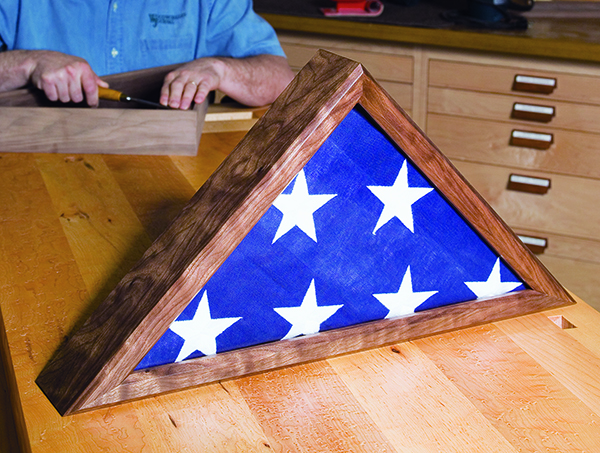
Those bottom corners may look impossible, but a simple tenoning jig and table saw setup make the work easy.
It’s tradition to drape an American flag over the casket of a deceased U.S. forces veteran. Prior to burial, the flag is removed, folded into a triangle and presented, “on behalf of a grateful Nation,” to the deceased veteran’s next of kin. I know this first hand because my father recently passed away, and our family was given his burial flag. My mother asked me to make her “a really nice case” for Dad’s flag. I responded without hesitation: “I’d be honored.” And even though this is an easy thing to build, I still put my heart into making it perfect, knowing how proud my father would have been with the results.
When my brother got wind of my making Dad’s flag case, he asked if I would make one for his father-in-law’s flag as well. So I made two out of walnut, and I used one board for each case. I ended up with one case having all dark and figured wood, and the other having all lighter, straight-grained wood. Both are beautiful!
Getting the Fit Right
I did a little research and found out that these flags are called burial or internment flags. When open, they measure 5′ x 9-1/2′. When folded, the height from the bottom center to the peak is approximately 10-1/2″, and the length across the bottom is twice the height, thus 21″ long. Those were also the inside dimensions given for “store-bought” cases. My flags seemed a bit larger than that, so I made a quick hot-glued-together mockup to assure myself of the fit. I didn’t bother with the 22-1/2° mitered ends yet; instead,I just 45° mitered the bottom ends of the sides and set them butt on a square-cut bottom. My flags fit really snug in the mockup, so I made another, this time 1/2″ taller. To my surprise, that was too big! One more mockup, this time just 1/4″ taller than the first, and fit was per fect. The final inside dimensions of my flag case became 21-1/2″ across the bottom, with a 10-3/4″ peak.
Adjusting dimensions for flag sizes
While it’s true that internment flags are all the same size, there are plenty of folks out there with a flag that isn’t flying anymore, but still has some special meaning to a family. Rather than fold it up in a box, a flag case like the one built here can become the perfect honored resting place for a treasured family heirloom. The Elevation Drawing at right shows you the formula to use to decide on your box dimensions. Remember, start with scrap wood and test the fit of your folded flag.
Cutting The Steep 22-1/2° Miters
In the meantime, while I was making my mockups, I’m thinking to myself… “How the heck am I going to cut those steep bottom miters?” After much experimentation, the solution hit me. If I set my table saw blade to 22-1/2°, and hold the workpieces upright, I can cut the angle I need. Now, what better tool is there to hold the pieces upright other than a tenoning jig! I tested the setup, and it worked great. The only drawback was that with my saw blade raised to its maximum of 3″, the widest front molding I could cut was 1-1/8″. You’ll need to check your maximum blade height and shrink the width of your front moldings as needed.

Build the Main Case
The main case consists of the bottom (piece 1) and the sides (pieces 2). Cut the sides to the dimensions given in the Materials List, adding one inch to the length. Using a miter saw, cut the top corner 45° mitered ends, then cut the sides to their finished lengths. Cut the bottom to its finished size. Set a bevel square to 22-1/2° and mark the bottom to side joints. Remove most of the waste with your band saw.
Now for the tenoning jig and table saw setup. Make sure your tenoning jig table and fence are aligned 90° to your saw’s table, and that the saw’s blade is tilted to 22-1/2°. As you can see in the photo on the previous page, I placed a 3/4″ thick spacer between the work piece and the tenoning jig’s table to keep the saw blade far away from the jig, and I screwed a backer board to the tenoning jig’s fence to reduce tearout at the rear of the cuts. I used a 1/8″ thick riser board, which rests on the saw’s table behind the blade and to the side of the tenoning jig. When you clamp your workpieces in the tenoning jig, you do so with them on top of the riser board, so the jig holds everything 1/8″ off of the saw’s table, and the wood can’t bind against the table as you saw.
Use scrap wood to test your table saw setup. Adjust the blade to tenoning jig distance so the cut makes a point on the end of the workpiece without reducing its length. Cut the ends of two scraps and check the combined angle to verify that it’s exactly 45°. Make any necessary adjustments, then finish cut the 22-1/2° miters.
Rout the rabbets for the back on the rear edges of the sides and bottom and then clamp the main case pieces together using band clamps. Make sure the top edges are flush at the corners.
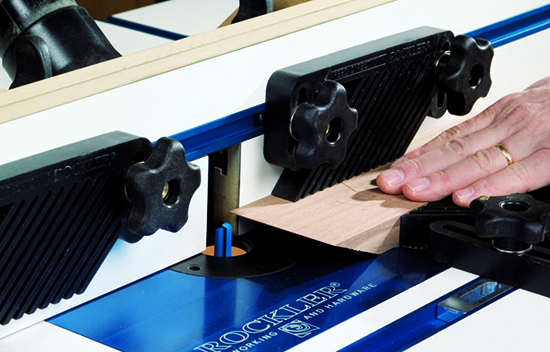
Make the Front Molding Frame
Make the front moldings (pieces 3 and 4) the same way you made the case sides and bottom. Cut the moldings 1/32″ longer, so when attached to the main case, their edges will overhang slightly. Covering the molding end faces with masking tape prior to cutting the 22-1/2° miters greatly reduces tearout. Use a router table and chamfer bit to rout the molding inside chamfers. Finish sand the chamfers and inside edges. Glue and band clamp the moldings together to make the frame. After that cures, glue and clamp the frame to the main case.
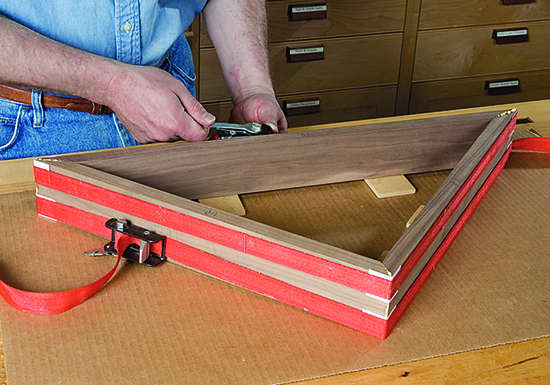
Do the Finish Work
You’re just about done… but there are a few more steps. Start by sanding the frame edges flush with the main case. Next, rout the frame outside chamfers and complete your finish sanding of the whole case. The final construction step is to make the back (piece 5), testing the fit as you go, to ensure a nice, tight fit.
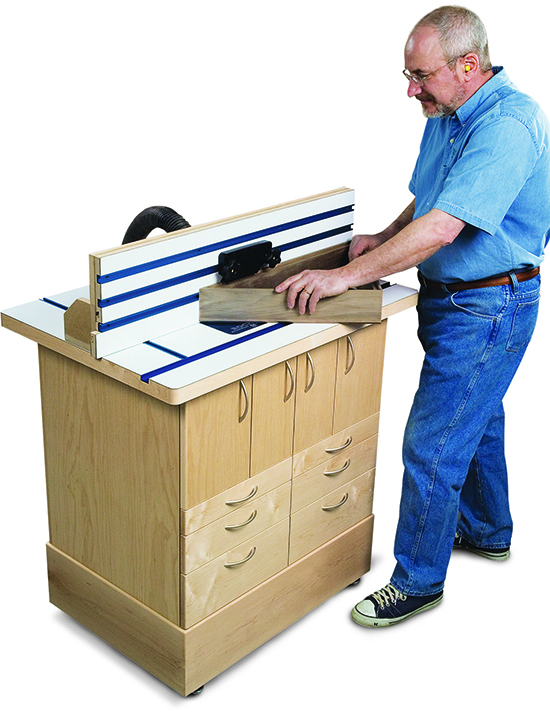
Finally, finish the case with three coats of clear stain spray lacquer. Take the case to your local glass supplier and have them fit the glass (piece 6). Set the glass in the case and affix it with a few dollops of clear silicon or hot glue. Add protective felt dots to the bottom, insert your flag, and attach the back. I can tell you right now, once you build one, there are probably a couple more in your future!
Bruce Kieffer is a professional woodworker and frequent contributor to the pages of Woodworker’s Journal.