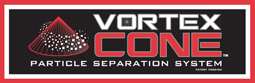
If you’ve spent much time researching and mulling over the best dust collector for your shop, you know the basic situation already. There are two options: single-stage and two-stage. Single-stage dust collectors draw all of the debris through an impeller and into a filtration bag or canister and a collection bag. It all swirls around inside the machine with no distinct separation of heavy and light debris. Single-stage machines are economical, but they can blast fine dust back into the air during operation. Or, the top filter packs with debris from the heavy chips, clogs up, and the efficiency drops off sharply. Neither separation nor fine filtration is something they do very well, but having one sure beats sweeping the floor. Two-stage dust collectors, on the other hand, “pre-separate” heavier particles into a collection bag or other container right away so only the finer dust makes it to the filter, where it can be filtered effectively. That leads to cleaner shop air, but at a significantly higher price for the machine. The twains between single-stage affordability and two-stage efficiency don’t really meet.
That is, until now. As of April 4, JET now offers single-stage dust-collectors with a patented new Vortex Cone Technology that “will start to approach the separation efficiency of two-stage dust collection,” says Barry Schwaiger, internal manager of woodworking machinery for JET. Even better, the new machines will be priced very close to what you currently pay for a conventional single-stage machine.
To get a clearer idea of how the new Vortex Cone system works, Schwaiger says the basic principles and physics of dust collection are similar to a tornado. Inside a tornado, there’s a low-pressure vacuum in the middle that draws debris up the column and violently expels it from the top. In a single-stage dust collector, the “tornado” effect spins the debris down and then forcefully up against the top filter before finally settling it in the collection bag. The impact of that heavy debris on the upper filter is where the problem lies.
“A couple of years ago, an Australian friend of mine named Robert Gregory and I were at a trade show turning single-stage dust collectors on and off. He’s extremely knowledgeable about dust collection systems. The two of us kept thinking, there’s just got to be a way to stop that violent updraft in the center that makes these machines so inefficient, and we challenged ourselves then and there to come up with an answer,” Schwaiger recalls. “Sometimes you don’t pick when and where innovation begins, but when a good concept comes along, you go with it fast and furious.”
The solution that resulted, after multiple prototypes and refinement, is elegantly simple: it’s a cone-shaped piece of metal fixed inside the machine between the upper filter and lower collection bag. As particulate enters the dust collector, the cone promotes a quick fallout of heavy debris down into the collection bag. Finer dust particulate still rises past the cone into the upper filter, similar to a two-stage system, where the filter separates it from cleaner exhaust air. “What Vortex Cone does, is eliminates the massive barrage of both large and small particles from going up into the filter without objection…It’s designed to stop the updraft without impeding the performance of the exiting air.”
Along with delivering cleaner air, Vortex Cone purportedly does a better job of packing the lower containment bag, so you’ll spend less time emptying it.
Schwaiger says the decision to develop better single-stage technology is right in keeping with JET’s commitment to dust collection in general. It’s been a strategic product category for the company for the past 10 to 15 years. “JET didn’t invent fine-filtration canisters for dust collectors, but we took them mainstream back in the early 2000s and have made them ubiquitous across the industry. We were the first to be known for the ability to clean these canisters conveniently using a system of internal baffles and an external handle. We were also the first to offer dust collectors with remote control.”
While the new Vortex Cone machines should not be confused with two-stage collectors — Barry says Vortex is still a “dirty fan” system — JET claims a 98 percent efficiency rating of particles captured. It’s a statistic that matches some current two-stage units and a dramatic improvement over conventional single-stage dust collectors without Vortex Cone. “Within the dust collection industry, you don’t even begin to talk about separation efficiency with conventional single-stage machines,” Barry comments.
JET’s launch of the new Vortex Cone dust collector line includes three 1-1/2HP (115-volt) models: two with either 30-micron or 5-micron cloth bags and one with a 2-micron canister filter and a heavy-duty lower plastic collection bag. These units are rated at 1,100 CFM and come with a wye adapter that accepts two 4-in. dust collector hoses. Prices range from $450 to $650. The company also offers three models of 1,200 CFM Vortex Cone dust collectors that are powered by 2HP, 230-volt motors. One model is single-phase, and the other two are three-phase; they’re outfitted with various 30-, 5- or 2-micron configurations of bags and canisters, with pricing between $500 to $700. Schwaiger adds that JET is not offering 650 CFM single-stage dust collectors with Vortex Cone Technology at this time.
Before wrapping up our interview, Schwaiger reminded me that powered dust collection is still a relatively new development for home shops. You don’t have to turn back the pages of time too far when it was still common to blow planer chips right onto the floor. Once single-stage collectors became commonplace, canister filtration made them better. “We feel that Vortex is the third step in this evolution toward cleaner air and better dust containment … a metal cone may seem like a small thing, but in single-stage collection, little changes done right can make really big improvements.”