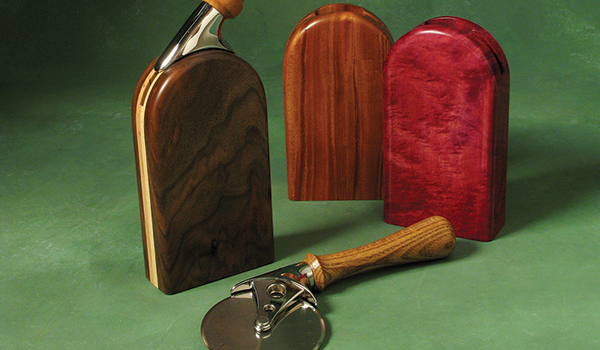
My decorative wooden blocks will store Rockler’s metal pizza cutter (item 34913) inside a form-fitting recess you can make with a special routing jig.
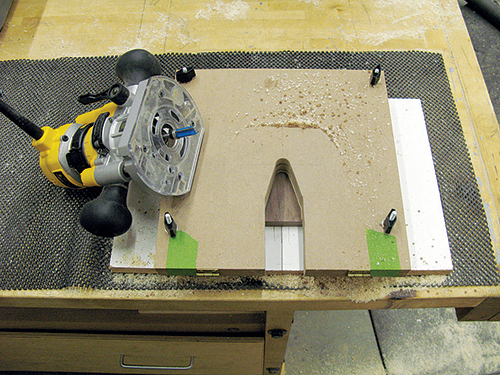
The jig consists of a base and four spring-loaded carriage bolts with knobs that hold two interchangeable routing templates. One template creates a round recess for the pizza cutter’s wheel, and the other template forms a ramp to cut a relief for the wheel’s tapered metal housing.
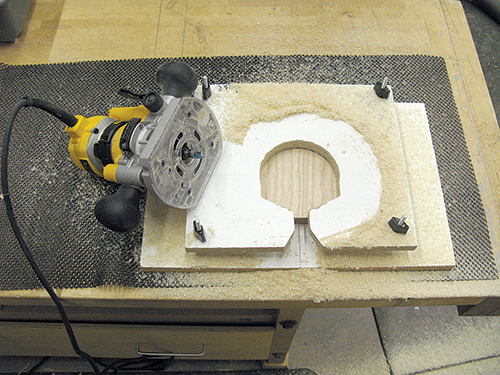
Build the jig base and two template assemblies from sheet stock as shown in the Drawings. I use springs on the carriage bolts to help push the templates up when the knobs are loosened, to make the block workpieces easier to slide in and out.
These blocks can be made from a single piece or multiple laminations. I start with a blank 4-1⁄2″ wide, 8″ long and about 2″ thick. Split your block through its thickness into two equal halves to prepare for routing. Mark a horizontal line 2-1⁄2″ from the top across the inside face of each block half so you can align it with either the 5-1⁄2″ or 4-3⁄8″ centerpoints on the two routing templates (see Drawings).
Routing the Cutter Recesses
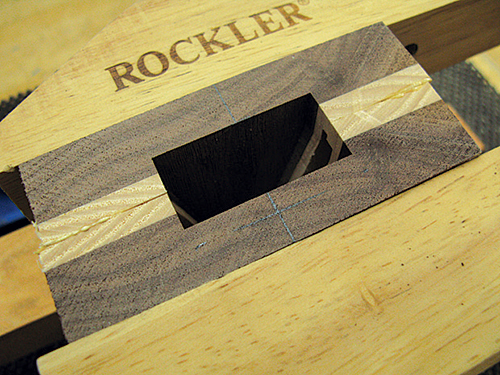
Start the routing process by installing the cutter template on the jig base, and clamp one of the block halves into place (the top of the block should face the router opening). Use a short 1/2″-diameter pattern bit to rout the circular cutter recess to a depth of 1/8″. Rout both blanks. Next, switch your jig to the hinged ramp routing template to mill the tapered wheel housing recess.
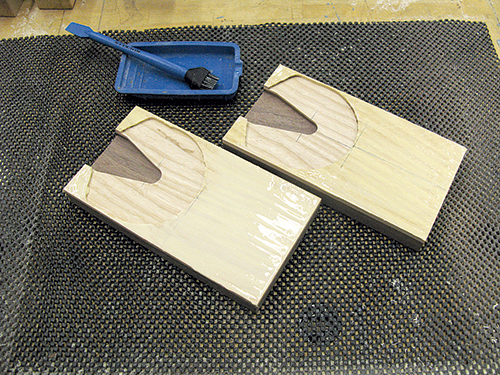
Slip three shims between the plates of this template to open it up to about 5/32″. Install a longer pattern-routing bit in your router, and set the depth to cut the top opening of this recess 15/32″ deep. As you rout, the cutting depth will decrease to about 21/64″ when you reach the tapered end of the recess, due to the effect of the hinged ramp. Rout this angled recess into both block halves to wrap up the pizza cutter recess. Now glue and clamp the block halves together.
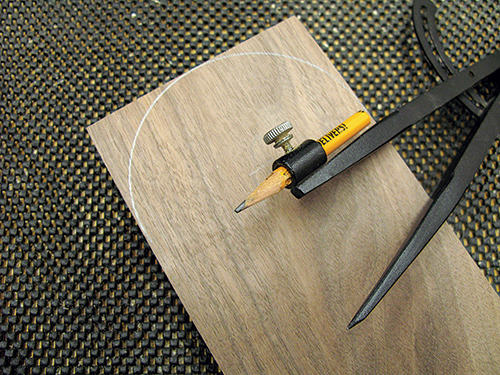
Mark the broad arch on top of the block with a compass, and band saw it along your layout line. If that doesn’t quite open up the long cutter slot, sand the arch farther until it does.
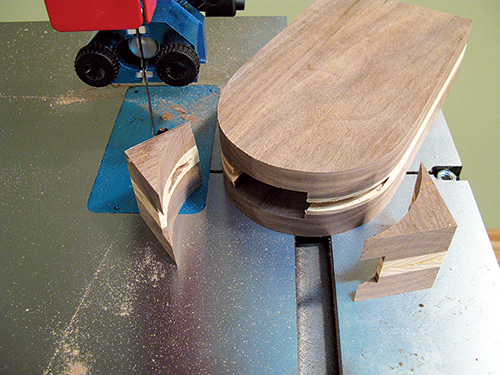
Insert the pizza cutter and check its fit, then continue sanding until the hardware nests nicely in the curve. Ease the sharp edges with a router and roundover bit.
Finishing Up
Give your block a thorough sanding. I finish mine with boiled linseed oil first, including flooding it into the recess and dumping it out. When the oil dries, apply a durable topcoat. These blocks make such great holiday gifts for others that my wife is still waiting for hers!
Click Here to Download the Drawings and Materials Lists.
Alan Vondran is a woodworker in Asbury, Iowa. His son’s girlfriend got the first pizza cutter block.