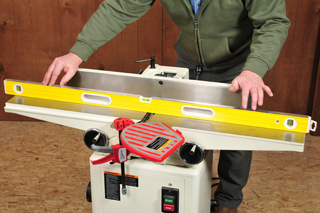
I reviewed Mr. Nagyszalanczy’s Skill Builder on Jointer Maintenance and found it extremely helpful. Now I have a couple of questions I would like to ask the staff and/or other readers. I have a 6″ Delta table top that I just received and have gone through the setup to make sure it is tuned up. Everything that I thought I could do, I did. My problem, and maybe it’s the beginner problem, is that when I try running the edge of a board to flatten it and square it with one side, I always end up with a taper. The leading part of the board begins to get smaller in height than the trailing edge. Am I applying too much pressure to the outfeed and not enough on the infeed table? I am working with scrap pieces that I have kept around and am using these as a means of learning. But I’m at a standstill. Any suggestions? – Lee Nalley
Sandor Nagyszalanczy: If all the boards you joint end with their leading ends significantly narrower than their trailing ends, then it’s likely one or both of your jointer’s tables droop: The outer end of the table is slightly lower than the middle part, next to the cutterhead. You can check this by first raising the jointer’s infeed table until it’s flush in height with the outfeed table (also make sure that the outfeed table is level with the cutterhead’s cutting circle). Lay a reliably straight carpenter’s level (or straightedge) across both tables. If the level won’t lay flat but rocks back and forth lengthwise, one or both tables are drooped at their ends. You can usually reduce or eliminate droop by adjusting the gibs that secure the tables to their sliding ways (for more information, see my Skillbuilder article from Woodworker’s Journal, June 2011 print issue that you referenced in your question).
If, on the other hand, the amount of taper in your jointed stock is slight and varies from board to board, it’s possible that the taper is simply due to inconsistencies in the edges of the boards themselves. The edge of a rough board is typically uneven and somewhat curved. If the concavity of the rough edge isn’t centered along the length, the jointer’s cutterhead may remove slightly more stock near one end than the other. To end up with jointed stock with parallel edges (the same width along its entire length), it’s always best to rip your stock to final width on the table saw after jointing. Of course, I’m assuming that you always joint boards with their concave edges facing down. Jointing a board convex edge down usually produces an edge that’s curved or wavy instead of straight.
Tim Inman: A jointer is a great tool, but it is a tool that reflects operator control. Unlike most wood surface planers, which grab a board and automatically control the cutting and feeding operation, a jointer requires a person to feed and control the cutting passes. People are not machines. Every pass can be different. I’m guessing your taper is probably the result of pressing hard at the beginning of the cut, and letting off as the cut — and your confidence — progresses.
Of course, it could be a mechanical problem, too. If the tables are “dished” toward the middle, you will get a taper. Lay a straightedge across your jointer. First, bring both tables up to level with each other. Then, check to be sure the straight edge is touching the far ends of each table. Now, check to see if there is any space under the straightedge near the middle, or near the cutterhead. There shouldn’t be any space. If you can slip a piece of paper under the straight edge, that’s too much.
Chris Marshall: As Sandor and Tim suggest, check for table parallelism, and keep practicing your machine technique. I remember when I started using a jointer that the unsettling feeling of passing a board over that big, spinning cutterhead made me bear down on it with all my might. Call it nervous overcompensating, and at times it made for poor results. A cupped board, for instance, remained cupped because I was pressing down so hard that the cup would just spring back after completing a pass. Now, I take a controlled but moderate approach to feed pressure: I try to keep it consistent on both infeed and outfeed sides of the cutterhead, letting the board present its shortcomings and allowing the jointer do the work it’s intended to do. I also keep my jointer set for very light passes and just make more of them to remove the deviations gradually.