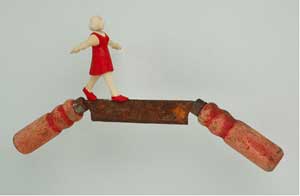
While Jessica Straus feels that woodworking must have been somehow in her blood – a grandfather she never met was a highly skilled amateur carver, and “apparently, I had a great-great-grandfather who was the last ‘sabot,’ or wooden shoemaker, in his village in France” – much of her own carving work comes from skills she taught herself.
“I envied those boys in junior high who got to take shop while I was stuck in home ec,” Jessica said. This may be why, when she was studying ceramics in art school, she also took a few trips over to the woodshop to seek some advice. Plus, after graduate school, she apprenticed for a year on a carpentry crew and learned how to use basic power tools.
The graduate degree was in ceramics, as was her undergraduate degree, and Jessica started out her career making large-scale clay sculptures – until she ran into some limitations. The sculptures were “a real hassle to fire, and I was not very excited about the glaze process or outcome,” Jessica said. “Someone suggested I try wood, and I took them up on that. I’ve never looked back!”
She’s not particular about using a particular wood, though: “Since I paint nearly all my surfaces, I’m not too concerned with the ‘beauty’ of the wood surface – I just want a nice, even grain, easy to carve, so I almost always use basswood.” It’s a wood that she received an introduction to from folk artist Garland Adkins, as part of a pilgrimage kind of trip Jessica took about 20 years ago. She traveled “5,000 miles of back roads through Appalachia, meeting folk and outsider artists along the way.”
Among those artists were Minnie and Garland Adkins and Denzil Goodpasture. “I was already a carver at that point, but I didn’t know about working with basswood,” Jessica said. “Garland put a big block in my car to take home with me. And Denzil inspired me to try my hand at walking sticks, like he did. I made about 20 of them in homage to each artist I met.”
It’s spheres, though, that Jessica thinks she has become known for. “I have carved hundreds and hundreds of spheres – I think by now others are starting to think of all those balls as a ‘trademark’ of mine, but really they’re just a current obsession.”
She describes herself, in fact, as “a pretty obsessive worker” – and one who is not interested in perfection. “In fact, I loathe perfect! It is very important to me, when I use a form like a sphere, that I carve it rather than buy a pre-existing and perfect sphere.”
Jessica also carves her own dowels instead of buying them, and tries to use pegging and friction fits for joinery rather than employing joining hardware. “Everything needs to have the mark of the maker’s hand – I guess that’s my signature. I love the warm, hand-hewn, tactile surface of the carved wood. (I leave the chip marks–I don’t like a sanded, overly smooth, slick look.)”
In fact, Jessica doesn’t even use a mallet and chiself for her carvings. Instead, after rough cutting her forms on a band saw, she switches to doing everything by hand with a small knife. “I guess a more accurate description for me would be a whittler,” she said. “That surprises some people, because sometimes my pieces are quite large, and most folks think of whittling being done only on a small scale.”
Right now, her big project is putting together a solo show for the Boston Sculptors Gallery this spring. “Every piece incorporates an antique glass bottle or bottles that a friend of mine excavated from urban rivers and ponds in the Boston area,” she said.
Like most of her work, this series incorporates painted wood. “I love the way the wood receives the paint that I apply to the finished work,” Jessica said. “I can let the paint sink in so it really impregnates the wood, or I can keep it on the surface by priming first.”
Jessica also appreciates the actual carving process. “I love the meditative process of chip carving wood. The process is slow, but I get a lot of thinking done while I’m carving!”