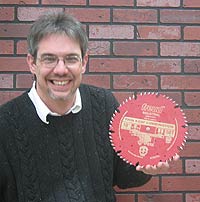
I have many years of experience using router bits and saw blades made by Freud TMM Inc. – their carbide-tipped saw blades and dado heads were prominent in my father’s cabinet shop. The Freud products have always proved to be of excellent quality and performed the tasks that I asked of them without complaint. (Even when the task at hand was not, perhaps, exactly what they were designed for.) Now, after an extensive tour of the Freud manufacturing facilities in Udine, Italy, I have a better understanding of why that is so.
The factory tour, hosted by owner Giorgio Pozzo and Freud USA’s Nino Ruggierio, Jim Brewer, Russel Kohl and Lisa Agostoni, impressed me. And while their gracious hospitality and the wonderful Italian cuisine and countryside were no hindrance to Freud’s cause, it was the remarkable level of sophistication demonstrated by their leading edge manufacturing innovation and rigorous quality control that struck me so strongly.
The tour began with a discussion of how super micro-grain carbide is produced. Yes, Freud makes their own carbide cutting material. In order to control quality, the company has developed its own “recipes” and processes to create specific carbide for specific cutting tasks. They want to achieve a finer grained and more homogenous product than is otherwise available, because these qualities produce sharper and longer-lasting cutting edges.
I had boned up a bit on carbide and its production before I went on the tour … so I would not seem such a numskull … but I left this session with a much deeper understanding of the subject. Freud has spared no expense with its technology in this area, either in manufacturing or in research. I looked through an electron microscope and watched a machine I think of as an “electro-radiologicalmorphographer” (not its real name), which refracts X-rays at any substance in order to identify and quantify what elements it is made of. Both machines are used to check and verify the quality of Freud’s carbide products and to benchmark the competitors. It was all very interesting to a tool geek like me. I left this aspect of the tour feeling that Freud had proved its argument that they indeed produce superior quality carbide.
Router bits and saw blades were next on our agenda. (OK … we shared a lovely meal first!) Freud’s proposition is that, while there are many bits and blades in the marketplace to choose from, the quality of the product they produce creates a value that is difficult to beat.
To help examine that claim, allow me to digress for a moment. The saw blades and router bits that Freud produces are designed by the same engineers who do their custom cutter designing. Freud’s historical strength is in the industrial market, making custom-machined cutters for multi-head molders that may have up to 60 different knives per machine; these can cost up to $80,000.00 a set. Giorgio compared this aspect of his business to an automobile maker’s racing team. The lessons learned at the “one-of” custom level of design are invaluable when applied to a production-made product.
When it comes to the manufacture of both their router bits and saw blades, the level of automation and robotics is simply remarkable. As I observed the various plants (which run three shifts a day, seven days a week), they appeared almost empty of people. But that is part of the plan. Each person is expected to run several CNC machines. An operator’s key responsibility in this process is quality control … not material handling. The precision accuracy inherent to automation , whether in the multiple-head laser cutting machines (which produce their saw blade blanks) or the hundreds of CNC grinders (which shape the router bits and sharpen the carbide cutting edges), is the key to Freud’s consistent high production quality. Also pointed out during our meetings were the “extra ” steps that Freud takes, such as forging the larger diameter router bit blanks and a “seating” grind on the saw blade blanks. These steps add quality, but may be overlooked by other manufacturers.
The main thing I took away from my time with Freud in Italy, in addition to the ten pounds I gained, was that quality and value are the key goals for Freud’s manufacturing process. The scope of their cutting tool line is broad, driven by customer demand and their ability to respond to it. The Freud router bits and blades I used years ago in my father’s shop are not the same products as those that are available today. The bits and blades made now are considerably better. So the next time you see a red saw blade or bit on the shelves of your local woodworking store, I hope you have a better understanding of what went into their construction. I know I sure do.