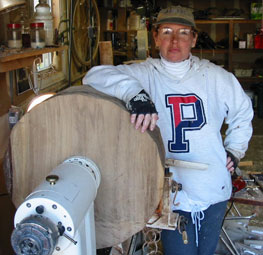
When an interesting tree goes down in Bucks County, Pennsylvania, folks have come to expect Jill Biros to stop by and ask if she can salvage some of it. As an accomplished woodturner, it’s Jill’s vocation and passion to uncover the wonderful bowl that may wait inside.
It all started around 11 years ago, when Jill bought a couple of turned bowls at a local craft show. Over the next couple of years, she often found herself wondering how they were made. Then in 1993, when she decided she wanted to do something more creative than her work in public relations, she came back to the bowls. She asked her son’s elementary art teacher if he knew anyone who could teach her to turn. The teacher, Jay Baldwin, suggested she look up Palmer Sharpless.
“I was hesitant as first,” recalled Jill. “Then I found a website for The American Association of Woodturners and they had a section on teachers. When I saw that Palmer Sharpless was listed as a teacher and was only 20 minutes from my house, I felt less bashful about calling him.”
Palmer, a nationally renowned turner, had taught woodworking for years and maintained a production turning business doing custom work for architects and homebuilders. When Jill phoned, he invited her to attend a turner’s club meeting that happened to be that very evening. Jill felt like a sore thumb, however, sticking out among the large group — around 80 — of mostly older men with only a sprinkling of women. Fortunately she found Palmer, and he put her at ease. Something about Jill’s quest to express her creativity in wood touched Palmer, and he offered to teach her about turning.
“It was intimidating initially and exhausting. I was scared of the large pieces of timber spinning around at a thousand RPMs,” Jill explained. “I had to learn which way the lathe turned and what the tools did. First, I just made chips, not even shapes. My first real project was turning a little bowl out of green wood … it’s easy cutting when you’re first learning.”
Soon, Jill discovered she’d made the right choice with woodturning and in finding the right teacher.
“If it hadn’t been for Palmer’s guidance I would never have stuck with it.”
Developing an intuitive woodturning ability, the craft has been a perfect fit for Jill and allowed her to stay closer to home and her two children. She described her learning curve as having three different phases: first, learning the craft and getting comfortable; second, having the freedom to be creative and play with the wood; and finally, the marketing or business aspect.
The second phase is obviously her favorite, and she explained the process she follows.
“I use green wood. It’s easier to work, and since I’m usually using recovered wood, it doesn’t cost anything,” Jill described. “My husband, Greg, is the silent, and probably harder working, partner in the business. Once we find a tree we want, he cuts the pieces into slabs with a chainsaw … avoiding the pith. Then we use a compass to make circles on the wood and begin laying out the bowls I’m going to make. The band saw then cuts them into round shapes.”
To create a rough bowl, she attaches what will become the opening of the bowl to her lathe using a screw center or for larger pieces, a faceplate. As she turns the outside shape, she also makes a tenon on the bottom of the piece. When she’s happy with the general outside shape, she flips it around and the tenon goes onto a chuck so she can work the inside of the bowl. When that’s done, her One-Way lathe has a device that holds the bowl so the base can be turned. Each piece takes about five hours. Then leaving the walls an inch thick, she waxes the bowl to slow the drying process and lets it sit for a year.
“You never know how they’ll dry,” Jill noted. “15% eventually crack or split. Just yesterday I threw three sweet little cherry pieces that didn’t make it into the fire pile.”
Jill uses a moisture meter to make sure they’re dry (about 12% moisture). There’s almost always, however, some movement in each piece as it dries, and it has to be re-trued, which means repeating the entire turning process again. Then, after what she described as “a ton of power and hand sanding.” she finishes the bowl, most often using Minwax® Antique Oil Finish.
She works with maple, cherry, and ash, sometimes walnut and box elder, and whatever her fellow woodturning club members share. (She thinks ash is the most forgiving and quick to sand.) Her bowls sell well, but the third phase, the business side, has proved to be the most challenging.
“A business head is different than a turning head,” Jill explained. “You have to figure out ways to keep your current customer base interested and ways to attract new customers. I have to keep my inventory pretty flush, because I never know when demand will be there. I do a handful of shows, all within an hour’s drive, but they are a whole ordeal unto themselves. The website has been good, but it has to be supported with other publicity.”
In fact, her work and business has been featured in the Philadelphia Inquirer and most significantly in Martha Stewart Living magazine. What comes across in the articles and in talking with Jill is her love for her craft.
“Woodturning gave me the ability to create. It’s always exciting, as the chips are flying, to unearth what’s underneath. It’s an immediate, instant gratification!”