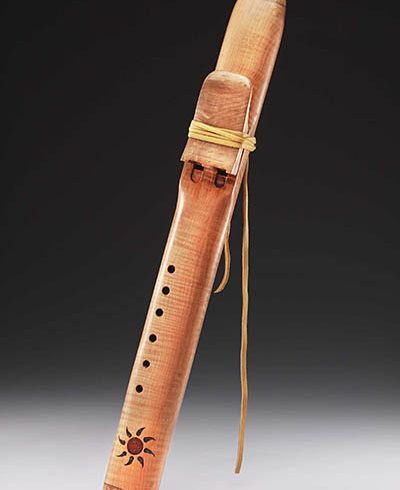
About 20 years ago, Lee Entrekin attended a music festival where he heard Geri Littlejohn play the flute. Lee said, “I just fell in love with the sound of it.”
Shortly after purchasing a flute from the performer, Lee decided to try making a flute, “just to see if I could. It didn’t seem all that complicated. The first one I made sounded OK. It wasn’t great, but it played. So I thought, ‘Well, I’ll make another one, and I’ll fiddle around with things and try to make it better – and it just kind of mushroomed.’”
Today, he makes about 120 to 125 flutes a year. Most are mid-size flutes in a popular key, pentatonic minor scale, “but there are always a few that I just enjoy spending time on and trying to produce something that’s a little more creative,” Lee said.
“The first flute I ever made was pretty much a copy of the flute that I bought from Hawk and Geri [Littlejohn]. I just took measurements from the flute,” he said. “And it’s pretty obvious, if you look at it, how it produces a sound, so what you learn is how to carve the sound hole to get the best sound, and, of course, where to put the finger holes for the tuning.”
For a while, Lee and a couple of other guys – including Dana Ross, who also went on to become a well-known flute maker – were meeting in each other’s shops, “floundering in the dark, trying this, and trying that,” to get a flute that sounded good, Lee said.
For his flute making process, Lee said, “Basically, I start with what would be a spindle, say an inch and a half square by 24 inches long. I cut it in half, I hollow out the center on a router table, and then I carve the sound hole. I glue the two halves back together and, at that point, I turn the flute, then tune it.”
Unlike some art turnings of bowl shapes, however, “A flute obviously has a function,” Lee said. “If you’re turning a bowl, you can have a lot more freedom as far as the shape. You can make it any shape you want, you can have voids in the wood – with a flute, to produce a sound, it has to have certain characteristics. The sound hole has to be in a certain place. If you’re going to tune it to a key, the sound chamber has to be a particular size. The finger holes have to be in a particular place for it to play a scale properly.”
That being said, “I could go in the shop and turn out a hundred mid-size flutes and it would be like clockwork. It would be very repetitive and easy to do,” Lee said. And, although those are the flutes that generally sell best, “It’s kind of boring to make the same thing over and over,” he added. “So, making the really small, almost pennywhistle size flutes, or some really big, deep flutes is more of a challenge because the fingering is a little harder to get.”
Although there are formulas used to determine the size of the board to get a given key and the location of the finger holes, “because of the hand work involved, the formulas are more like a rough template; they’re not something that you can follow absolutely without having to think much about it,” Lee said.
Generally, Lee said, he starts with a smaller hole and then enlarges it to bring the flute into tune. “As the flute gets bigger, the finger holes get farther apart, so at some point you get to a point where you have to be a professional basketball player to have hands large enough to reach the finger holes.” Some of the adjustments he makes involve the locations of the finger holes to make it possible for a person with average sized hands to play.
Sometimes, Lee gets commissions from musicians who might want a flute in a particular scale or with a particular tuning, but for the most part, specific requests mean that somebody either wants a flute in a particular key or made from a particular wood.
Most kinds of cedar work well for flutes, he said, as does “any wood that carves really smoothly.” He likes cherry, maple and redwood – “it’s one of the softest woods I work with, but it produces a really mellow sounding flute. I’ve made a number of flutes from old redwood that was recycled from decks and things like that.”
When it comes to exotics, he admits that some of the harder woods, like rosewood and bubinga, can be more difficult to work with when he does his handcarving, “but they do make a nice sounding flute.”
And, although he has made flutes from oak, “If I have a choice, I’m not going to use oak,” he said. The coarser, more porous woods can make it more difficult to achieve the specific shape of the sound hole and the necessary angles on the interior carvings.
In general, however, “trying to trying to combine different woods or slightly different shapes or carving or decorating on the body of the flute is really what I enjoy doing,” Lee said.
He has been adding woodburning decorations to his flutes since he began making them, because woodburning was something he had done before as a hobbyist. Last year, after taking a class at Arrowmont School of Arts and Crafts from Dixie Biggs, Lee has been inspired to add more carvings to his flutes: “leaves or other kinds of designs that stand out from the body of the flute, so it’s more of a relief type of carving and not just a surface design,” he explained.
Although he considers himself much more of a flute maker than a flute player, Lee has recently released a CD of his flute music. Partly, it was something he had always wanted to do. Partly, it gives him something to sell to those at shows who might not buy a flute.
It’s disappointing, Lee said, when people approach him at shows or during his demonstrations at the Southern Highland Craft Guild “and say how much they like the flutes and how great they sound, but then they’ll say, ‘but I don’t have a musical bone in my body.’ I hear over and over, ‘The only thing I can play is a radio.’ If I had a dollar for every time I’d heard that, I’d be rich.
“It’s kind of frustrating to me to have people who are kind of denying themselves the opportunity to learn to play. It’s not that hard to do, and I think I can teach just about anybody who is interested to play.”
The flip side of that experience is one of Lee’s greatest rewards in flute making. “One thing that’s really delightful about making flutes is having somebody come up and try to play one and realize they can play — so that’s a big reward for me.”