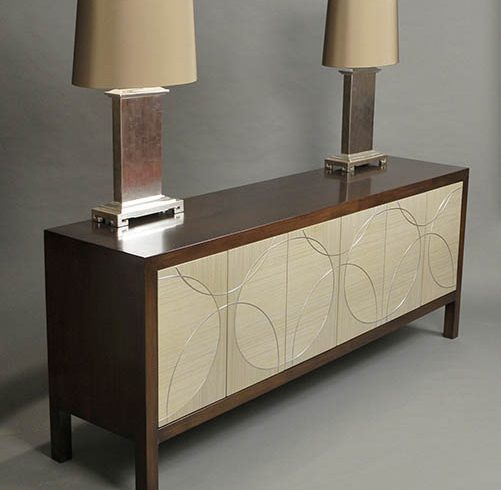
According to Mark Luedeman, “In truth, I’ve really only been woodworking, furniture building, for fewer than 10 years.”
Prior to that 2010 decision to focus on furniture, however, he did do quite a lot of building: shortly after he started out as a photography assistant in New York City in 1986, Mark’s employers discovered his ability to build props, sets and scenery. He found himself in that business for several years before moving to the Hudson Valley in 2003 and switching to custom interiors and custom built-ins. That wasn’t just about building the projects, but also about getting to know the clients. “It’s about improving their lives, the quality of their space. There’s something intangible beyond just building. The human side of it is just as important.”
Intangible aspects were also a big part of Mark’s decision to switch his focus to furniture. “As we get older, hopefully we’re getting closer to getting paid for what we really love to do. We’re not just taking jobs to pay the bills; we’re doing what we love and we’re rewarded for it. I love to do the furniture, and that’s really what I’ve been doing for the most part since 2010: furniture, furniture, furniture.”
Much of what he does, Mark maintains, “is just basic woodworking, basic joinery and assembly – but it’s the finishes and the veneering, I think, that really sets them off.”
Drawing on his background as a college biology and chemistry major, Mark spends a lot of time mixing finish colors to achieve the look he wants. Mostly, he works with dyes and stains to create a base color, which will then be covered with a clear topcoat of lacquer or catalyzed lacquer. “I don’t really want to put a lot of color in the clear coating; I want to get the color first and then seal it in,” he said.
“I end up sitting here making 30 different combinations of mahogany [dye or stain], literally, but just mixing in different parts of mahogany with different parts of walnut. It’s a record-keeping process: one part this, two parts that; three parts that, one part this, putting it down and taking it and finishing it. It’s kind of like creating a library: this combination makes this, and this combination makes that on various species.”
Playing with finishes, Mark said, is a way of expressing himself. For instance, he’s currently working on a piece for an upcoming show, a small lacquered cabinet “that’s basically a gloss school bus yellow. It’s just meant to be an eye-catcher.”
Mark also enjoys playing with veneer. “I like parquetry, and beyond just cutting strips of rectangles and straightedges, I’ve been playing a lot with pairing up two different species of veneer and doing a lot of curve cutting,” he said.
In the past few years, he’s also started to incorporate more metal into his work, starting at the design stage. “I think metal is kind of like the jewelry on a piece, especially when you put some handles on it,” he said. “It’s kind of like adding the jewelry after you’ve gotten dressed, the special little extra that goes on.”
His yellow cabinet, for example, “is begging for something interesting, so I’m going to design some handles for it. I’ve ben looking at Art Deco jewelry, believe it or not, for inspiration, especially when it comes to creating hardware for handles and things like that.”
Both Art Deco and Art Nouveau style are attractive to Mark, for different reasons. For Art Nouveau, it’s not the furniture – Mark says he’s “not crazy about [it], though I do love the organic form” – but the other items, such as lamps, jewelry, ceramics and glass, which he finds beautiful. As for Art Deco furniture, it’s what Mark considers somewhat of his fallback design style. “We look at Art Deco, and how many things get put into an Art Deco piece? Two elements? Three elements? It’s not a lot of bling-bling and clutter and so forth. It’s just simple, it’s elegant. That’s what attracts me.”
That doesn’t mean Mark is necessarily against ornamentation. “We’ve built all the furniture types that we’re probably every going to build – we’ve got chairs, we’ve got tables, we’ve got dressers – we’re not going to come up with too many new shapes, but what we will do is keep reinventing them and ornamenting them differently.” That’s what he was trying to do in a credenza piece which incorporates both black walnut, one of his favorite domestic woods, and koto, which he’s been using over the past couple of years.
Black walnut is a favorite, Mark said, for being so beautifully rich, while what he most appreciates about his other high-ranking domestic, white oak, is its versatility. “Just depending on cut alone, you can get three or four different options from the cut of wood, but then it can be light, it can be dark, it can just take on so many different characteristics. It can be fashioned into something that’s old-school; it can be very modern or chic. It’s just a really beautiful wood to play with.”
As for koto, typically a blond wood, “I’ve played with two bundles of it in the last couple of years. The first bundle was kind of this naturally oatmeal color with sort of a nickel metal cast to it, and it finishes it’s just a beautiful shimmer: it shimmers like mahogany. As for the second batch, used on the credenza, “It was a little grayer, almost too gray for my liking for the piece, and so I ended up giving it just a light khaki green wash, and I’m contrasting it against the black walnut,” Mark said.
The walnut credenza, he explained, wraps around and frames six doors made of koto, with grain going in two directions. He also routed out many of the seams where the koto joins its complement and filled them with polished aluminum stripping in a circular and oval wave pattern. “It was a little bit scary, because I’m handholding a router against a jig, and if you slip, you’re screwed. You don’t want to make a mistake, and you want to be very methodical. You do a step, and you stop, and you pause. You do another step, and you stop, and you pause.”
Most of Mark’s pieces like this are built with basic tools, with a heavy reliance on his table saw, router and miter saw. For sculpting art pieces, he uses a Dremel rotary tool and, for working with veneer, he has Quality Vakuum Products (see their profile page on Mark here). “I’m not one of those guys who has a lot of extra equipment. I don’t have a CNC machine. It’s pretty basic, but I do know how to use my equipment so I come up with some pretty interesting pieces based on what I have.”