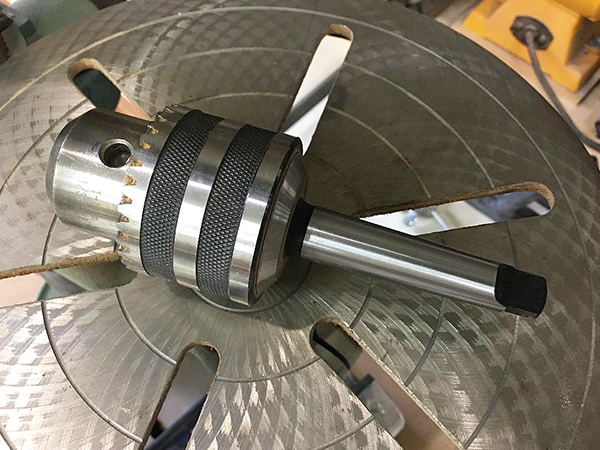
I enjoyed your Drill Press “Tool Tutorial” in the June 2019 issue of Woodworker’s Journal. I have a couple of additional questions about mine, though. My drill press uses a #2 Morse taper chuck arbor to mount the Jacobs chuck on the spindle. That adds flexibility in chuck choices I can share with my lathe. However, in applications involving vibration, such as drilling with spade bits or using sanding drums, the chuck’s arbor loosens and drops free, leading to a couple of questions. Should I keep the finish on the faces of the Morse taper polished, smooth or abraded? Should they be dry, lubricated with machine oil or is a temporary locking substance like Loctite® Threadlocker appropriate? – Robert Johnson
Tim Inman: A Morse taper is an engineering wonder of the world. When the tool is finely made, the surface contacts all along the length and diameter of the tapered fit. Way back when, I was required to learn how to machine a Morse taper on a lathe, and my grade was determined by the amount of surface contact my tool could make with the instructor’s master socket. How did he determine that? The same way you can test your tools right in your own shop. Get some Dykem® Steel Blue® Layout Fluid. If you don’t have that, you could just use a black magic marker. Color the tapered chuck arbor with the dye. Then, fit the arbor into the spindle socket. Don’t slam it home; insert the shaft gently and twist as you seat it. Remove the arbor and look for wear marks on the tapered shaft. They should be all along the length of the shaft. If you have a circle or two where the dye is worn off, that is where your problem is. GENTLY machine/sand down that wear mark and repeat. Do this until you have a shaft that fits closely all along the length of the taper. Do NOT rough up the shaft. Do not coat it. Make that shaft as smooth as possible. The magic of a tapered arbor shaft is the fit. Get that right, and you’re home and dry.
Chris Marshall: I have several drill presses in the shop, all of them having chucks installed with Morse taper-style arbors. They are polished smooth from the manufacturer, clean, dry and held in place with friction alone. (One of those is pictured in the top photo.) To add to what Tim has suggested, I’d also make sure that the inside of the tapered spindle on your drill press is absolutely clean and free from corrosion. When I remove a chuck to occasionally use it in the tail stock of my lathe, here’s how I re-install the arbor in the drill press again: I raise the table up and put a piece of scrap on it. I insert the arbor in the spindle, turn it some until it seats partially on its own and then just advance the spindle down (like drilling a normal hole) with the machine turned off and the jaws retracted inside the chuck. Then, when the chuck makes contact with the scrap on the table, I give the drill press handle a bit more of a pull downward to seat the arbor further in the spindle. That’s it. It stays put for any bit or accessory I need to use. Once you’ve checked/cleaned the contact surfaces, try installing your chuck’s arbor this way and see if it helps.