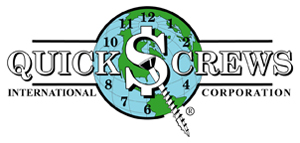
Quickscrews International’s founder Greg Wiener must be a believer in that old adage about a chain only being as strong as its weakest link. Because, for 27 years, he’s dedicated his career to studying and improving the quality of fasteners that are used in the woodworking and cabinetry industries. For projects to succeed, Wiener wants to make sure that the often under-appreciated but always important fasteners are doing their job. Even more, when he finds inferior examples, he sets out to redesign and improve them before offering them to his customers.
The need for quality control is important for the wood fastening industry, which uses more than 5 billion fasteners a year. That challenge only becomes greater when all of those screws are manufactured overseas; it’s been about 20 years since there has been a domestic producer of woodworking screws here in the United States, Wiener reports. In spite of these factors, however, quality standards within the fastener industry have continued to vary, depending on the requirements of the importer. The lack of standardization across the wood fastener industry has been an unacceptable fact of doing business for Greg, but it’s one he’s committed to changing.
He says that many years ago, Quickscrews contacted the Industrial Fasteners Institute (IFI), the major governing body of the fastener industry, in an effort to have them establish standards for wood fastener producers at large. They refused, claiming the industry was too small, but Greg thinks the reasoning is actually different: since there are no domestic producers of fasteners who are requesting standardization, why set a standard at all?
“It’s discouraging,” Wiener admits, “that the IFI refuses to acknowledge the need for uniform standards and specifications,” but he sees that shortsightedness as a call to action. “That’s why it’s incumbent among companies like Quickscrews to lead the way and publish and promote a set of standards and let the industry decide if they wish to choose them or not.”
In terms of producing the some 600 different woodworking fasteners Quickscrews sells, Wiener also believes it’s important to stick with the sources you trust. He’s used the same three overseas suppliers for fasteners for the past 25 years, and Quickscrews has designed and specified every product it purchases from them. “Our suppliers understand our desire to provide high quality woodworking screws,” Wiener says, “And we agree to pay for this quality. Our standards have been the same for 25 years … we guarantee our products against defects and will replace any product deemed defective at our costs.”
It might come as a surprise for those of us that use a limited number and type of screws, but Wiener says the wood fastening industry is far from static. The need for new and innovative fastening solutions is always on the rise. Much advancement has come about in the past couple of decades, such as screws that can self-countersink into even hardwoods without the need for a pilot hole. And the search for the ideal fastening solutions for composites like melamine, MDF and particleboard continue. Each of those materials requires a different fastener style.
“The biggest challenge over the past 27 years has been the continued introduction of different wood and manmade species used to produce cabinets and furniture and the unending introduction of hardware requiring different fasteners.”
Aside from staying abreast of new hardware and material developments, there’s also the opportunity to make inferior fasteners better. That brings about an interesting historical connection between Quickscrews and the now ubiquitous fastener most of us use: the pocket screw. We have Greg Wiener, Kreg Tools and the University of Iowa to thank for making casework and face frame assembly about as simple as it can possibly be using a drill, a jig and a deep-seated screw.
Wiener recalls that back in the mid 1990s, pocket screws weren’t what they are now. The problem was, the stress applied by driving a #2 square drive bit would cause the shanks to break under the screw heads. “In fact, those who purchased them expected them to snap. This was very difficult for me to accept,” he recalls. When Greg met Craig Sommerfeld, inventor of the Kreg Jig, the two began to work together in conjunction with Quickscrews’s overseas source and the U of I to redesign the screw head.
“The flat-top head design was born out of necessity, and that design is what you see on every square drive pocket-hole screw made today.”
Quickscrews has also innovated three other woodworking fasteners over the years that, by Greg’s estimation, have been game changers for certain segments of the woodworking industry. Quickscrews’s Undercut Head Hinge Screw (item 6057) was originally designed to solve a problem at Broyhill Furniture. The flat portion of the head of the original screws was causing wood to split above and below the hinge being attached. “They had two workers at the end of the line who would putty and sand the cracks,” Wiener recalls. His improvement in the screw design eliminated cracking from occurring and led to improved productivity at Broyhill.
The company’s QuickCutter Double T17 Thread screws (item 5443) have a thread design that allows them to be driven into dense wood like hickory or hard maple without the need to drill a pilot hole first. Similarly, Quickscrews Funnel Head screws (item 15451) also have a unique thread and point design that enable them to penetrate most types of wood and composite sheet materials without pre-drilling. The heads of these screws also have teeth underneath to cut a countersink.
For a company that offers more than 2,200 different products, and has sold more than 1 billion screws this fiscal year, you might be curious to learn what the top sellers are for woodworkers. Wiener says Quickscrews ships more #7 x 1-1/4-in. zinc-plated pocket screws than any other fastener — some 54 million this year. Its number two sellers are #6 x 5/8-in. drawer slide screws, followed by the workaday #8 x 1-1/4-in. flathead wood screw. He’s sold 35 million of that size alone this year.
That’s a mountain’s worth of screws for a relatively small company of 17 employees, but Wiener credits Quickscrews’s 20 percent growth rate over each of the past two years to two causes: his company has the largest and most complete fastener line in the industry, and his employees have a “deep understanding” of fastening to wood.
“These days, wood fastening knowledge is rare, but as long as companies like (ours) remain vibrant and dedicated to improving this industry, then the outlook for fastening in wood will look pretty good, too … Tell us what you’re building and what material you’re using, and we will most certainly have the right screw for you.”